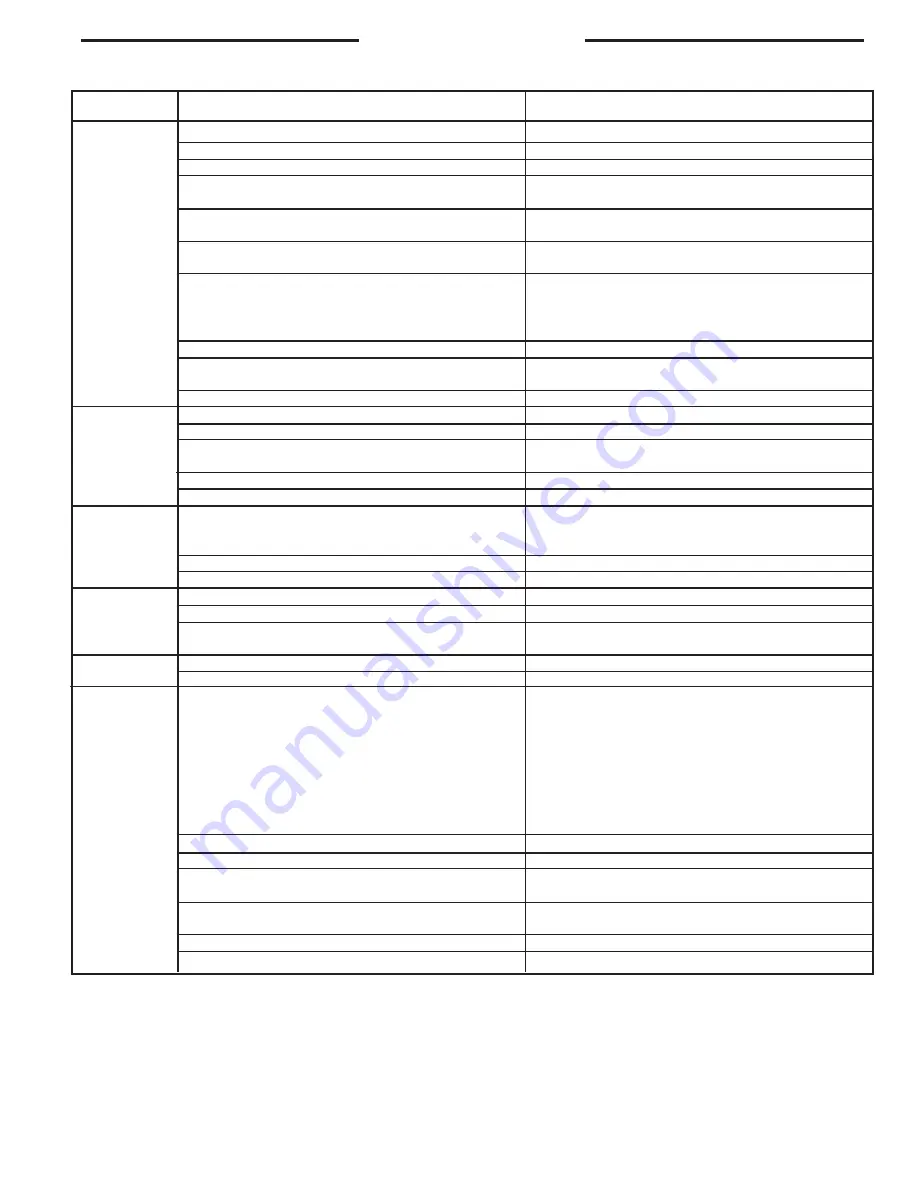
23
TROUBLESHOOTING
TROUBLE
CAUSE
REMEDY
Oil level below intake line in supply tank.
Fill tank with oil.
Clogged strainer or filter.
Remove and clean strainer. Replace filter element.
Clogged nozzle.
Replace nozzle.
Air leak in intake line.
Tighten all fittings in intake line. Tighten unused intake
port plug. Check filter cover and gasket.
Restricted intake line. (High vacuum reading).
Replace any kinked tubing and check any valves in
intake line.
No Oil Flow
A two line pipe system that becomes air bound.
Check for and insert by-pass plug. Make sure return
at Nozzle
line is below oil level in tank.
A single line pipe system that becomes air bound.
Loosen gauge port plug or air bleed valve and bleed oil
for 15 seconds after foam is gone in bleed hose, Check
intake line fittings for tightness. Check all fuel pump plugs
for tightness.
Slopping or broken coupling.
Replace coupling.
Rotation of motor and fuel unit pump is not the
same as indicated by arrow on the pad at top of unit.
Install fuel pump with correct rotation.
Frozen fuel pump shaft.
Replace fuel pump. Check for water and dirt in tank.
Loosen plugs and fittings.
Tighten with good quality thread sealer.
Leak at pressure adjusting screw or nozzle plug.
Replace fuel pump.
Oil Leak
Blown seal (single-pipe system)
Check to see if by-pass plug has been left in fuel pump.
Replace fuel pump.
Seal leaking.
Replace fuel pump.
Cover.
Tighten cover screws.
Bad coupling alignment.
Loosen fuel pump mounting screws slightly and shift
Noisy
fuel pump in different positions until noise is eliminated.
Operation
Retighten mounting screws.
Air in inlet line.
Check all connections. Use only good flare fittings.
Tank turn on two line pipe system and inside tank.
Install return line hum eliminator.
Partially clogged strainer or filter.
Remove and clean strainer.
Air leak in intake line.
Tighten all fittings.
Air leaking around cover.
Be sure strainer cover screws are tightened securely.
Check for damaged cover gasket.
Low Oil
Defective gauge
Check gauge against master gauge or other gauge.
Pressure
Nozzle capacity is greater than fuel pump capacity.
Replace fuel unit with unit of correct capacity.
To determine the cause of improper cut-off, insert
a pressure gauge in the nozzle port of the fuel pump.
After a minute of operation, shut burner down. If the
pressure drops from normal operating pressure and
stabilizes, the fuel pump is operating properly and air
is the cause of improper cut-off. If, however, the
pressure drops to 0 psi, fuel unit should be replaced.
Improper
NOTE: Never use the amount of pressure drop as an
Nozzle
indication of the quality or speed of cut-off.
Cut-Off
Filter leaks.
Check face of cover and gasket for damage.
Strainer cover loose.
Tighten 4 screws on cover.
Air pocket between cut-off valve and nozzle.
Run burner, stopping and starting unit, until smoke
and after-fire disappears.
Air leak in intake line.
Tighten intake fittings. Tighten unused intake port and
return plug.
Partially clogged nozzle strainer.
Clean strainer or change nozzle.
Leak at nozzle adaptor.
Change nozzle and adaptor.
TABLE 10 - OIL BURNER TROUBLESHOOTING