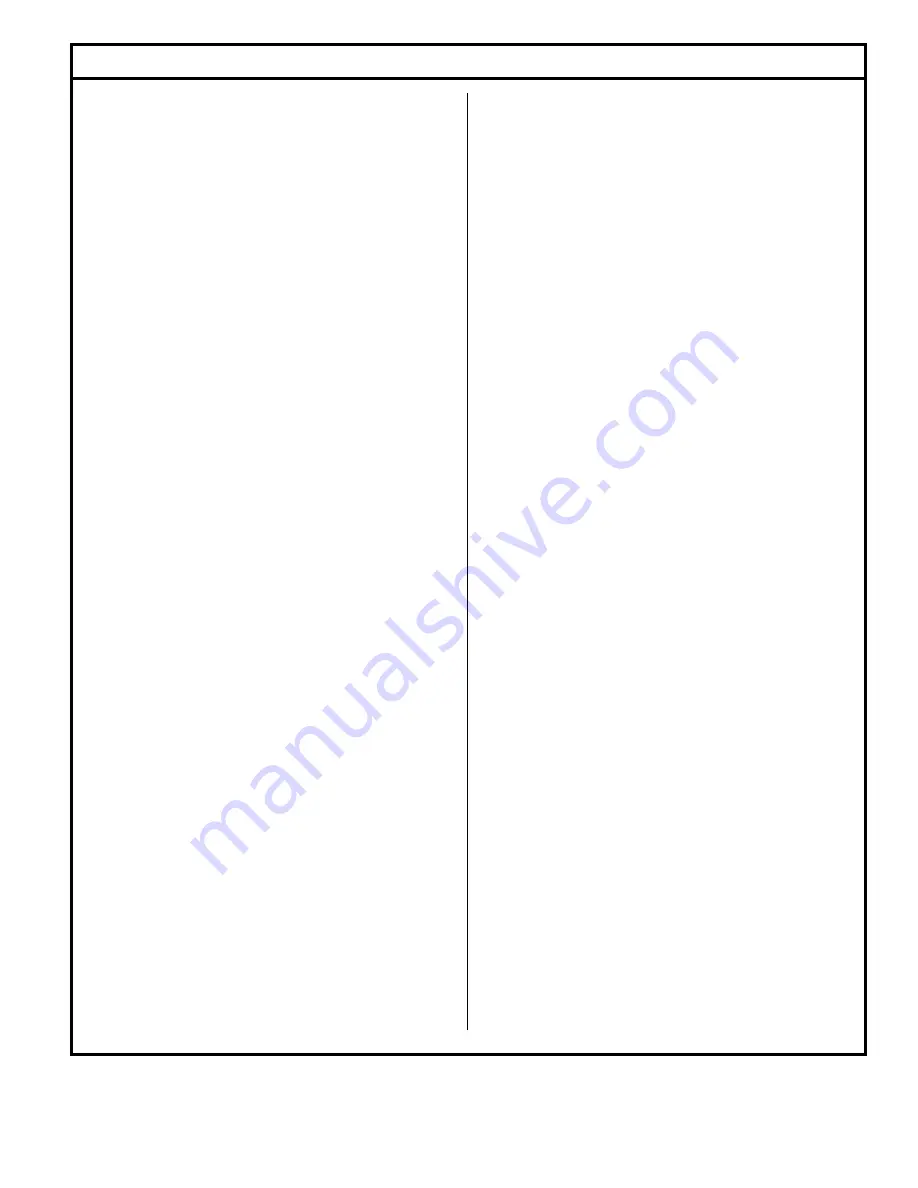
9
© Copyright 2018 Zoeller
®
Co. All rights reserved.
Operation
GENERAL
Zoeller pumps are lubricated and tested at the factory prior to shipment
and require minimum pre-start-up maintenance.
Maximum operating temperature of pump liquid for explosion proof
grinder pumps must not exceed 104 °F (40 °C).
These units are designed for intermittent duty sanitary sewage
applications. If pump is used to dewater areas or pump liquids with
heavy or abrasive materials, the warranty will be voided.
NAMEPLATE DATA
The nameplate, located on the side of the pump, indicates specific
information about the construction of the pump. The model number
and date code information should be recorded on the front page in the
“Owner’s Information” section of this manual.
SHORT TERM STORAGE
Do not install pump until electrical power is available and system
is operational.
When not in use, the pump should be stored and the
following is advised:
• Store pump inside whenever possible or cover with some type of protective
covering.
• Tape or seal in plastic bag the terminal ends of wire leads.
• Spray coat unpainted surfaces with rust inhibiting oil.
• The impeller should be rotated every six months in order to keep the
seals lubricated and not develop a permanent set.
If panel is to be stored, the following is advised:
• Store the panel inside whenever possible and leave in the shipping
box.
• All openings shall be sealed.
• Store in an upright position.
• Do not stack anything on top of panel.
START-UP PROCEDURE
Before placing the equipment into operation the following should be
checked:
• Clean pit.
• Pump, float switches and electrical cables are dry and properly
installed.
• Electrical boxes dry, sealed and securely installed.
• Floats positioned properly.
• Discharge valves open.
• 3/16” vent hole drilled in pipe between check valve and pump.
Once the above has been verified proceed with the following checks:
• Pump power cables and control floats properly installed and voltage
verified.
• Conduit connections to panel are properly sealed.
• After installing the pump into the containment area, with adequate
submergence, open the discharge valve fully. Start the unit using
manual controls. If flow is appreciably less than rated performance,
pump may be air locked. To expel trapped air, jog the unit several
times, using the manual controls.
• Have a qualified electrician take voltage and current measurements
with the pump running. Record these readings in the space provided
in the
“Owner’s Information”
section on page 1 of this manual for
future reference.
ADJUSTMENT PROCEDURE
Pumps: No adjustments are required.
Floats: Refer to the system drawing or to the panel wiring schematic
for the desired location of each float switch setting.
Valves: Discharge valves should be placed in the fully open position.
Systems should not be operated for extended periods of time
with the discharge valves partially closed due to damaging
the valve.
SHUTDOWN PROCEDURES
If a system is shutdown for more than six months, the following is
recommended:
Pumps: If pit is to remain dry, then the pump can remain in the pit.
With the pump in the pit, it should be operated for five minutes
once every three months. If the pit is to remain wet, the pump
should be removed and stored as noted above.
Panels: The panel should have all openings sealed to prevent moisture
and dust from entering the enclosure. Prior to restarting system,
the panel should be inspected for presence of moisture and any
loose connections.
Valves: Consult the valve/actuator supplier for information concerning
these systems components.