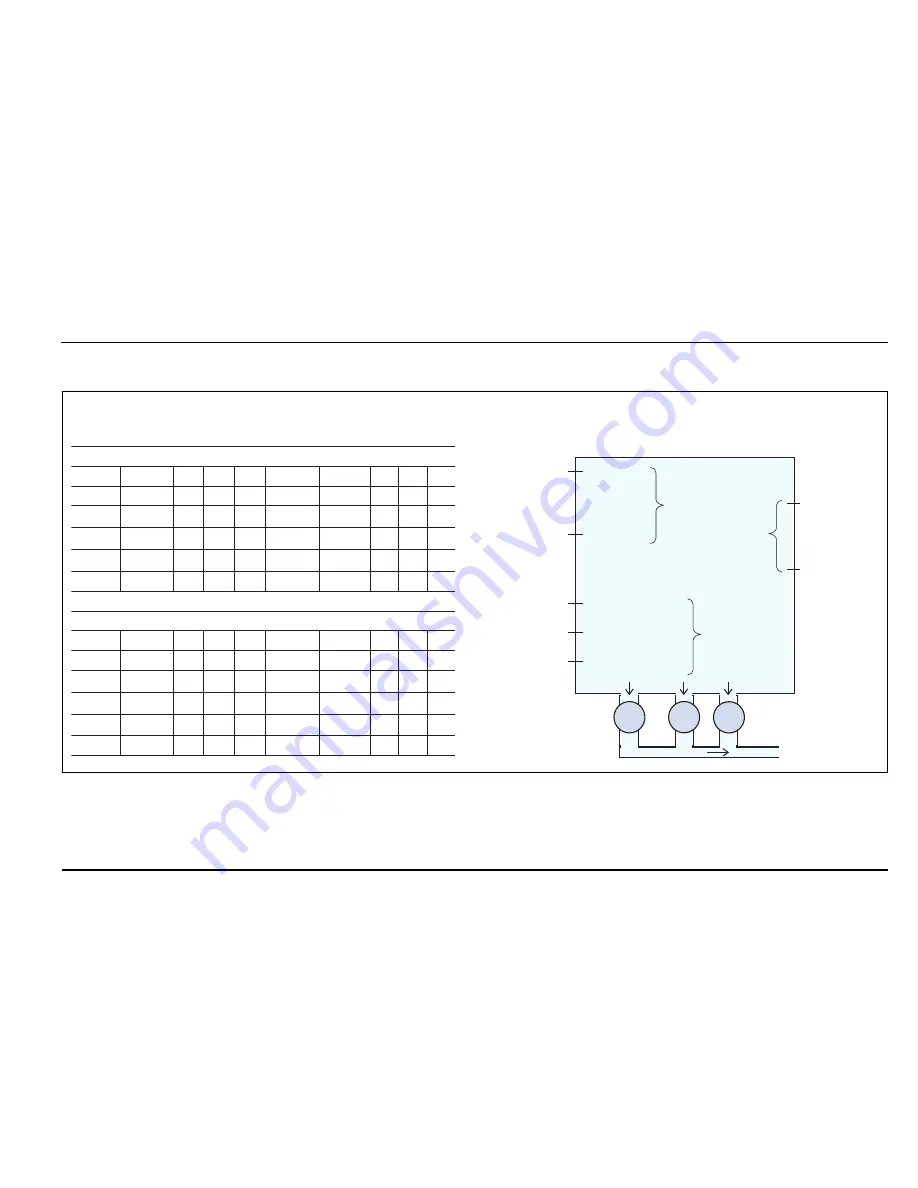
ControlMaster CM10, CM30 and CM50
Universal process controllers,
1
/
8
,
1
/
4
and
1
/
2
DIN
7 Advanced Level
IM/CM/S–EN Rev. R
91
…Functions / …Bank Control
…Bank Control
Using
First In First Out
(
FIFO
) and
Rotate
modes on a 3 pump system
P1
P2
P3
4 m
3 m
2 m
1 m
First In First Out (FIFO)
Level
P1
P2
P3
Level
P1
P2 P3
Seq. 1
1.3 m
Seq. 6
2.2 m
Seq. 2
2.2 m
Seq. 7
0.8 m
Seq. 3
3.6 m
Seq. 8
1.8 m
Seq. 4
4.3 m
Seq. 9
0.8 m
Seq. 5
2.8 m
Seq. 10
1.8 m
Rotate Pump Cycling
Level
P1
P2
P3
Level
P1
P2 P3
Seq. 1
1.3 m
Seq. 6
2.2 m
Seq. 2
2.2 m
Seq. 7
0.8 m
Seq. 3
3.6 m
Seq. 8
1.8 m
Seq. 4
4.3 m
Seq. 9
0.8 m
Seq. 5
2.8 m
Seq. 10
1.8 m
On trip
at 4 m
Off trip
at 3 m
On trip at 1.5 m
Off trip at 1 m
Pump 2
Pump 3
Pump 1
On trip
at 3.5 m
Off trip
at 2.5 m