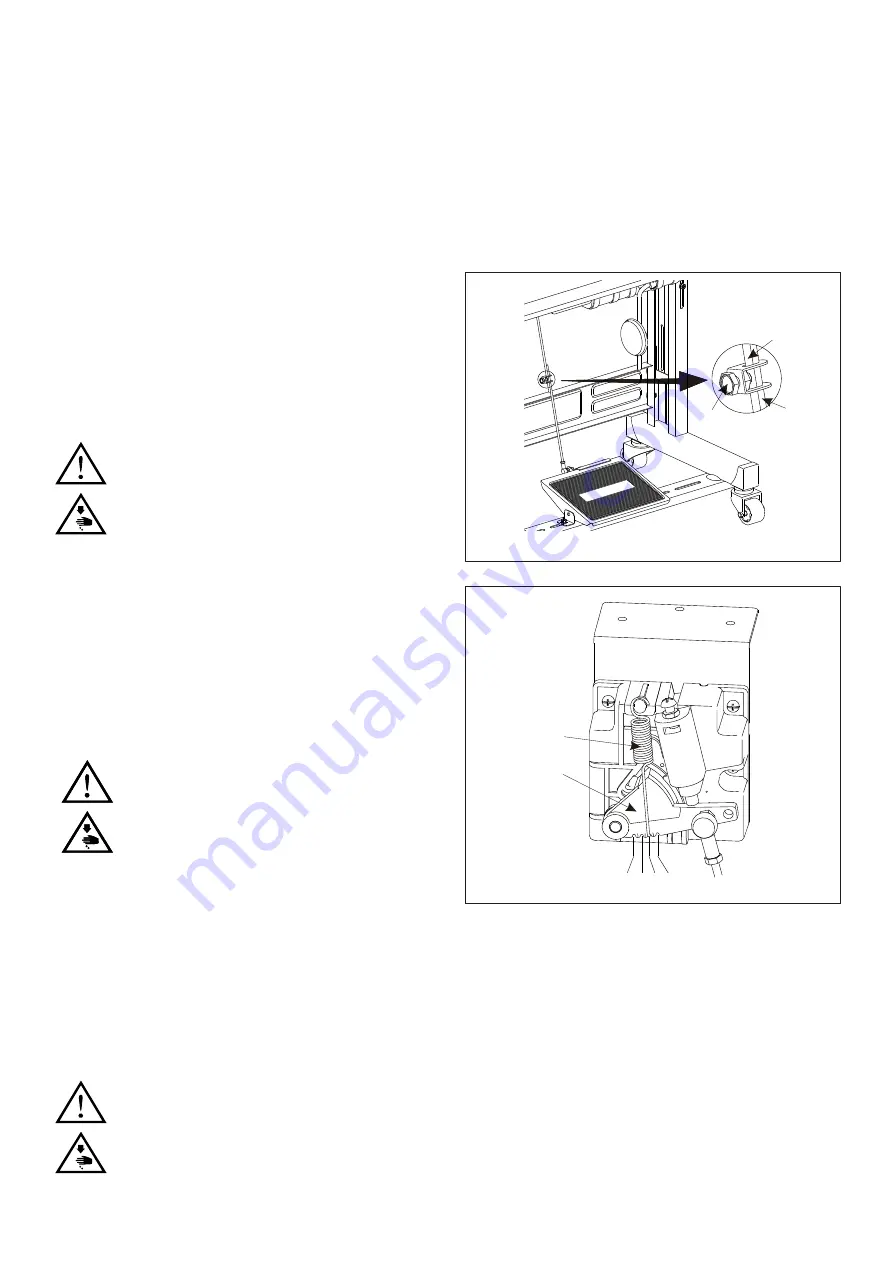
-13-
升动作,继续向后强力踩踏板,压脚下降进行
切线动作,再次进行压脚提升动作。
machine stop switch and thread trimming swit
-ch.The presser foot goes up when you lightly
depress the back part of the pedal(D),and if y
-ou further depress the back part,the thread tr
-immer is actuated.
踏板的调整 (图
19
、图
20
、图
21
)
Adjusting the Treadle(Fig. 19, Fig. 20, Fig. 21)
17
1
.踏板角度的调整
1
)调节踏板连接杆的长度即可以调节踏板
的角度:旋松螺钉
①
,
上下移动上连接杆
②
和
下连接杆
③
就可以调节踏板连接杆的长度。
2
)调节完成后旋紧螺钉
①
。
1.Adjusting the angle of treadle
1)Adjust the angle of treadle only by adjusti
-ng the length of treadle connecting rod: unsc
-rew screw
①
, and adjust the length of treadle
connecting rod by moving upward/downward
the upper connecting rod
②
and lower connec
-ting rod
③
.
2)Screw down screw
①
when adjustment is
over.
注意
:
1.
为了防止缝纫机的意外启动,请关掉
电源之后再进行操作。
Caution:
1.To prevent the unexpected startup
of sewing machine, trim off the pow
-er supply before the operation is co
-nducted.
①
②
③
图
19
Fig.19
2
.踏板踩踏力的调整
将脚放在踏板上并向前轻踩踏板时,缝纫机
进行低速缝纫。如感觉踩踏力比较轻时,将踩
踏力调节弹簧④挂在踏板旋臂拨杆⑤的位置上
进行调节(踩踏力以a为最小,b、c、d依次逐渐
增大)。
图
20
Fig.20
a b c d
④
⑤
注意
:
1.
为了防止缝纫机的意外启动,请关掉
电源之后再进行操作。
2.Adjustment of the strength of pedal
The sewing machine run at a low speed wh
-en step forth on the panel slightly.If the stren
-gth is insufficient, hang the stepping adjust
-ment spring
④
on the panel spiral arm drivin
-g lever
⑤
in order to adjust strength.(a is the
minimum stepping strength ,b,c,d increase g
-radually)