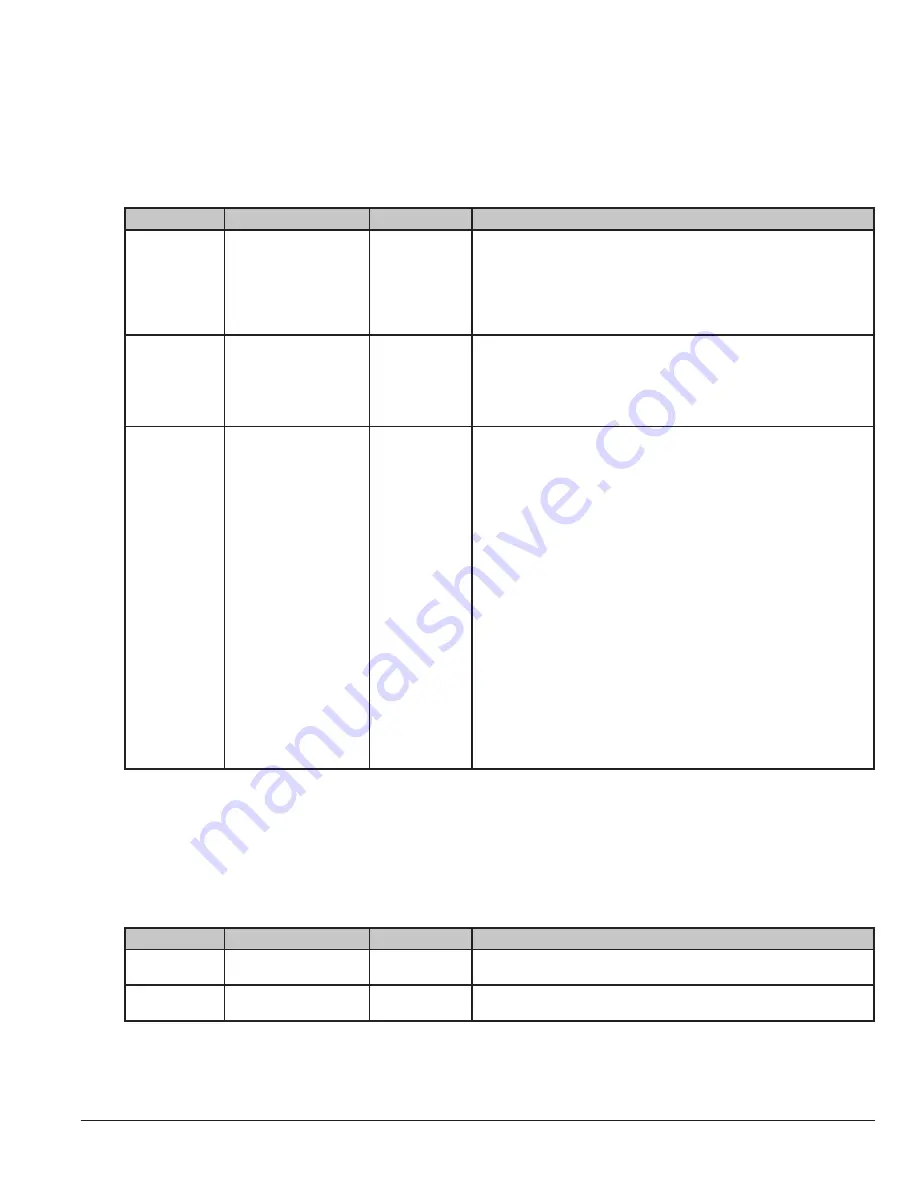
Standalone Motor and ABB Drive Setup 11-7
MN448
11.8 Speed Control Adjustment
Default tuning with the proportional gain (25.02) setting of 10 may result in unstable performance with EC Titanium motors.
Setting the proportional gain to 3 is recommended for smooth operation. Fine tuning the integration time is optional
depending on system dynamics.
Parameter
Name
Value
Description
25.02
Speed Proportional
Gain
3
Defines the proportional gain (Kp) of the speed controller. Too
high a gain may cause speed oscillation.
Here set the proportional gain for the drive control to a value of
3.
Range: 0.00…250.00
25.03
Speed Integration
Time
2.5
Use if fine tuning of the motor performance is required, the
default setting of 2.50s is recommended for most applications.
Reference ACH580 firmware manual for advanced setup of the
speed integration time if required.
Range:0.00…1000.00 s
25.33
Speed controller
autotune
1
ON
Activates (or selects a source that activates) the speed controller
autotune function.
The autotune will automatically set parameters 25.02 Speed
proportional gain, 25.03 Speed integration time and 25.37
Mechanical time constant.
The prerequisites for performing the autotune routine are:
•
the motor identification run (ID run) has been successfully
completed
•
the speed and torque limits (parameter group 30 Limits)
have been set
•
speed feedback filtering (parameter group 90 Feedback
selection), speed error filtering (24 Speed reference
conditioning) and zero speed (21 Start/stop mode) have
been set, and the drive has been started and is running in
speed control mode.
WARNING: The motor and machinery will run against the
torque and speed limits during the autotune routine. MAKE
SURE IT IS SAFE TO ACTIVATE THE AUTOTUNE FUNCTION!
The autotune routine can be aborted by stopping the drive.
For better performance, auto-tuning the speed controller if possible is recommended. Turn the speed controller auto-tune
to on. The load should be connected at this point and free and safe to rotate. During the normal ID run, the motor will rotate
and perform a Parameter 25.33 auto-tune function.
11.9 Auto-phasing configuration
Enter the service password in parameter 96.2 (170708). Auto-phasing current should be between 0.2 and 0.3 p.u. Auto-
phasing time introduces a start delay and with small motors 2 to 3 seconds will be enough to ensure a successful initial rotor
positioning. On larger frame motors 4 to 5 seconds may be required.
Parameter
Name
Value
Description
25.20
Auto-phasing current
0.25
Per unit auto-phasing current for rotor alignment prior to starting
the motor.
25.21
Auto-phasing time
3
Time in seconds auto-phase current is applied to motor for rotor
alignment prior to starting.
Содержание EC Titanium Series
Страница 1: ... MN448_May 2020 May 2020 EC Titanium Manual User s guide ...
Страница 10: ...1 4 Introduction MN448 ...
Страница 20: ...3 4 Mechanical Information and Mounting MN448 ...
Страница 26: ...4 6 Electrical Installation and Planning MN448 ...
Страница 32: ...5 6 Control Pad Wiring and Keypad Interface MN448 ...
Страница 36: ...6 4 Keypad Programming and Basic Operation MN448 ...
Страница 44: ...8 4 Parameter Navigation and Groups MN448 ...
Страница 51: ...9 7 Control Modes MN448 ...
Страница 77: ...11 8 Standalone Motor and ABB Drive Setup MN448 ...
Страница 99: ...A 12 Modbus RTU Example Connection MN448 ...
Страница 102: ......