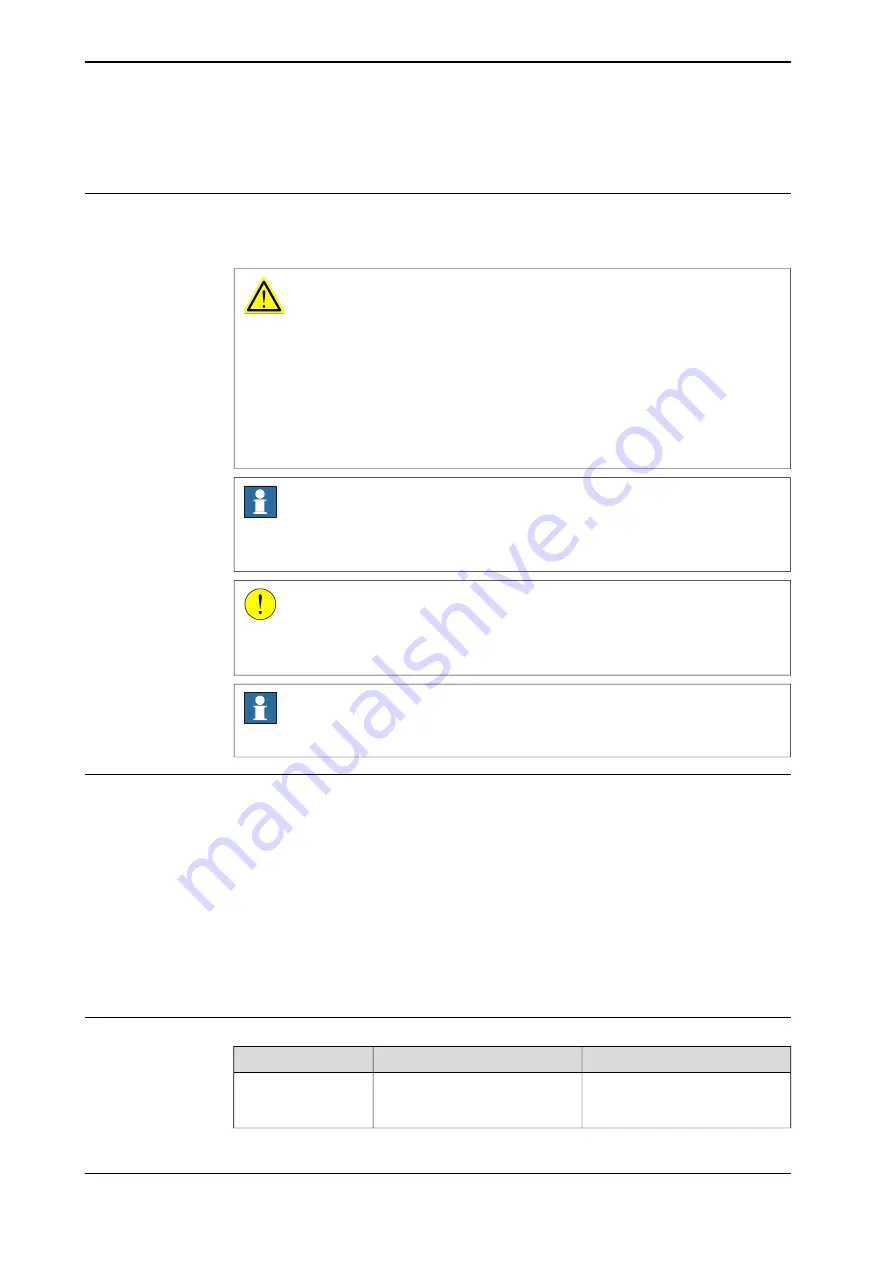
3.3.5 Bar system
General
This section describes maintenance on the bar system, with the intervals 500 and
4000 hours.
DANGER
Turn off all electrical power, hydraulic and pneumatic pressure supplies before
entering the workspace of the manipulator.
Also read the safety sections:
•
Pneumatic or hydraulic related hazards on page 32
•
•
Maintenance and repair on page 34
Note
The wear on the bearing rings depends on the payload, number of cycles, and
environment. Collisions can damage the bearing rings!
CAUTION
The spring units must be removed according to the description in section
Replacement of parallel arms on page 167
or they will be damaged.
Note
Never use grease on the bar system.
Different versions of bearing rings require different maintenance procedures
Valid for robot versions: IRB 360 - 1/1130, IRB 360 - 3/1130, IRB 360 - 1/800, IRB
360 - 1/1600.
At delivery the robot is equipped with bearing rings 3HAC028087-001. These are
maintenance free.
In specific environments the bearing rings 3HAC028087-001 might have been
changed to bearing rings 3HAC2091-1 after delivery. These must be lubricated
regularly.
The bearing rings 3HAC028087-001 are white. The bearing rings 3HAC2091-1 are
grey.
Required equipment and references
Note
Spare part no.
Required equipment
For article number see:
•
Spare parts - parallel arm
system, IRB 360
.
Bearing rings
Continues on next page
104
Product manual - IRB 360
3HAC030005-001 Revision: Z
© Copyright 2008-2021 ABB. All rights reserved.
3 Maintenance
3.3.5 Bar system
Содержание IRB 360
Страница 1: ...ROBOTICS Product manual IRB 360 ...
Страница 8: ...This page is intentionally left blank ...
Страница 266: ...This page is intentionally left blank ...
Страница 268: ...This page is intentionally left blank ...
Страница 271: ......