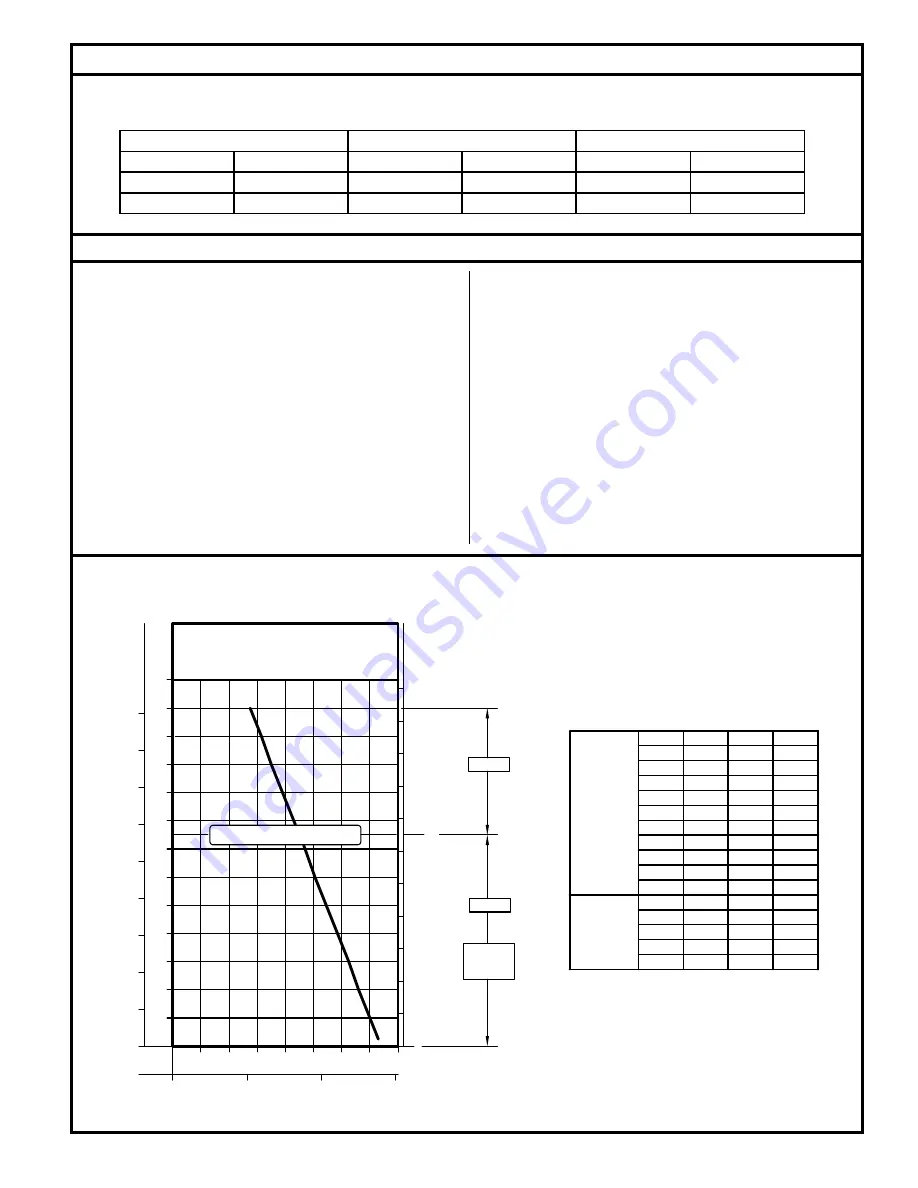
3
© Copyright 2017 Zoeller
®
Co. All rights reserved.
Recommended Limits of Application for Progressing Cavity Grinder Pumps
Simplex Station
Duplex Station
Model
HP
Homes
GPD
Homes
GPD
810
1
1
400
2
800
815
2
1
400
2
800
These recommended application limits are for pump stations pumping to a gravity main. Low-pressure collection systems should be designed with
a pump located at each house. For applications where a lift station would handle more than 2 homes, consider the 840 or 71 Series grinder pump.
For applications where a lift station would handle more than 60 homes, a solids handling type pump should be considered.
General Information
FIGURE 1.
PROGRESSING CAVITY
GRINDER PUMP DESCRIPTION
1. Pumps are constructed of class 30 cast iron protected with powder
coated epoxy for long life when pumping sewage in submersible
applications. The cutter assembly is comprised of stainless steel
components hardened to a value of 55-60 on the Rockwell C scale;
a star shaped cutter and a precision ground flat disk. Cutting action
takes place with the rotation of the cutter blades at 1750 RPM against
the stationary cutter plate (see page 7).
2. The cutter mechanism on the model 810 & 815 is single directional.
3. Pump motors are single phase. Single phase motors require a run
capacitor, which is mounted in the the upper cap of the pump (ref.
page 4). The units have an internal thermal overload.
4. The 810 & 815 progressing cavity grinder pumps are single seal.
5. The pressure relief valve provides motor protection under inadvertent
shut-off head condition.
6. A progressing cavity grinder pump is an intermittent duty pump designed
for pumping sanitary sewage. It is not a dewatering or trash pump.
FIELD ASSEMBLED INSTALLATION
1. Installation and piping instructions are included with the control panel, rail
system and basin instructions. If pump is being retrofitted to an existing
rail system, accessory parts may be required. Consult the factory and
advise make and model of rail system being used.
2. Refer to the appropriate Indoor/Outdoor prepackaged instructions for more
information on system installation.
3. All electrical connections including pump to control box and power supply
to control panels must comply with the “National Electrical Code” and
applicable local codes. Conduit and panel enclosure openings must have
a gas-tight seal. Installation of electrical panels and connections should
be made by a qualified licensed electrician.
4. A properly sized disconnect switch, supplied by others, shall be installed
on the service side of the pump and control panel.
5. When used in a pressure sewer, install an anti-siphon valve (see Fig. 5A).
018330
0
2
4
6
8
10
12
14
16
0
20
40
60
80
100
120
140
160
180
200
260
PUMP PERFORMANCE CURVE
MODEL 810/815
8
16
24
32
40
48
56
64
GALLONS
LITERS
METERS
FEET
TOT
AL
DYNAMIC HEAD
FLOW PER MINUTE
220
240
72
20
40
60
10
20
30
40
50
60
70
80
90
100
110
0
PSIG
TOT
AL
DYNAMIC HEAD
2 HP
1 HP
LOW PRESSURE SEWER
TYPICAL
OPERATING
RANGE
DESIGN PRESSURE (150 FT OR LESS)
TOTAL DYNAMIC HEAD/FLOW
PER MINUTE
MODEL
Feet
810
Meters
Gal.
Liters
MODEL
815
5
10
20
6.1
3.0
1.5
14.6
55
40
60
18.3
12.2
80
100
30.5
24.4
120
36.6
140
150
45.7
42.7
55
53
50
47
44
41
38
36
34
14.4
14.0
13.2
12.5
11.7
10.9
10.1
9.4
9.0
160
48.8
180
54.9
200
61.0
220
67.1
240
73.2
5.5
33
30
27
24
21
8.6
7.8
7.0
6.3