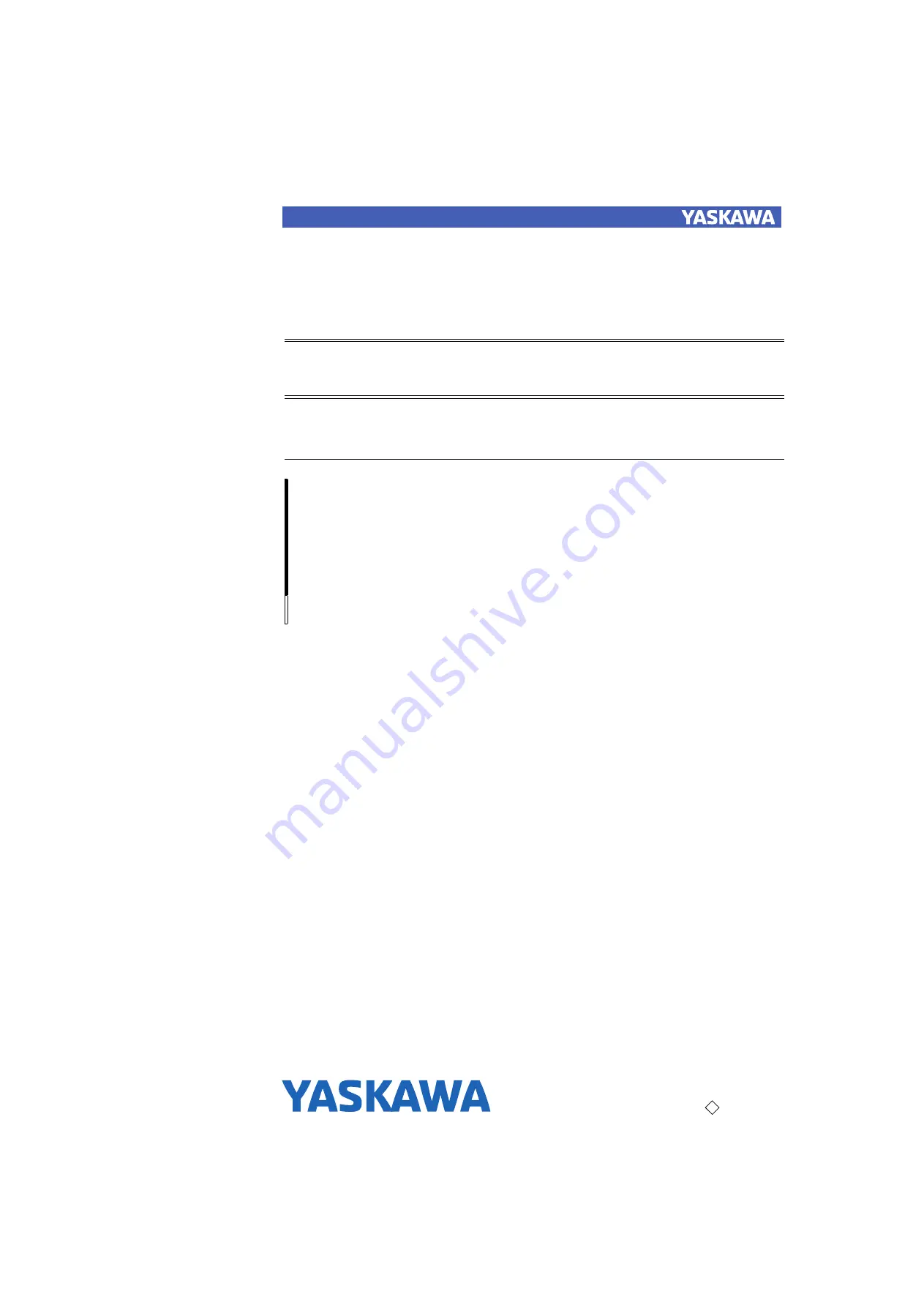
MANUAL NO.
2
HW0485750
Part Number:
171469-1CD
Revision:
1
MOTOMAN-MH5
INSTRUCTIONS
TYPE:
YR-MH00005-C00 (STANDARD SPECIFICATION DX100)
YR-MH0005N-C00 (STANDARD SPECIFICATION NXC100)
Upon receipt of the product and prior to initial operation, read these instructions thoroughly, and retain
for future reference.
MOTOMAN INSTRUCTIONS
MOTOMAN-MH5 INSTRUCTIONS
DX100 INSTRUCTIONS
DX100 OPERATOR’S MANUAL
DX100 MAINTENANCE MANUAL
NXC100 INSTRUCTIONS
NX100 OPERATOR’S MANUAL
NXC100 MAINTENANCE MANUAL
The DX/NX100 Operator’s Manuals above correspond to specific usage.
Be sure to use the appropriate manual.
1 of 74