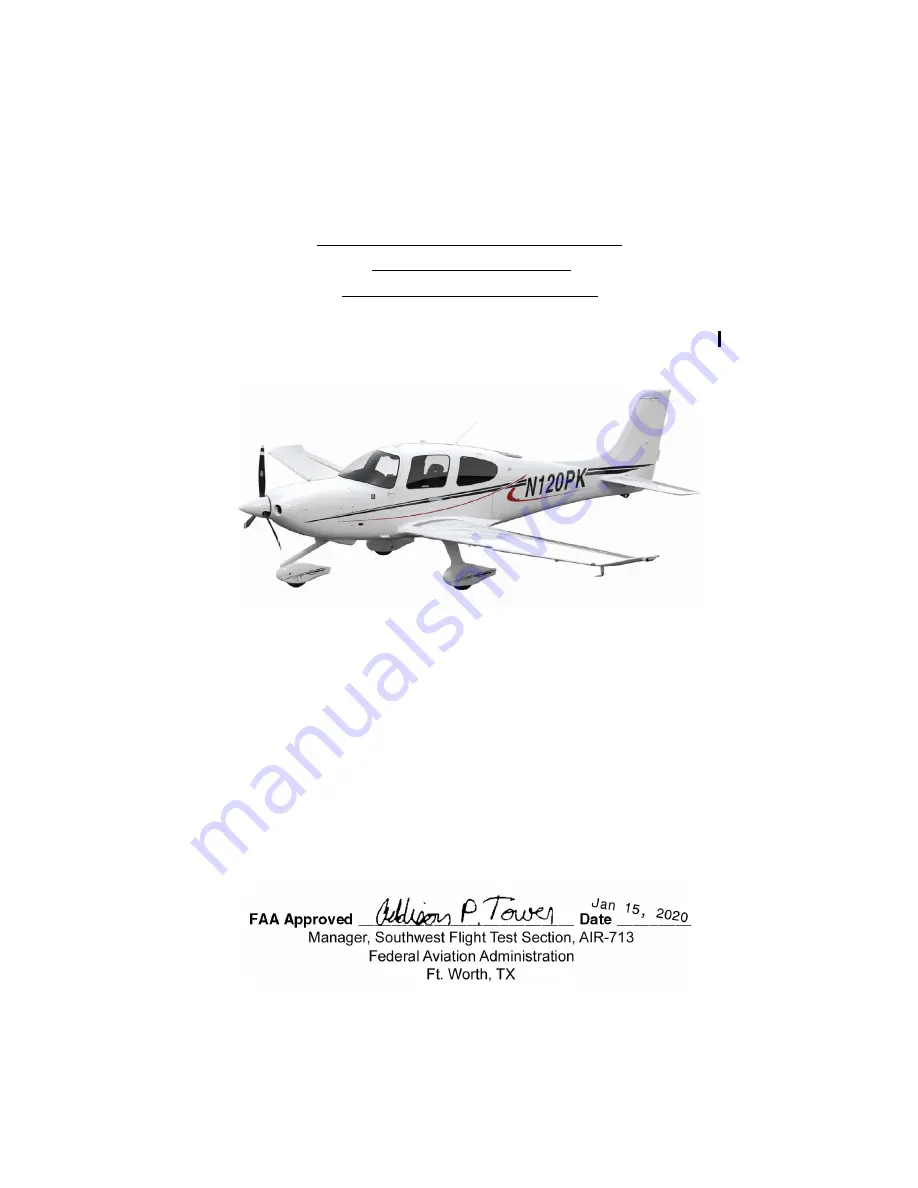
P/N 11934-005
Cover Page-i
PILOT’S OPERATING HANDBOOK
AND FAA APPROVED
AIRPLANE FLIGHT MANUAL
for the CIRRUS DESIGN SR20
Aircraft Serials 2220, 2339 and Subsequent with
Cirrus Pers Avionics System
FAA Approved in Normal Category based on 14 CFR 23. This document
must be carried in the airplane at all times and be kept within the reach of
the pilot during all flight operations.
THIS MANUAL INCLUDES THE MATERIAL REQUIRED TO BE FURNISHED TO
THE PILOT BY 14 CFR 23 AND ADDITIONAL INFORMATION PROVIDED BY
CIRRUS AIRCRAFT AND CONSTITUTES THE FAA APPROVED AIRPLANE
FLIGHT MANUAL.
Model - Serial #:
Registration #:
Reissue A