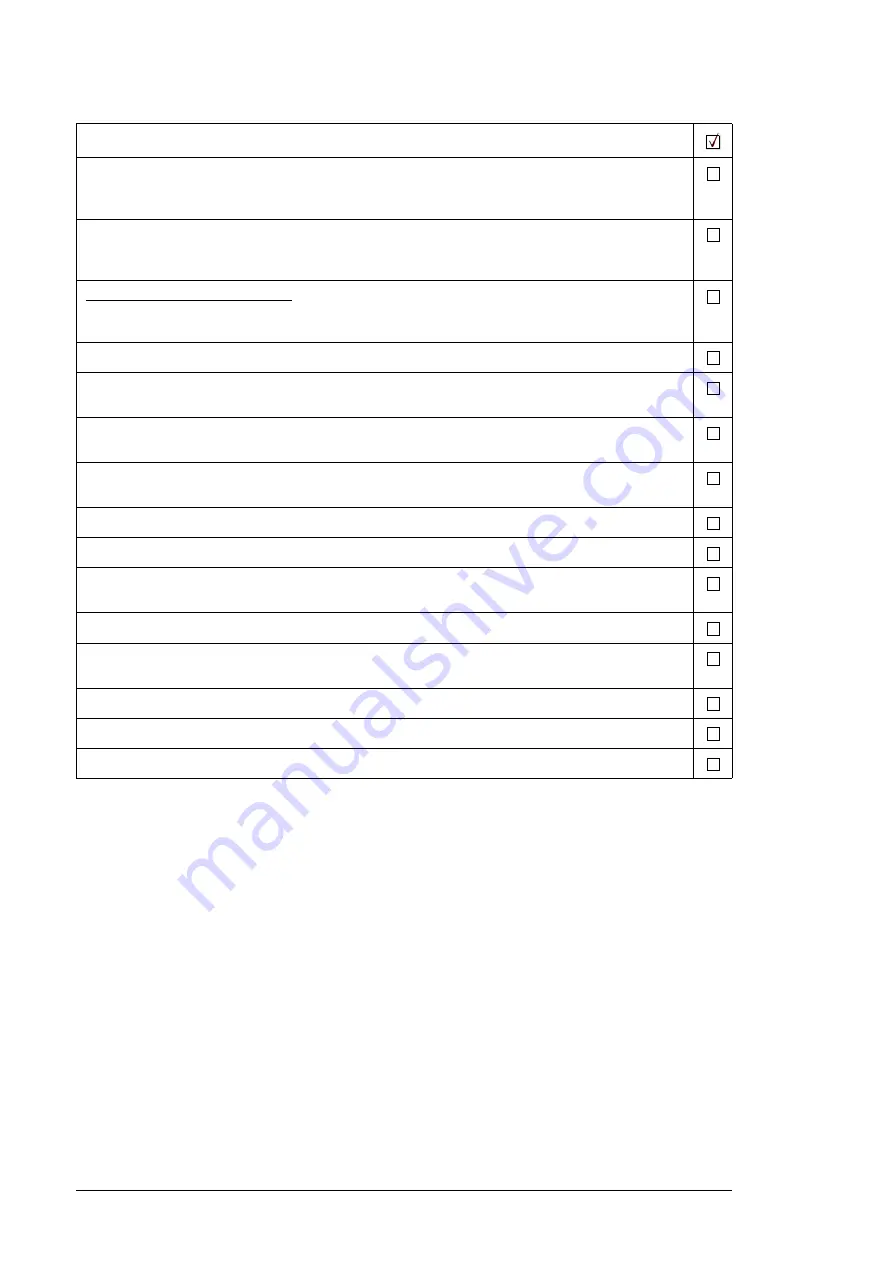
106 Installation checklist
There is an adequately sized protective earth (ground) conductor between the drive and the
switchboard, and the conductor has been connected to appropriate terminal. Proper grounding has
also been measured according to the regulations.
There is an adequately sized protective earth (ground) conductor between the motor and the drive,
and the conductor has been connected to appropriate terminal. Proper grounding has also been
measured according to the regulations.
Only for drives with D150: There is an adequately sized protective earth (ground) conductor
between the user-installed brake resistor and the drive, and the conductor has been connected to
appropriate terminal. Proper grounding has also been measured according to the regulations.
The supply voltage matches the nominal input voltage of the drive. Check the type designation label.
The voltage setting of the auxiliary voltage transformers T21 (standard), T101 (option-specific) and
T111 (option-specific) is correct.
The input power cable has been connected to the appropriate terminals, the phase order is right, and
the terminals have been tightened. (Pull the conductors to check.)
The motor cable has been connected to the appropriate terminals, the phase order is right, and the
terminals have been tightened. (Pull the conductors to check.)
The motor cable (and brake resistor cable, if present) has been routed away from other cables.
No power factor compensation capacitors have been connected to the motor cable.
The external brake resistor (if present) has been connected to the appropriate terminals, and the
terminals have been tightened. (Pull the conductors to check.)
The brake resistor cable has been routed away from other cables.
The control cables have been connected to the appropriate terminals, and the terminals have been
tightened. (Pull the conductors to check.)
There are no tools, foreign objects or dust from drilling inside the drive.
All shrouds and cover of the motor connection box are in place. Cabinet doors have been closed.
The motor and the driven equipment are ready for start.
Check that …
Содержание ACS880-07XT Series
Страница 1: ...ABB industrial drives Hardware manual ACS880 07XT drives 400 to 1200 kW ...
Страница 4: ......
Страница 12: ...12 ...
Страница 20: ...20 Safety instructions ...
Страница 26: ...26 Introduction to the manual ...
Страница 47: ...Mechanical installation 47 Moving the crate with a forklift Free width for fork tines 750 mm 29 5 ...
Страница 54: ...54 Mechanical installation ...
Страница 89: ...Electrical installation 89 PE 11 8 4 9 11 ...
Страница 94: ...94 Electrical installation ...
Страница 110: ...110 Start up Test and validate the operation of Prevention of unexpected start with FSO xx option Q950 Action ...
Страница 112: ...112 Fault tracing ...
Страница 123: ...Maintenance 123 5 6 7 ...
Страница 124: ...124 Maintenance 8 10 9 ...
Страница 126: ...126 Maintenance 6 5 4 ...
Страница 127: ...Maintenance 127 9 8 7 ...
Страница 128: ...128 Maintenance 12 11 10 ...
Страница 149: ...Dimensions 149 Dimension drawing examples Frame 2 R11 R10 with brake chopper ...
Страница 150: ...150 Dimensions Frame 2 R11 R10 without brake chopper ...
Страница 153: ...Dimensions 153 Location of input terminals ACS880 07XT 12 pulse ...
Страница 154: ...154 Dimensions Location of output terminals ACS880 07XT R10 with du dt ...
Страница 155: ...Dimensions 155 Location of output terminals ACS880 07XT R10 without du dt ...
Страница 156: ...156 Dimensions Location of output terminals ACS880 07XT R11 with du dt ...
Страница 157: ...Dimensions 157 Location of output terminals ACS880 07XT R11 without du dt ...
Страница 158: ...158 Dimensions Location of PE terminals ACS880 07XT ...
Страница 159: ...Dimensions 159 Location of resistor terminals ACS880 07XT R10 ...
Страница 160: ...160 Dimensions Location of resistor terminals ACS880 07XT R11 ...
Страница 168: ...www abb com drives www abb com drivespartners 3ABD00043579 Rev C EN 2018 01 01 Contact us ...