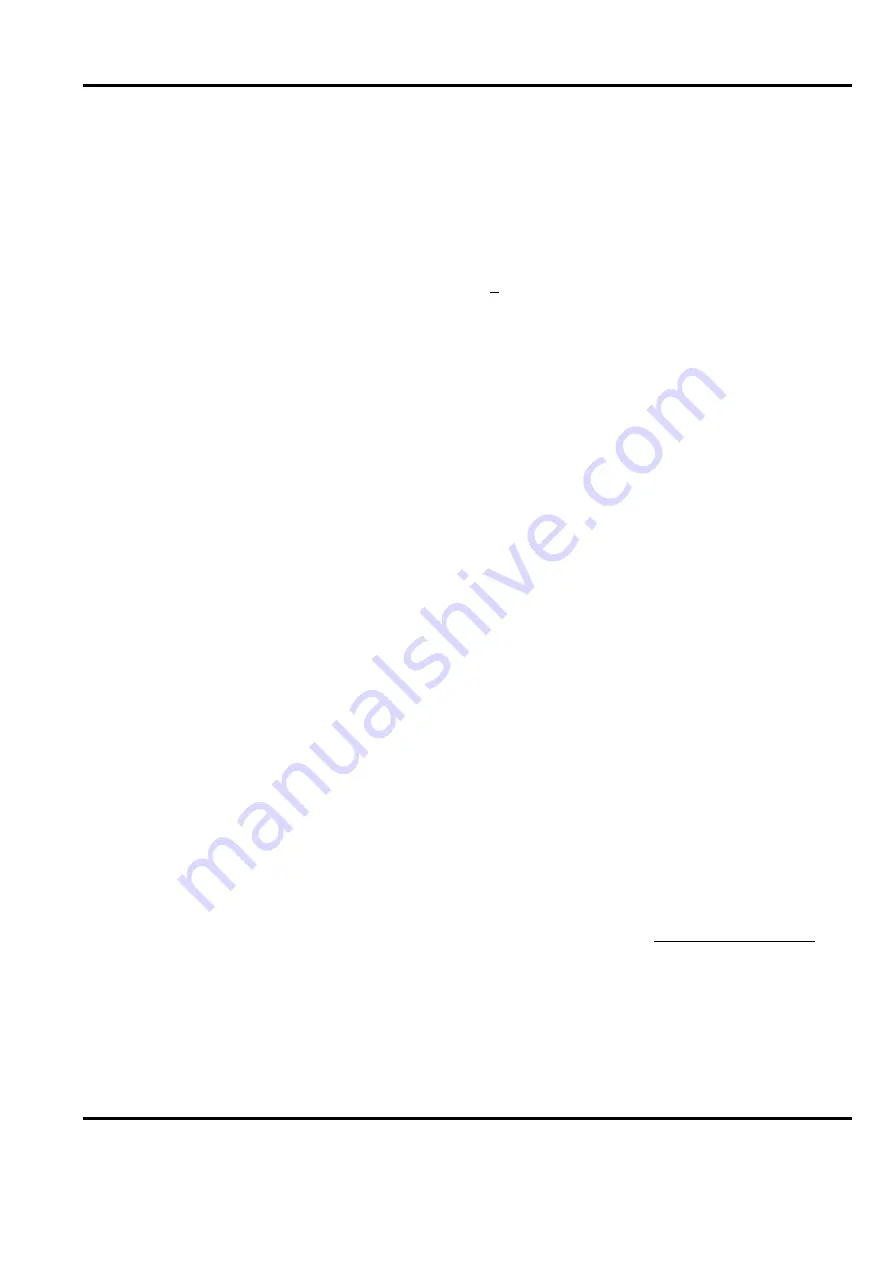
Manual for Induction Motors and Generators
Mechanical and Electrical Connections -
37
3BFP 000 050 R0101 REV E
The cooling water circulates in ducts integrated in the machine frame. The material of the frame
and ducts is carbon steel according to the standard EN 10025: S235 JRG2, equivalent with DIN
17100 - RSt 37-2. This material is prone to corrosion in saline and foul water. The corrosion
products and fouling deposits might block the water flow in the ducts. This is why it is
important to use pure and inhibited water in the cooling system.
Standard values for the cooling water to be used in the cooling system:
•
pH
7.0 - 9.0
•
Alkalinity (CaCO3)
> 1 mmol/kg
•
Chloride (Cl)
< 20 mg/kg
•
Sulphate
< 100 mg/kg
•
KMnO4-concentration
< 20 mg/kg
•
Al-concentration
< 0.3 mg/kg
•
Mn-concentration
< 0.05 mg/kg
In most of the cases, normal tap water, i.e. water for domestic consumption, fulfils all these
requirements.
The cooling water must also be inhibited with an agent protecting the cooling system against
corrosion, fouling and when necessary, against freezing. All materials in touch with the cooling
water (pipes, heat exchanger, etc.) must be taken into account when selecting a suitable
inhibitor.
Recommended inhibitor:
Manufacturer
ASHLAND
Product
RD-25
which is suitable for steel, copper, aluminium and many other materials.
Use only suitable and high-class connection parts and seals to connect the machine to the water
circuit. Check for possible leaks after the piping and joints have been connected.
***Following chapter for bearing type: Sleeve bearing
4.2.3 Sleeve bearing oil supply
Machines with flood lubrication system are equipped with oil pipe flanges, and possibly with
pressure gauges and flow indicators. Install all necessary oil pipes and connect the oil
circulating units.
Install the oil supply system near the machine in equal distance from each bearing. Before
connecting the pipes to the bearings, test the oil supply system by flowing rinsing oil through it.
After this, remove the oil filter and clean it.
Install and connect the oil inlet pipes to the bearings. Install the oil outlet pipes downwards from
the bearings at a minimum angle of 15°, which corresponds to a slope of 250 - 300 mm/m (3 -
3½ inch/ft). The oil level inside the bearing will increase if the slope of the pipes is too small;
the oil will flow too slowly from the bearing to the oil container, and this can result in oil leaks
or disturbances in the oil flow.
NOTE: Do not drill holes through the frame during the installation of the pipes or any other
equipment, as this can damage the machine seriously.