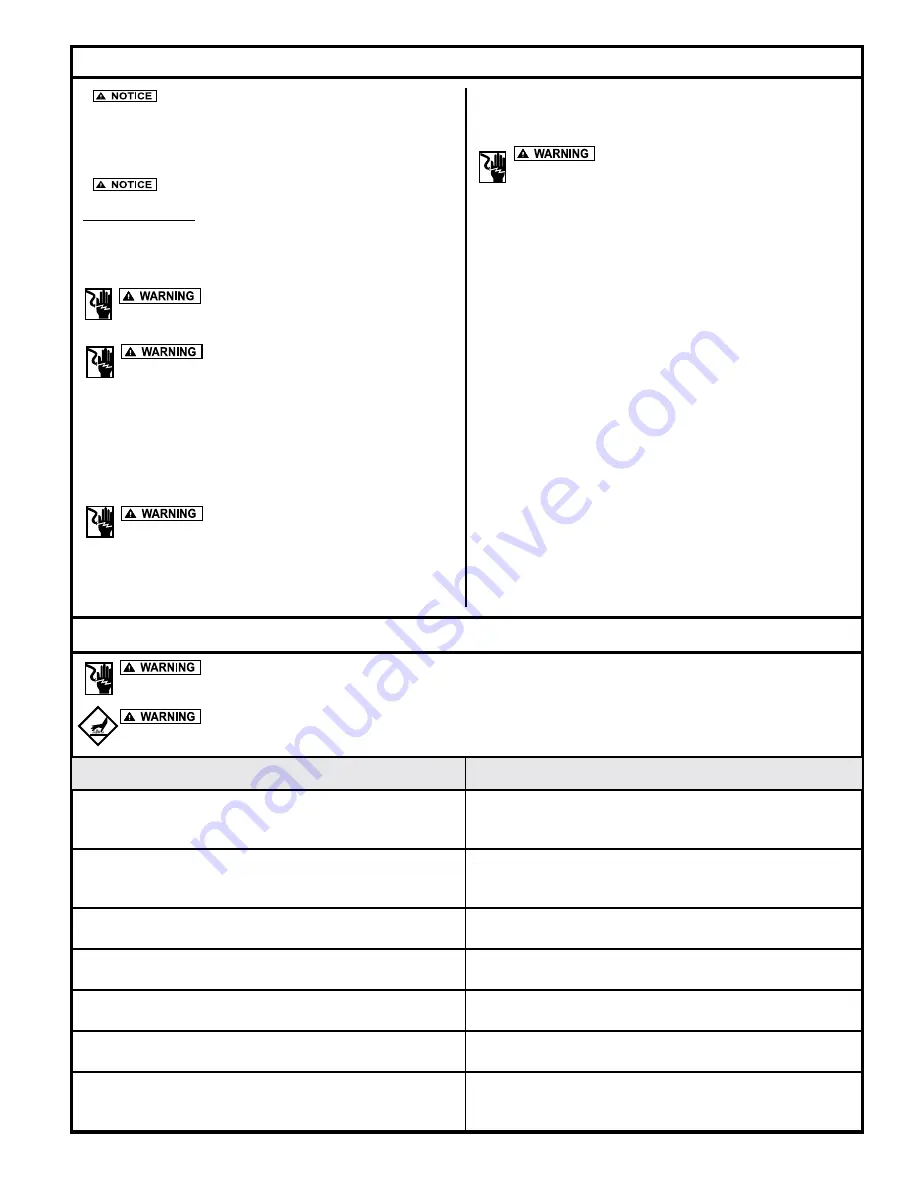
11
© Copyright 2018 Zoeller
®
Co. All rights reserved.
Condition
Common Causes
A. Pump will not start or run.
Blown panel or circuit breaker fuse, low voltage, thermal overload open, defective
capacitor circuit, cutter or impeller clogged, float switch held down or defective,
incorrect wiring in control panel, water in cap assembly.
B. Motor overheats and trips on overload.
Incorrect voltage, impeller or cutter blocked, negative head (discharge lower than
intake of pump). Defective “off” float. Pump runs continuously at low water level.
Low oil level in motor shell.
C. Pump will not shut off.
Air lock, debris under float assembly, defective switch, incoming sewage exceeds
capacity of pump.
D. Pump operates but delivers little or no water.
Intake clogged with grease or sludge, pump air locked (clear vent hole), low
or incorrect voltage, clogged discharge line, operating near shut-off head.
E. Pump starts and stops too often.
Check valve stuck open or defective. Sump pit too small to handle incoming
sewage. Level control out of adjustment. Thermal overload tripping.
F. Large red flashing light comes on at control box.
High water in pit. Check pump for clogging, or overload trip. On single phase
pumps, check the start capacitor in the control panel. See “A” and “D” above.
G. Grease and solids accumulate in pit around pump.
Break up solids and run pump with water running into the pit. Allow level to lower
to the pump intake. Continue until solids are cleared from the pit. Do not drain
kitchen grease down the sink.
Service Checklist
Electrical precautions. Before servicing a grinder pump, always shut off the main power circuit. Make sure you are wearing
insulated protective sole shoes and not standing in water. Under flooded conditions, contact your local electric company or a qualified
licensed electrician for disconnecting electrical service to the pump prior to removal.
Grinder pumps contain oil which becomes pressurized and hot under operating conditions. Allow 2-1/2 hours after shut
down before servicing pump.
General Maintenance
GENERAL SYSTEM INSPECTION
Before the system is placed into operation, it should be inspected by a qualified
technician.
Wiring and grounding must be in accordance with the
National Electrical Code and all applicable local codes and ordinances.
LUBRICATION PROCEDURES
No lubrication is required.
If pumps are to be stored for more than six months, refer to short term storage
procedure in the Operation section.
PREVENTIVE MAINTENANCE
preventive maintenance is recommended to ensure a long service life from the
product. Provided is a suggested maintenance schedule.
Every month:
• Check for proper and unobstructed float operation.
• Listen for proper check valve operation.
• Duplex Units - Check for even operating times. Uneven times indicate a
defective unit, float switch or control.
• Inspect the panel for any presence of moisture in enclosure, loose connections,
and general component condition. check out location and condition of float
switches.
Every year:
• In addition to the monthly checks, the basin should be inspected and cleaned.
Any defective components should be replaced. Inspect and remove any
sand, debris, or mud present in the pump basin assembly.
Every two years:
• Inspect power cables and cap assembly for damage or wear. Replace
immediately if damage or wear is detected by an approved Service Station.
Replace if damage or wear has significantly altered the impeller’s geometry.
• Inspect impeller for damage or wear.
Repair and service must be performed by a firm approved
by Zoeller Company. To repair a pump with an explosion-proof motor in ac-
cordance to the guidelines listed in Policy ZM1462-3c, contact the Zoeller
Product Support Department for additional information.
If the motor housing, seal cavity or cord cap is disassembled
or repaired by a firm not approved to work on explosion proof motors, the
explosion proof rating is void and the FM CSA approval tags
MUST BE
REMOVED FROM THE PUMP.
SAFETY PROCEDURES
For your protection, always disconnect pump and
panel from its power source before handling.
Never enter the basin until it has been properly vented
and tested. Any person entering a basin should be wearing a harness
with safety rope extending to the surface so that they can be pulled
out in case of asphyxiation. Sewage water gives off methane and hydrogen
sulfide gases, both of which can be highly poisonous.
Installation and checking of electrical circuits and hardware should be performed
by a qualified electrician.
Pump is never to be lifted by power cord.
Unit must be cleaned and disinfected, inside the
pumping chamber and all exterior surfaces, prior to servicing.