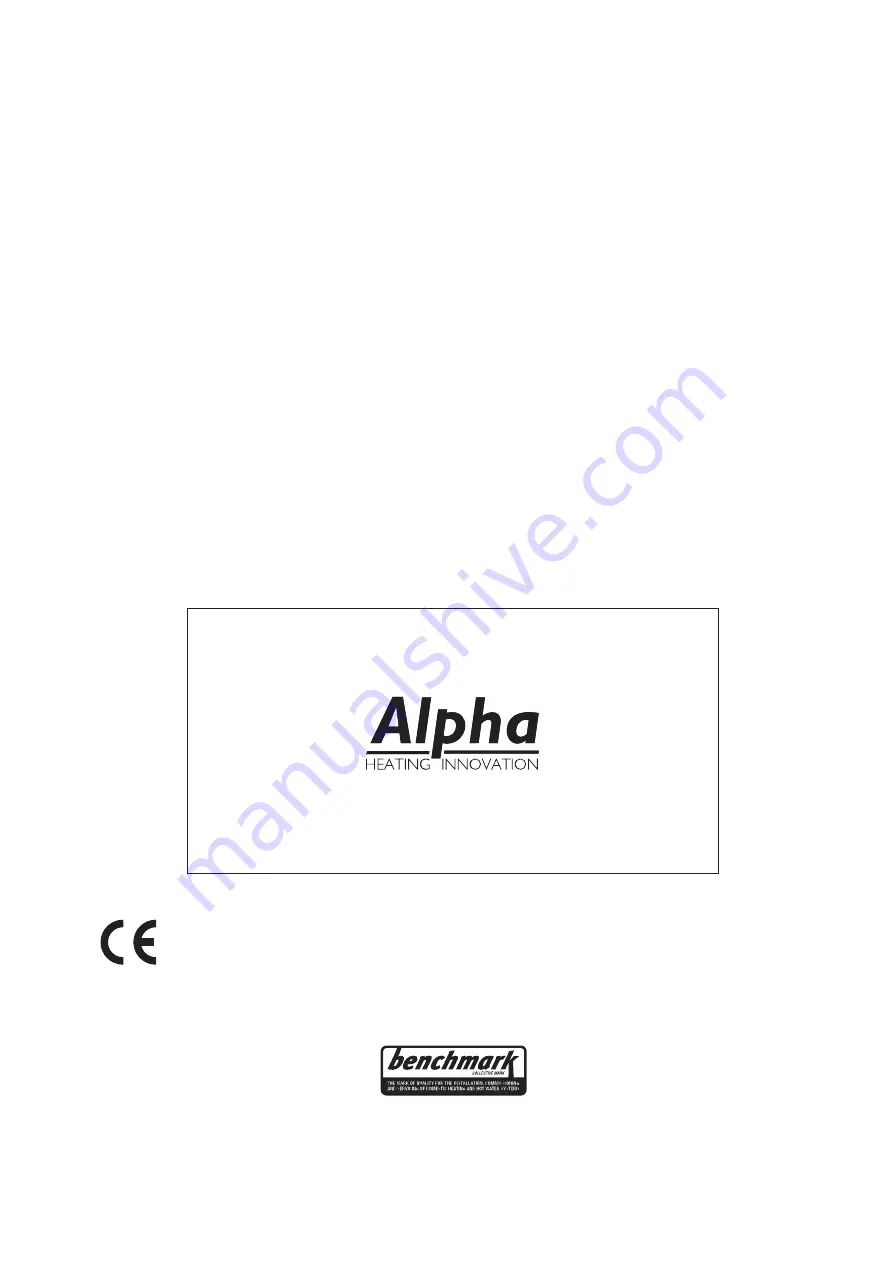
Alpha CD 13R (NG)
G.C. No. 41 532 05
Alpha CD 18R (NG)
G.C. No. 41 532 03
Alpha CD 24R (NG)
G.C. No. 41 532 04
Alpha CD 13R (LPG)
G.C. No. 41 532 11
Alpha CD 18R (LPG)
G.C. No. 41 532 09
Alpha CD 24R (LPG)
G.C. No. 41 532 10
Set for use with Natural Gas
Leave these instructions with the User
These instructions have been carefully prepared but we reserve the right
to alter the specification at any time in the interest of product improvement.
© Alpha Therm Limited 2015.
Part No. 1.038436 ST.001941/000
0615/D352
Installation and Servicing
Instructions
Alpha CD 13R,18R and 24R
Wall Mounted, Fan Assisted, Room Sealed, Gas Fired,
High Efficiency Condensing Regular Boiler Range
British Gas
Service Listed
Nepicar House, London Road,
Wrotham Heath, Sevenoaks,
Kent TN15 7RS
For Technical help or for Service call ...
ALPHA HELPLINE Tel: 0844 871 8764
website: www.alpha-innovation.co.uk