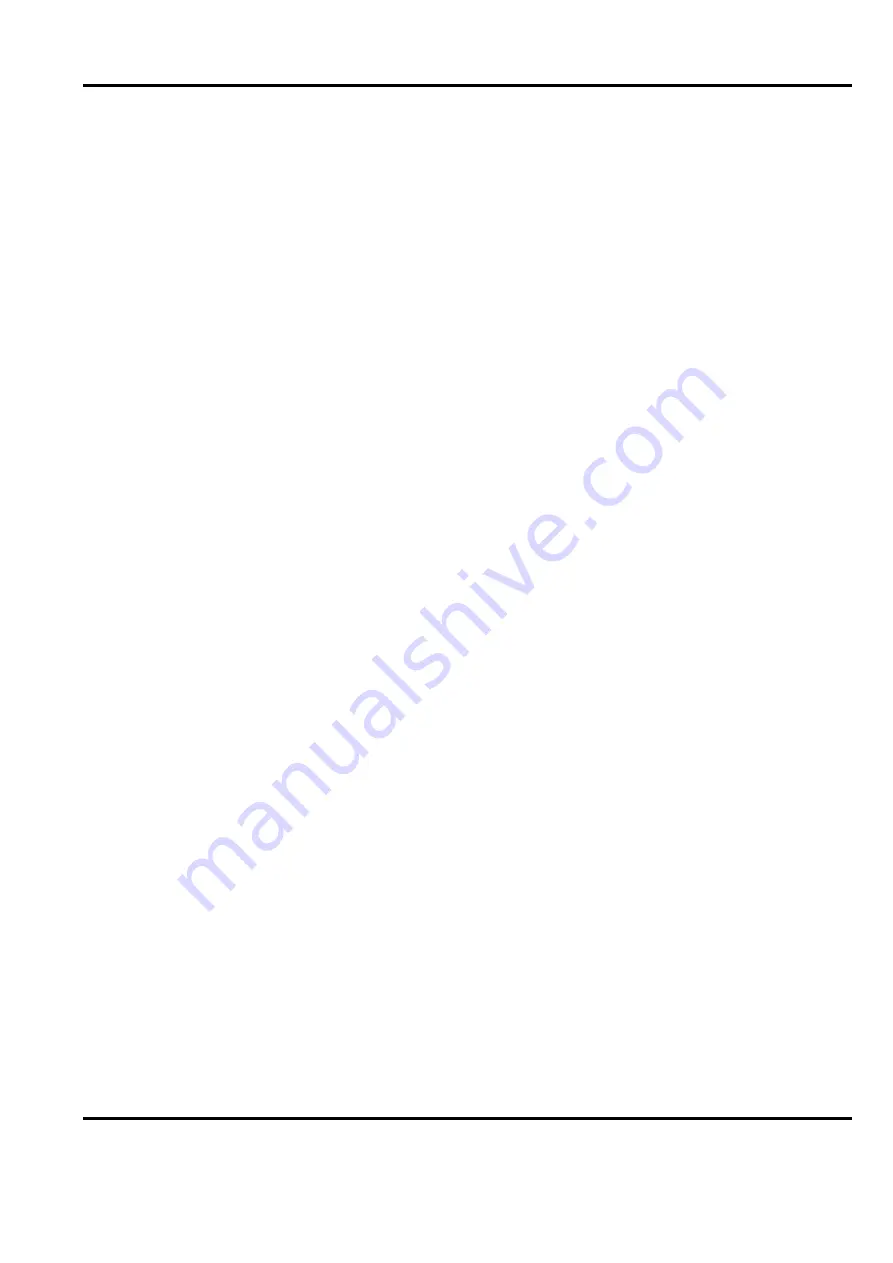
Manual for Induction Motors and Generators
Installation and Alignment -
31
3BFP 000 050 R0101 REV E
3.6.4.3 Thermal axial growth
The thermal axial expansion needs to be taken into consideration if the axial movement of the
non-drive end bearing is locked. See the dimension drawing in order to determine which end is
locked.
The expected axial thermal expansion of the rotor is proportional to the length of the stator
frame, and can be approximately calculated according to the formula:
∆
L =
α
×
∆
T × Lwhere
∆
L=thermal expansion[mm]
α
=10 × 10
-6
K
-1
∆
T=50 K (for AMA, AMB, AMK, AMI), 80 K (for AMH, HXR, M3BM, M3GM)
L=frame length [mm]
NOTE: Make sure that a continuous free axial movement is possible between the coupling
halves (excluding rigid couplings) in order to permit axial thermal expansion of the
machine shaft as not to damage the bearings.
3.6.5 Final alignment
3.6.5.1 General
In the following, the final alignment is made with dial gauges, although there is other and more
exact measuring equipment on the market. The reason for using dial gauges in this text is to
provide some alignment theory.
NOTE: Measurements should be made only after proper shimming and with fixing bolts
properly tightened.
NOTE: The final alignment measurements should always be recorded for future reference.
3.6.5.2 Run-out of the coupling halves
The alignment procedure is started by measuring the run-out of the coupling halves. This
measurement will show any inaccuracy of the shaft and/ or coupling halves.
The run-out of the coupling half in respect to the bearing housing of the machine is measured.
Place the gauges according to
Figure 3-7 Measuring the run-out at the coupling half.
Similarly
check the run-out of the coupling half of the driven machine in respect to its bearing housing.
A simple lever arm is needed to turn a rotor of a sleeve-bearing machine.
***Following note for bearing type: Sleeve bearings
NOTE: Sleeve bearings must be filled with oil before turning.
The admissible run-out error is less than 0.02 mm (0.8 mil).