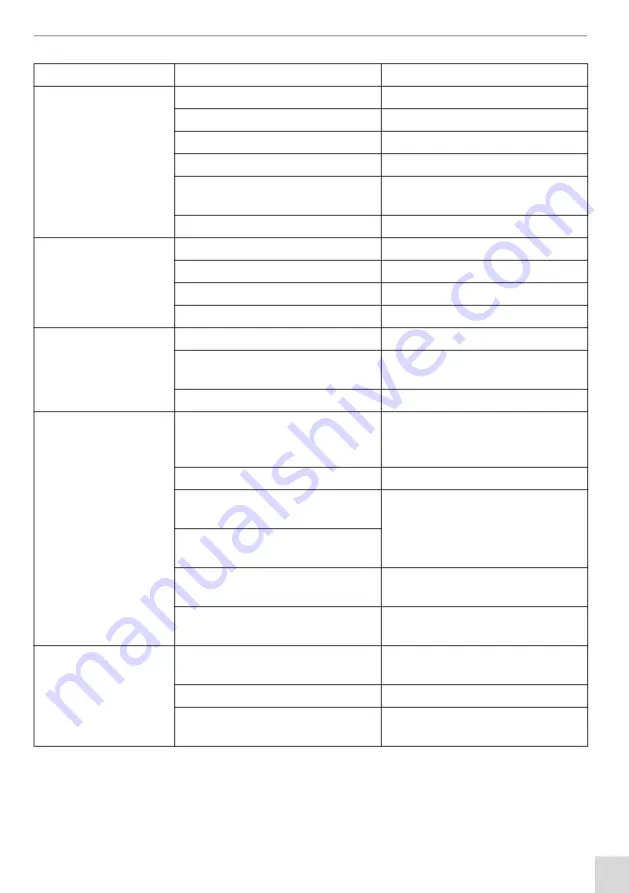
BAL.0716.0 • 2022-01-11
EN
-
29
ABIPLAS
®
CUT HF
10 Troubleshooting
Fault
Cause
Troubleshooting
Insufficient penetration
• Pressure drop during cutting
• Reset the pressure monitor
• Cutting rate too high
• Reduce the cutting rate
• Tilt angle of the torch too great
• Reduce the tilt angle
• Material thickness too high
• Use a lower material thickness
• Equipment parts worn or
damaged
• Replace the equipment parts
• Output not adjusted
• Adjust the output
Cutting arc breaks
• Cutting rate too low
• Increase the cutting rate
• Torch clearance too great
• Reduce the torch clearance
• Material thickness too high
• Use a lower material thickness
• Output too low
• Adjust the output
Excess dross formation
• Cutting rate too low or too high
• Adjust the cutting rate
• Equipment parts worn or
damaged
• Replace the equipment parts
• Output not adjusted
• Adjust the output
Cutting nozzle burned
out
• Damaged or loose nozzle
• Hand-tighten the nozzle or cap
body. Replace the nozzle if
necessary.
• Contact with the workpiece
• Avoid contact
• Start of cut at the edge of the
workpiece too fast
• Start cutting at a lower rate
• Too much spatter when punching
holes
• Pilot arc struck too long and too
frequently in the air
• Shorten/avoid ignitions in the air
if possible
• Pilot arc too strong (depends on
the power source)
• Set the pilot arc current to the
lowest possible value
Strong electrode burn-out
• Pressure drop while cutting due to
incorrectly set pressure monitor
• Correct the pressure monitor
setting
• Loose electrode
• Hand-tighten the electrode
• Pilot arc struck too long and too
frequently in the air
• Shorten/avoid ignitions in the air
if possible
Tab. 9
Troubleshooting