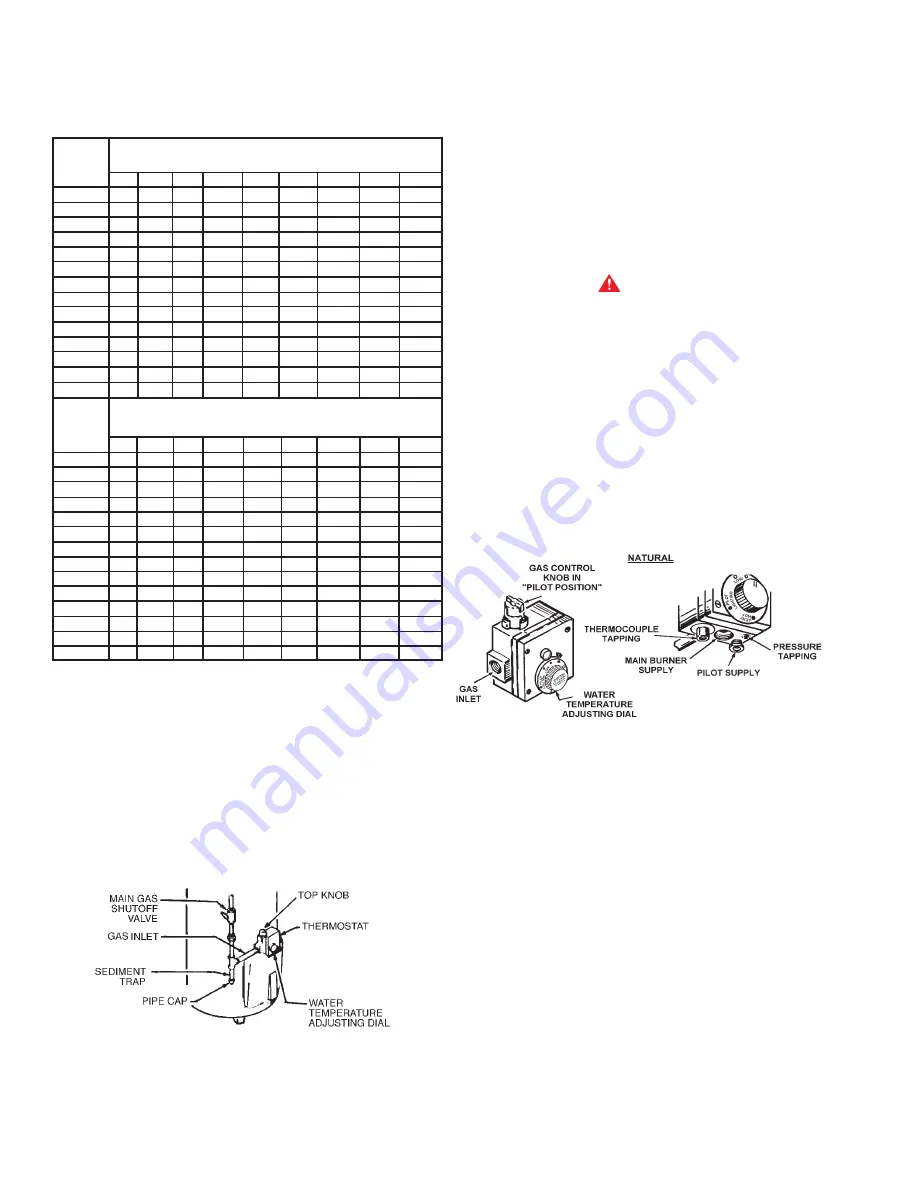
8
TABLE 1 - GAS SUPPLY LINE SIZES (IN INCHES)*
MAXIMUM CAPACITY OF PIPE IN
CUBIC FEET PER HOUR
LENGTH
NORMAL IRON PIPE SIZES (INCHES)
IN
INPUT IN THOUSANDS BTU/HR
FEET
1/2"
3/4"
1"
1 1/4" 1 1/2"
2"
2 1/2"
3"
4"
10
175
360
680
1400
2100 3960
6300
11000 23000
20
120
250
485
950
1460 2750
4360
7700 15800
30
97
200
375
770
1180 2200
3520
6250 12800
40
82
170
320
660
990
1900
3000
5300 10900
50
73
151
285
580
900
1680
2650
4750
9700
60
66
138
260
530
810
1520
2400
4300
8800
70
61
125
240
490
750
1400
2250
3900
8100
80
57
118
220
460
690
1300
2050
3700
7500
90
53
110
205
430
650
1220
1950
3450
7200
100
50
103
195
400
620
1150
1850
3250
6700
125
44
93
175
360
550
1020
1650
2950
6000
150
40
84
160
325
500
950
1500
2650
5500
175
37
77
145
300
460
850
1370
2450
5000
200
35
72
135
280
430
800
1280
2280
4600
LENGTH
NORMAL IRON PIPE SIZES (INCHES)
IN
INPUT IN KW
METERS 1/2"
3/4"
1"
1 1/4" 1 1/2"
2"
2 1/2"
3"
4"
3
51
105
199
410
615
1160
1845
3221
6735
6
35
73
142
278
428
805
1277
2255
4626
9
28
59
110
225
346
644
1031
1830
3748
12
24
50
94
193
290
556
878
1552
3192
15
21
44
83
170
264
492
776
1391
2840
18
19
40
76
155
237
445
703
1259
2577
21
18
37
70
143
220
410
659
1142
2372
24
17
35
64
135
202
381
600
1083
2196
27
16
32
60
126
190
357
571
1010
2108
31
15
30
57
117
182
337
542
952
1962
38
13
27
51
105
161
299
483
864
1757
46
12
25
47
95
146
278
439
776
1610
53
11
23
42
88
135
249
401
717
1464
61
10
21
40
82
126
234
375
688
1347
To prevent damage, care must be taken not to apply too much
torque when attaching gas supply pipe to gas valve inlet.
Apply joint compounds (pipe dope) sparingly and only to the male
threads of pipe joints. Do not apply compounds to the first two
threads. Use compounds resistant to the action of liquefied
petroleum gases.
BEFORE PLACING THE HEATER IN OPERATION, CHECK FOR
GAS LEAKAGE.
Use soap and water solution or other material
acceptable for the purpose in locating the leaks.
DO NOT USE
MATCHES, CANDLES, FLAME OR OTHER SOURCES OF IGNITION
FOR THIS PURPOSE.
FIGURE 4 - GAS PIPING AND DIRT LEG INSTALLATION
DISCONNECT THE HEATER AND ITS MANUAL GAS Shut-off VALVE
FROM THE GAS SUPPLY PIPING SYSTEM DURING ANY SUPPLY
PRESSURE TESTING EXCEEDING 1/2 PSIG (3.45 Kpa). GAS
SUPPLY LINE MUST BE CAPPED WHEN DISCONNECTED FROM
THE HEATER. FOR TEST PRESSURES OF 1/2 PSIG
(3.45 Kpa) OR LESS THE APPLIANCE NEED NOT BE
DISCONNECTED, BUT MUST BE ISOLATED FROM THE SUPPLY
PRESSURE TEST BY CLOSING THE MANUAL GAS Shut-off VALVE.
PURGING
Gas line purging is required with new piping or systems in which
air has entered.
CAUTION
PURGING SHOULD BE PERFORMED BY PERSONS
EXPERIENCED IN THIS TYPE GAS SERVICE. TO AVOID RISK OF
FIRE OR EXPLOSION, PURGE DISCHARGE MUST NOT ENTER
CONFINED AREAS OR SPACES WHERE IGNITION CAN OCCUR.
THE AREA MUST BE WELL VENTILATED AND ALL SOURCES OF
IGNITION MUST BE INACTIVATED OR REMOVED.
GAS METER SIZE — NATURAL GAS ONLY
Be sure the gas meter has sufficient capacity to supply the full
rated gas input of the water heater as well as the requirements of
all other gas fired equipment supplied by the meter. If gas meter is
too small, ask the gas company to install a larger meter having
adequate capacity.
FIGURE
5 -THERMOSTAT FOR NATURAL GAS
GAS PRESSURE REGULATOR
The gas pressure regulator is built into the gas valve and is
equipped to operate on the gas specified on model and rating
plate. The regulator is factory adjusted to deliver gas to burner at
correct water column pressure allowing for a nominal pressure
drop through the controls.
The minimum gas supply pressure for input adjustment is
5.0" W.C. (1.24 kPa) for natural gas or 11.0" W.C. (2.74 kPa) for
propane gas.
Do not subject the combination gas valve to inlet gas
pressures of more than 10.5" W.C. (2.61 kPa) - natural gas or 13.0"
W.C. (3.23 kPa) - propane gas. A service regulator is necessary if
higher gas pressures are encountered.
Gas pressure specified in Table 2, refer to flow pressure taken at
pressure tap of automatic gas valve while heater is operating.