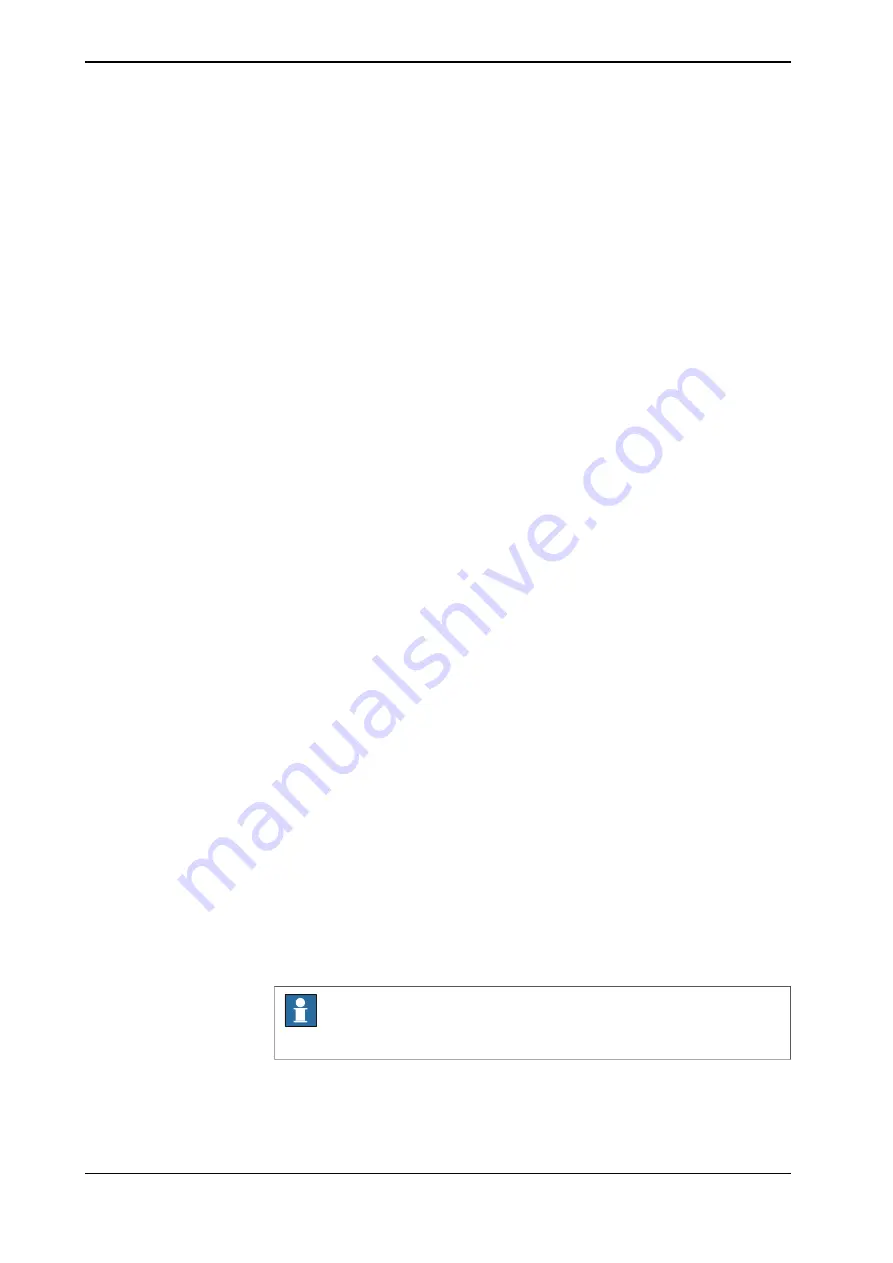
PrepareCalib.prg
(DSQC 2000 ) for this robot task (for example,
T_ROB1
), and select only this task for execution.
•
Start the loaded rapid program
-
Select calibration type: Conveyor.
-
Select conveyor: for example, CNV1.
-
Wait for the message
READY FOR CALIB
. The conveyor position
in the jogging window for CNV1 should now be displayed as “0”
mm.
3 Move the conveyor belt forward until the reference point is just inside the
working range of the next robot to calibrate.
The conveyor positions for all the conveyor work areas, in the jogging window
should indicate the same total travel distance for the reference point. The
nearest robot to the camera or sensor is calibrated first, followed by the next
nearest robot and so on until all the robots along the conveyor have been
calibrated.
4 Mount the calibration tool on the robot.
5 Open the Calibration window on the FlexPendant.
6 Select the conveyor, for example, CNV1.
7 Tap
Base Frame
.
8 Tap
4 Point
.
9 Select the robot, for example,
T_ROB1
.
This step is required for MultiMove robots.
10 Select the first point
Point 1
.
11 Jog or move the robot by hand. Point out the reference point on the conveyor
accurately with the calibration tool TCP.
12 Modify the selected point (
Point 1
) by tapping the
Modify Position
function
key.
13 Move the conveyor belt forward a distance where the reference point still
can be reached by the robot.
Long and equally spaced distances between the four calibration points (Point
1-4) are preferred since this increases the accuracy of the calibration.
14 Repeat the steps 10-13 for the points
Point 2
,
Point 3
, and
Point 4
.
15 Tap
OK
to calculate the base frame.
16 Check if the displayed mean error and max error of the base frame calculation
is acceptable. If the estimated error is acceptable, tap OK to confirm and
store the new base frame.
Note
A mean error of less than 1 mm is acceptable in most cases.
Continues on next page
192
Application manual - PickMaster® Twin - PowerPac
3HAC064218-001 Revision: B
© Copyright 2021 ABB. All rights reserved.
4 Working with PickMaster PowerPac
4.3.4.3 Defining the base frame (IRC5)
Continued
Содержание PickMaster Twin - PowerPac
Страница 1: ...ROBOTICS Application manual PickMaster Twin PowerPac ...
Страница 2: ...Trace back information Workspace Main version a394 Checked in 2021 03 25 Skribenta version 5 4 005 ...
Страница 8: ...This page is intentionally left blank ...
Страница 12: ...This page is intentionally left blank ...
Страница 16: ...This page is intentionally left blank ...
Страница 420: ...This page is intentionally left blank ...
Страница 444: ...This page is intentionally left blank ...
Страница 446: ...This page is intentionally left blank ...
Страница 448: ...This page is intentionally left blank ...
Страница 452: ......
Страница 453: ......