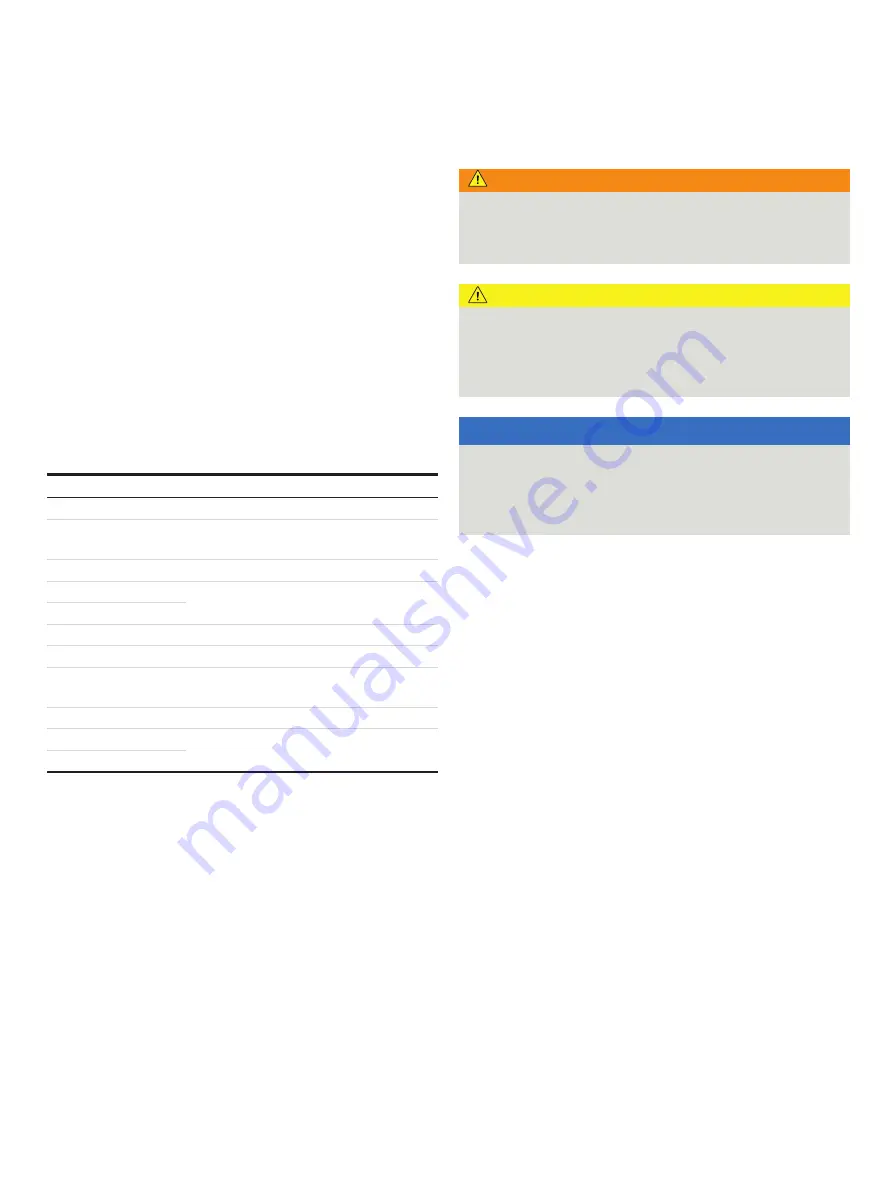
FEP630, FEH630
ELECTROMAGNETIC FLOWMETER | CI/FEP630/FEH630-EN REV. D
67
Verification
Fingerprint database
The sensor and transmitter fingerprint stored in the
SensorMemory allows you to compare the state of the device at
the time of manufacture at the factory with the current state of
the device at the customer site.
The check is started manually and returns a ‘successful / failed’
result.
If the verification is unsuccessful, troubleshooting information is
shown on the display (parameter ‘Rslt FP Verification‘).
A software tool (ABB Ability SRV500) is available for
documentation and trend analysis.
Setup
Menu / parameter
Description
Diagnostics / ...Diagnosis Control / ...Fingerprints
Tx Factory CMR, 1m/s,
10m/s
Display of transmitter fingerprint (factory
fingerprint)
Se Factory Coil Ind.
Display coil impedance fingerprint
Se Factory Imp. E1
Display electrode impedance fingerprint E1-GND,
E2-GND
Se Factory Imp.E2
Strt FP Verification
Start of test
Rslt FP Verification
Test result
Tx Customer CMR, 1m/s,
10m/s
Display of transmitter fingerprint (customer
fingerprint)
Se Customer Coil Ind
Display coil impedance fingerprint
Se Customer Imp. E1
Display electrode impedance fingerprint E1-GND,
E2-GND
Se Customer Imp. E2
8
Maintenance
Safety instructions
WARNING
Risk of injury due to live parts!
When the housing is open, contact protection is not provided
and EMC protection is limited.
• Before opening the housing, switch off the power supply.
CAUTION
Risk of burns due to hot measuring media
The device surface temperature may exceed 70 °C (158 °F),
depending on the measuring medium temperature!
• Before starting work on the device, make sure that it has
cooled sufficiently.
NOTICE
Damage to components!
The electronic components of the printed circuit board can be
damaged by static electricity (observe ESD guidelines).
• Make sure that the static electricity in your body is
discharged before touching electronic components.
Corrective maintenance work may only be performed by trained
personnel.
• Before removing the device, depressurize it along with any
adjacent lines or vessels.
• Check whether hazardous materials have been used as
measuring medium before opening the device. Residual
amounts of hazardous material may still be present in the
device and could escape when it is opened.
Within the scope of operator responsibility, check the following
as part of a regular inspection:
• pressure-carrying
walls
/ pressure equipment liner
• the measurement-related function
• the leak tightness
• the
wear
(corrosion)
Note
For detailed information on the maintenance of the device,
consult the associated operating instructions (OI)!