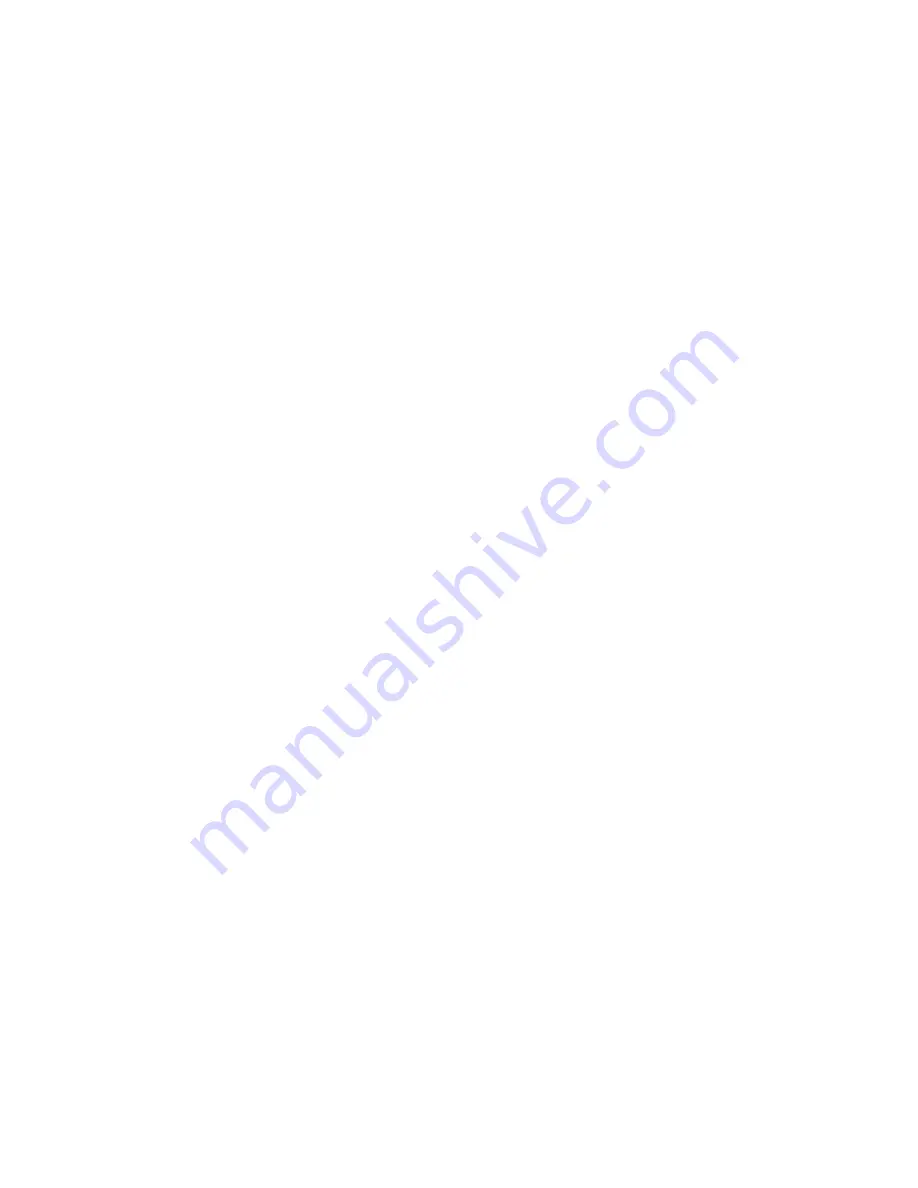
18
Bearings are a primary concern on pumping
units. First, dismantle the bearings; clean and
inspect them for any rusted or badly worn
surfaces. If bearings are free from rust and
wear, reassemble and relubricate them with
one of the recommended pump lubricants.
Depending on the length of time the pump
has remained in the flooded area, it is unlikely
that bearing replacement is necessary;
however, in the event that rust or worn
surfaces appear, it may be necessary to
replace the bearings.
Next, inspect the stuffing box, and clean out
any foreign matter that might clog the box.
Mechanical seals should be cleaned and
thoroughly flushed.
Couplings should be dismantled and
thoroughly cleaned.
Any pump that is properly sealed at all joints
and connected to both the suction and
discharge should exclude outside liquid.
Therefore, it should not be necessary to go
beyond the bearings, stuffing box, and
coupling when servicing the pump.
BEARING LUBRICATION – GREASE
Grease lubricated ball bearings are packed
with grease at the factory and ordinarily will
require no attention before starting, provided
the pump has been stored in a clean, dry
place prior to its first operation. The bearings
should be watched the first hour or so after
the pump has been started to see that they
are operating properly.
The importance of proper lubrication cannot
be over emphasized. It is difficult to say how
often a bearing should be greased, since that
depends on the conditions of operation. It is
well to add one ounce of grease at regular
intervals, but it is equally important to avoid
adding too much grease. For average
operating conditions, it is recommended that
1 oz. of grease be added at intervals of three
to six months, and only clean grease be
used. It is always best if unit can be stopped
while grease is added to avoid overloading.
NOTE:
Excess grease is the most common
cause of over-heating.
A lithium based NLGI-2 grade grease should
be used for lubricating bearings where the
ambient temperature is above -20°F. Grease
lubricated bearings are packed at the factory
with Shell Alvania No 2. Other recommended
greases are Texaco Multifak No. 2 and
Mobilux No. 2 grease.
Greases made from animal or vegetable oils
are not recommended due to the danger of
deterioration and forming of acid. Do not use
graphite. Use of an ISO VG 100 mineral base
oil with rust and oxidation inhabitors is
recommended.
The maximum desirable operating
temperature for ball bearings is 180°F.
Should the temperature of the bearing frame
rise above 180°F, the pump should be shut
down to determine the cause.
PACKING SEAL
When a pump with packing is first started it is
advisable to have the packing slightly loose
without causing an air leak. As the pump runs
in, gradually tighten the gland bolts evenly.
The gland should never be drawn to the point
where packing is compressed too tightly and
no leakage occurs. This will cause the
packing to burn, score the shaft sleeve and
prevent liquid from circulating through the
stuffing box cooling the package.
NOTE:
Eccentric run-out of the shaft or
sleeve through the packing could result in
excessive leakage that cannot be
compensated for. Correction of this defect
requires shaft and/or sleeve replacement.
Packing should be checked frequently and
replaced as service indicates. Six months
might be a reasonable expected life,
depending on the operating conditions.
CLEANING WITHOUT DISMANTLING PUMP
A short section of pipe so designed that it can
be readily dropped out of the line can be
installed adjacent to the suction flange. With
this arrangement, any matter clogging the
impeller is accessible by removing the pipe
section.
If the pump cannot be freed of clogging after
the above methods have been tried,
dismantle the unit as previously described to
locate the trouble.