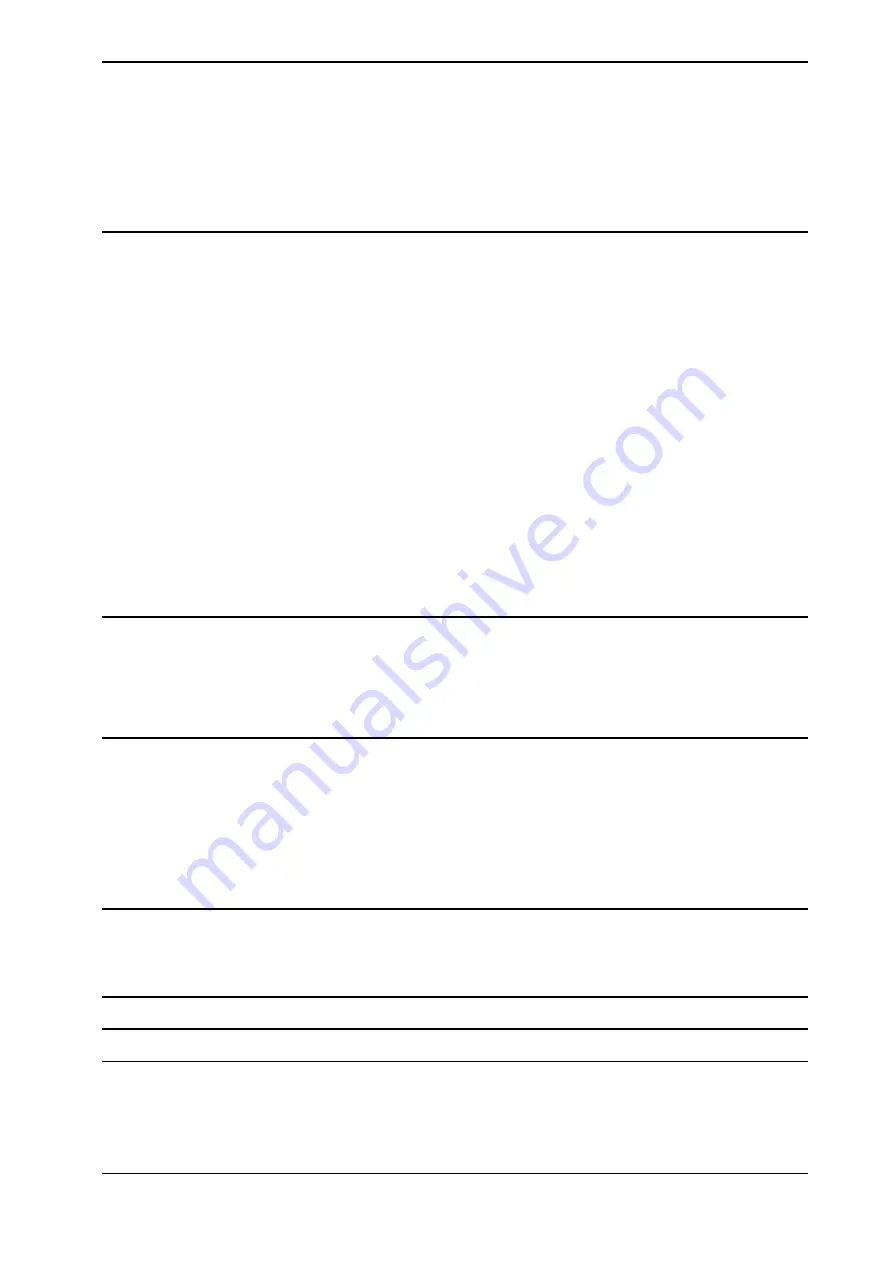
Table of contents
Protective stop and emergency stop ...........................................................
Make sure that the main power has been switched off ....................................
Safety risks during installation and service work on robots ..............................
Moving robots are potentially lethal ............................................................
First test run may cause injury or damage ....................................................
Work inside the working range of the robot ..................................................
Enabling device and hold-to-run functionality ...............................................
Risks associated with live electric parts .......................................................
The unit is sensitive to ESD .......................................................................
Hot parts may cause burns .......................................................................
1.3.11 Safety risks during work with gearbox lubricants (oil or grease) .......................
Safety signals in the manual ......................................................................
Safety symbols on product labels ...............................................................
Tuning the thermal supervision
Product manual - Motor Units and Gear Units
5
3HAC040148-001 Revision: K
© Copyright 2011 -2018 ABB. All rights reserved.
Table of contents
Содержание MID 1000
Страница 1: ...ROBOTICS Product manual Motor Units and Gear Units ...
Страница 2: ...Trace back information Workspace R18 2 version a15 Checked in 2018 10 30 Skribenta version 5 3 012 ...
Страница 10: ...This page is intentionally left blank ...
Страница 38: ...This page is intentionally left blank ...
Страница 68: ...This page is intentionally left blank ...
Страница 74: ...This page is intentionally left blank ...
Страница 86: ...This page is intentionally left blank ...
Страница 101: ......