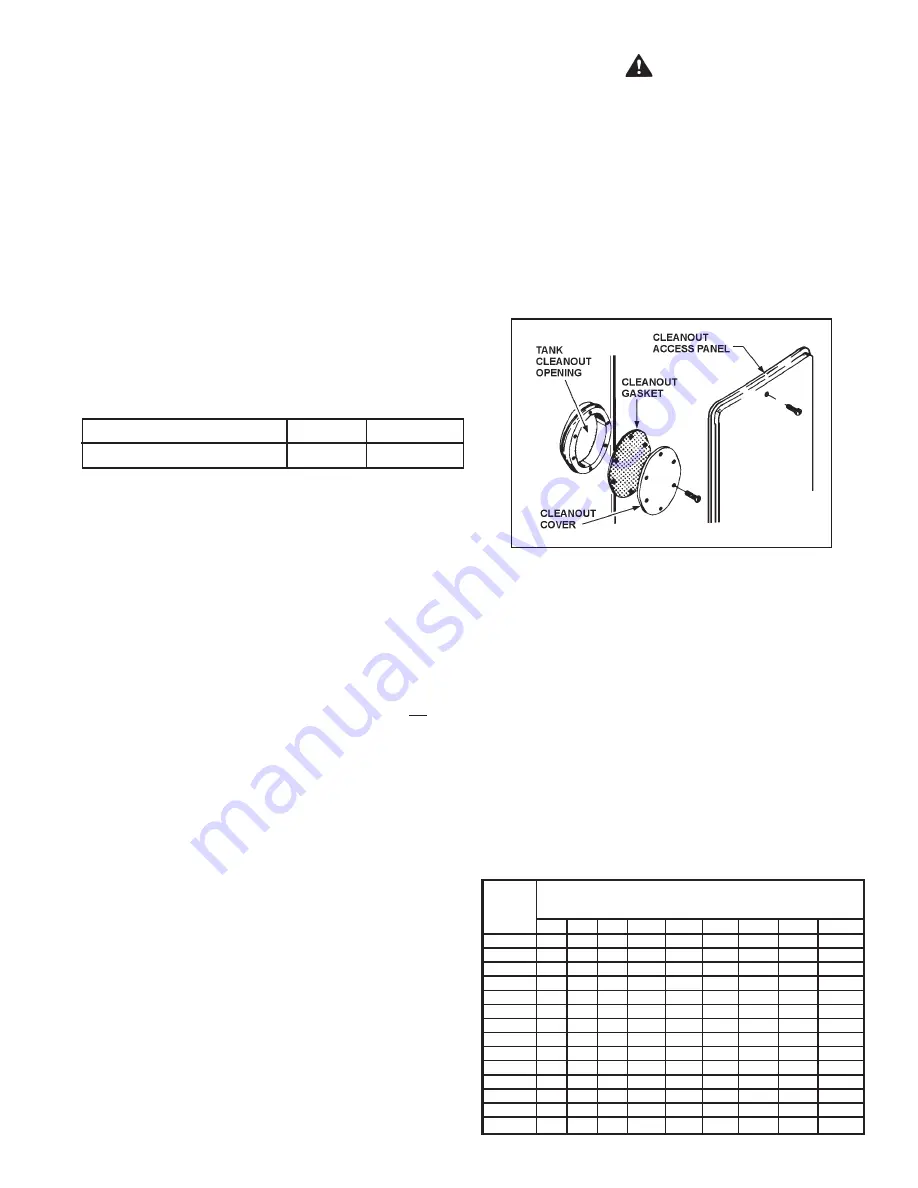
11
5.
Attach a properly sized length of Selkirk Metalbestos model
PS or model G venting to the exhaust vent adapter using the
inner vee bands, see Figures 7 and 7B on page 10.
6.
Fill the grooves in both inner vee bands with high-temp
silicone sealant, Dow Corning 736 or equivalent.
7.
Position the inner vee bands around the inner pipe flanges
and tighten the screws securing the bands.
8.
Align the outer channel band with the outer pipe grooves
and tighten the screws securing the bands.
9.
Repeat steps 6-8 for each successive pipe length until the
venting reaches the heater.
10. Follow the manufacturer’s instructions for proper support
and guide spacing for horizontal runs of pipe, see Table 6.
TABLE 6.
Vent Diameter
S
F
8” - BTPV -540A, 650A & 740A
15’ 3”
7’ 6”
S = Maximum spacing between two guides or a support
and a guide in either a vertical or horizontal direction.
F = Maximum height above a guide or support for free
standing system above a roof or parapet wall.
11. Use an expansion joint between any two fixed points in the
exhaust venting system wherever the expansion may exceed
1/4”. Selkirk Metalbestos model PS and model G venting
will expand by one inch per 100°F in gas temperature per
100 feet of vent length. The expansion can be calculated by
the following formula:
Expansion,
Vent length between
5
Inches
two fixed points, feet 100
If the expansion calculated is greater than 1/4”, an expansion
joint must be used between the two fixed points.
12. Attach the flue reducer included in the exhaust vent hood
package to the flue collar on the heater.
13. Attach the flue reducer to the vent system using a seal ring.
Attach this ring to the venting using the inner vee bands as
outlined in Steps 5-7.
14. Attach 8” air-intake connector to intake vent hood collar. It
may be necessary to use a slip-slip coupling to fit the pipe
to the intake vent hood.
15. Attach 8” air-intake connector back to the 6” burner air inlet
with 8” x 6” reducer. Prime and cement each joint to assure
gas-tight construction.
16. Seal all joints at the vent hoods with silicone sealant. Also
seal the joints at the flue collar and air inlet adapter. Joint on
the exhaust side must be sealed with high-temp silicone
sealant, Dow Corning 736 or equivalent.
WARNING
PRIMERS AND CEMENTS ARE EXTREMELY FLAMMABLE, AND
MUST NOT BE STORED OR USED NEAR HEAT OR OPEN FLAME.
ALLOW ADEQUATE CURING TIME BEFORE OPERATING HEATER.
DRAIN VALVE AND ACCESS PANELS
The heaters are equipped with a 3/4” NPT drain valves mounted
above and to the left of the burner.
An access panel is located above and to the right of the burner,
see Figure 8. This panel covers the cleanout opening in the tank
which is sealed by a gasket and cover. Another cleanout access
panel is located towards the back of the heater.
FIGURE 8.
GAS PIPING
Contact your local gas service company to ensure that adequate
gas service is available and to review applicable installation
codes for your area.
Size the main gas line in accordance with Table 9 and 9A.
Minimum required gas supply pipe size is 1 1/4”. The figures
shown are for straight lengths of pipe at 0.5 in. w.c. pressure
drop, which is considered normal for low pressure systems.
Note that fittings such as elbows and tees will add to the pipe
pressure drop.
TABLE 9
MAXIMUM CAPACITY OF PIPE IN CUBIC FEET OF GAS PER HOUR
(Based upon a Pressure Drop of 0.5 inch Water Column
and 0.5 Specific Gravity Gas and max. gas press. of .5 psig)
LENGTH
IN
Nominal Iron Pipe Sizes, Inches
FEET
1/2"
3/4"
1"
1 1/4" 1 1/2"
2"
2 1/2"
3"
4"
10
175
360
680
1400
2100
3960
6300
11000
23000
20
120
250
485
950
1460
2750
4360
7700
15800
30
97
200
375
770
1180
2200
3520
6250
12800
40
82
170
320
660
990
1900
3000
5300
10900
50
73
151
285
580
900
1680
2650
4750
9700
60
66
138
260
530
810
1520
2400
4300
8800
70
61
125
240
490
750
1400
2250
3900
8100
80
57
118
220
460
690
1300
2050
3700
7500
90
53
110
205
430
650
1220
1950
3450
7200
100
50
103
195
400
620
1150
1850
3250
6700
125
44
93
175
360
550
1020
1650
2950
6000
150
40
84
160
325
500
950
1500
2650
5500
175
37
77
145
300
460
850
1370
2450
5000
200
35
72
135
280
430
800
1280
2280
4600
=
x
Содержание Conservationist BTPV 650A
Страница 20: ...20 FIGURE 11...
Страница 21: ...21 FIGURE 12...
Страница 25: ...25 PREMIX LOW NOx BURNER EXPLODED VIEW FOR BTP MODELS FIGURE 13...
Страница 26: ...26 PREMIX LOW NOx BURNER EXPLODED VIEW FOR BTPV MODELS FIGURE 14...
Страница 34: ...34 NOTES...
Страница 35: ...35 NOTES...