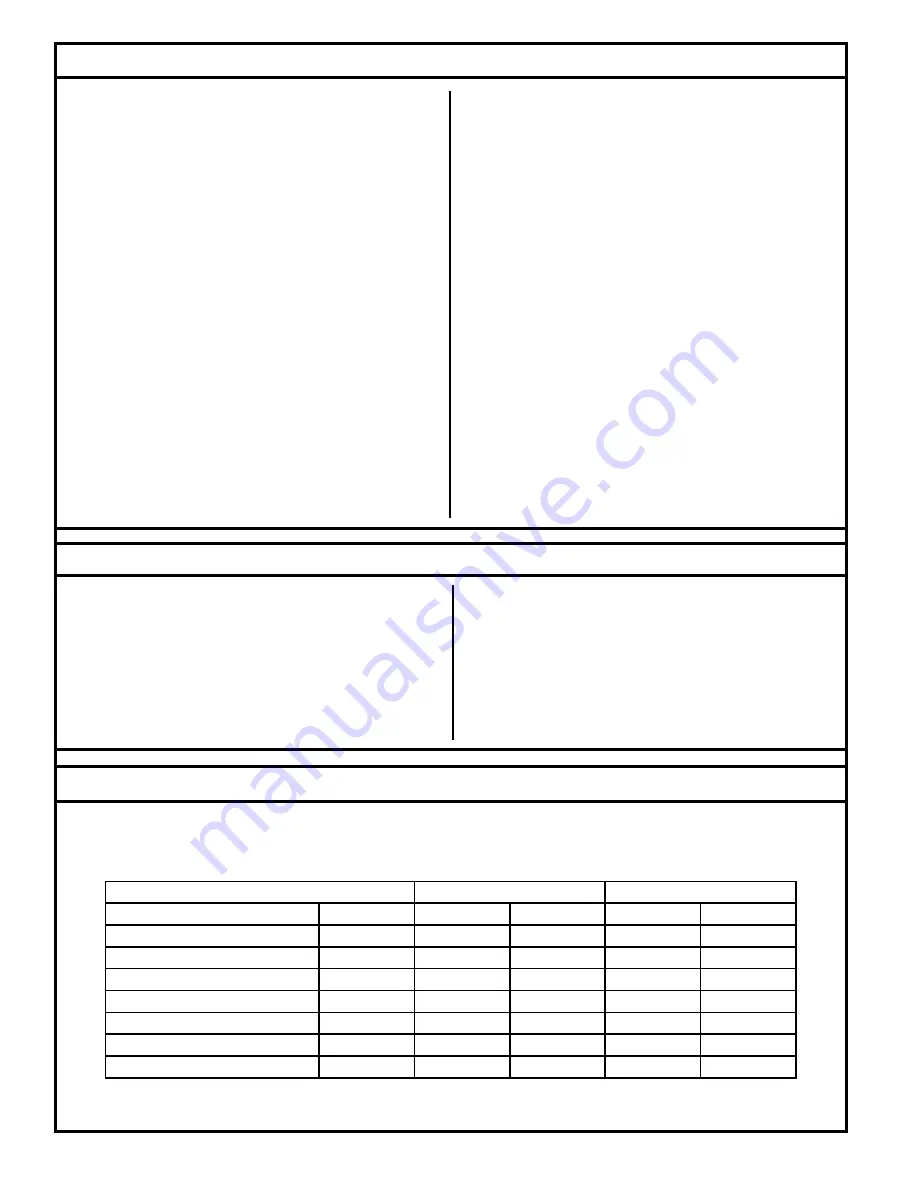
2
© Copyright 2018 Zoeller
®
Co. All rights reserved.
than in raw sewage pumping applications. The warranty set out in the
paragraph above is in lieu of all other warranties expressed or implied;
and we do not authorize any representative or other person to assume
for us any other liability in connection with our products.
Contact Manufacturer at, 3649 Cane Run Road, Louisville, Kentucky
40211, Attention: Customer Service Department to obtain any needed
repair or replacement of part(s) or additional information pertaining to
our warranty.
MANUFACTURER EXPRESSLY DISCLAIMS LIABILITY FOR
SPECIAL, CONSEQUENTIAL OR INCIDENTAL DAMAGES OR
BREACH OF EXPRESSED OR IMPLIED WARRANTY; AND ANY
IMPLIED WARRANTY OF FITNESS FOR A PARTICULAR PURPOSE
AND OF MERCHANTABILITY SHALL BE LIMITED TO THE DURATION
OF THE EXPRESSED WARRANTY.
Some states do not allow limitations on the duration of an implied warranty,
so the above limitation may not apply to you. Some states do not allow
the exclusion or limitation of incidental or consequential damages, so
the above limitation or exclusion may not apply to you.
This warranty gives you specific legal rights and you may also have
other rights which vary from state to state.
LIMITED WARRANTY
Manufacturer warrants, to the purchaser and subsequent owner during
the warranty period, every new product to be free from defects in material
and workmanship under normal use and service, when properly used
and maintained, for a period of one year from date of purchase by the
end user, or 18 months from date of original manufacture of the product,
whichever comes first. Parts that fail within the warranty period, one
year from date of purchase by the end user, or 18 months from the
date of original manufacture of the product, whichever comes first, that
inspections determine to be defective in material or workmanship, will be
repaired, replaced or remanufactured at Manufacturer's option, provided
however, that by so doing we will not be obligated to replace an entire
assembly, the entire mechanism or the complete unit. No allowance
will be made for shipping charges, damages, labor or other charges that
may occur due to product failure, repair or replacement.
This warranty does not apply to and there shall be no warranty for any
material or product that has been disassembled without prior approval
of Manufacturer, subjected to misuse, misapplication, neglect, alteration,
accident or act of God; that has not been installed, operated or maintained
in accordance with Manufacturer's installation instructions; that has been
exposed to outside substances including but not limited to the following:
sand, gravel, cement, mud, tar, hydrocarbons, hydrocarbon derivatives
(oil, gasoline, solvents, etc.), or other abrasive or corrosive substances,
wash towels or feminine sanitary products, etc. in all applications other
APPLICATIONS
1. Zoeller Grinder Pumps are designed for grinding and
pumping sanitary sewage from submersible lift stations.
The pump is intended to grind and pump reasonable
quantities of items normally found in sanitary sewage
applications.
2. Zoeller 7011, 7012 and 7013 Grinder Pumps can be
installed in new applications or as a direct replacement
for any grinder application of like size and capacity.
Some rail system retrofit kits are available.
3. The 7011, 7012 and 7013 can be installed in a
Prepackaged Job Ready System or may be used in a
Field Assembled basin package. Pages 6 and 8 show
a couple of Prepackaged Systems. Field Assembled
Systems are discussed on pages 3 and 4.
4. Zoeller 7011, 7012 and 7013 Grinder Pumps can be
retrofitted to existing positive displacement pump
installations.
*
Zoeller Company does not recommend a simplex station on anything over two homes in order to maintain continuous service during unusual
conditions.
Recommended Limits of Application 7000 Series Grinder Pumps
These recommended application limits are for pump stations pumping to a gravity main. Low-pressure pipe systems should be designed with a
pump located at each house. For applications where a lift station would handle between 15 and 60 homes, consider the 71 Series grinder pump.
For applications where a lift station would handle more than 60 homes, a solids handling type pump should be considered.
Simplex Station
Duplex Station
Model
BHP
Homes
GPD
Homes
GPD
7020 Progressing Cavity Grinder
1
1
400
2
800
7021 Progressing Cavity Grinder
2
1
400
2
800
7010
2
1
400
2
800
7011 w/o Reversing Control
2
2*
800
10
4,000
7011 w/ Reversing Control
2
2*
800
15
6,000
7012
2
2*
800
10
4,000
7013
2
2*
800
10
4,000