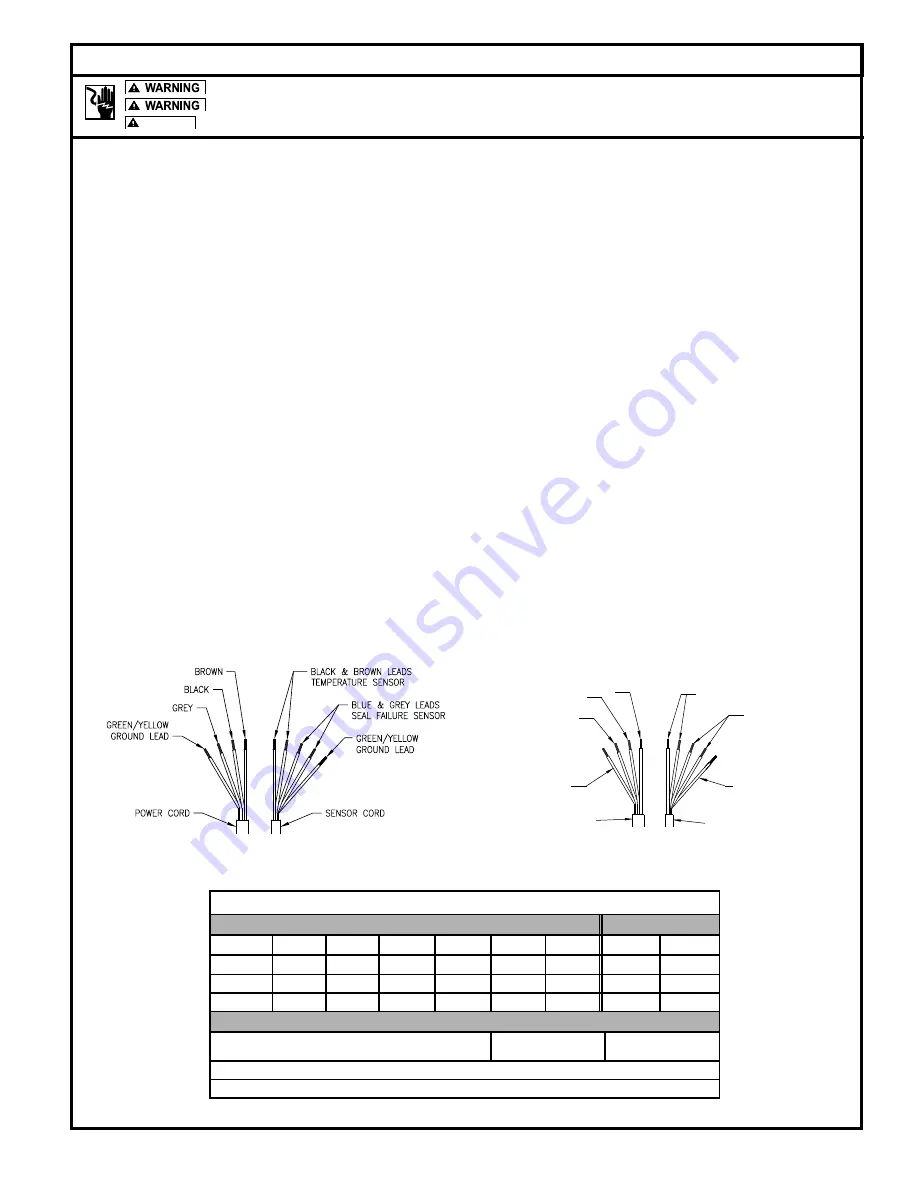
5
© Copyright 2011 Zoeller Co. All rights reserved.
Installation and checking of electrical circuits and hardware should be performed by a qualified licensed electrician.
“Risk of electrical shock”
Do not remove power supply cord and strain relief or connect conduit directly to the pump.
CAUTION
Power cords, sensor cords, and float cords all must be sealed to prevent gases from the basin entering the control panel.
INSTRUCTIONS FOR CHECKING ROTATION OF THREE PHASE UNITS
It is very important that these units be connected for proper rotation. Since no rotating parts are visible without removing the pump from the pit,
the rotation on 3 phase units should be checked before installation into the pit as follows:
After the proper electrical connections are made, momentarily energize the pump observing the direction of kick back due to starting torque. The rotation is
correct if the kick back is in the opposite direction of the rotation arrow. If the rotation is not correct, disconnect power and switch any two power leads. Turn
power back on and retest for proper rotation.
THERMAL SENSOR PROTECTION
Two thermal sensors and leads are wired in series with each other and located adjacent to the motor windings. When the temperature exceeds the maximum
recommended limit, the pump will deactivate when the lead wires are connected to the magnetic starter circuit of a control panel with the thermal cutout feature.
Continual deactivation of this circuit requires attention from maintenance personnel.
MOISTURE SENSORS
(1) Pumps with moisture sensors have a separate sensor cord in addition to the power cord.
(2) Sensor cord conductors are connected to sensors probes in the lower seal cavity. The conductor wires are terminated in the control panel for activating
an indicator light when moisture is present in the lower seal cavity.
(3) When the moisture indicator light is activated, the lower seal has allowed leakage of water into the lower oil-filled seal cavity. The pump should be serviced
within 30 days to avoid damage to the motor and bearings.
(4) Oil in the motor housing and lower seal cavity must be checked when pump is serviced. If oil from the motor housing contains water or other contamination,
both seals should be replaced during maintenance. Always replace with new factory recommended oil and service parts. All warranty repairs must be
made by Zoeller Authorized Service Stations.
(5) On existing applications where the control panel only has one moisture sensor hookup per pump, one moisture sensor lead from the pump should be
hooked to the moisture sensor lead in the panel, the other moisture sensor lead from the pump should be hooked to ground to complete the circuit.
(6) Moisture sensor circuit can be checked for continuity (complete circuit) with a (Volt-OHM-Meter). Set the VOM to read resistance and connect the VOM
leads to the sensor cord black and white wires. The VOM should read approximately 330k Ohms. Resistance readings significantly lower indicate a seal
leak with water in the seal chamber. If VOM reading is open then a problem exists with moisture sensor circuit.
(7) Check resistance between the green ground conductor of the pump power cord and the sensor cord black and white wires. This resistance reading should
indicate an open circuit. If VOM reading returns a reading other than open, then a problem exists with the sensor circuit wiring or cordage. If resistance
readings show a problem with either test, then pump should be repaired by a Zoeller Authorized Service Station.
CONTROL PANELS
These pumps are nonautomatic. They require a control panel. A motor starter circuit, control circuit, and alarm circuit within the panel are standard features.
Outdoor enclosures and alternating relays are often required. Variable level float switches are the most common level sensing device. The following should be noted.
(1) Single phase units require externally mounted capacitors and starting relays. Your control panel should have provisions for mounting these starting components.
(2) The seal failure sensor and thermal sensor protection require that interfacing terminals and functions be incorporated into the panel.
(3) All pumps require overload protection in panel. Use with approved motor control that matches motor input in full load amperes with overload element(s)
selected or adjusted in accordance with control instructions.
Pump Wiring Instructions
“71 SERIES GRINDER” FOUR CONDUCTOR POWER CORD SIZE
60Hz
50Hz
MODEL
230/1PH
200/3PH
230/3PH
380/3PH
460/3PH
575/3PH
380/3PH-STD
380/3PH-CE
7110
8 AWG
12 AWG
12 AWG
12 AWG
12 AWG
12 AWG
12 AWG
H07RN-F4G4
7111
8 AWG
8 AWG
12 AWG
12 AWG
12 AWG
12 AWG
12 AWG
H07RN-F4G4
7112
N/A
8 AWG
8 AWG
12 AWG
12 AWG
12 AWG
12 AWG
H07RN-F4G4
APPROXIMATE CORD DIAMETER
12 / 4 AWG apprx. = 0.64"
8 / 4 AWG apprx. = 0.93"
H07RN apprx. = 0.58"
STANDARD SENSOR CORD 18/5 AWG. APPROXIMATELY 11mm (0.43") DIAMETER
CE VERSION SENSOR CORD H07RN-F5G1 APPROXIMATELY 11mm (0.43") DIAMETER
POWER AND SENSOR CORD, LEAD IDENTIFICATION, CE MODEL
ZEPA0640
SEAL FAILURE
BLACK & WHITE
LEAD
GROUND
POWER
CORD
LEAD
SENSOR CORD
GREEN GROUND
BLACK
GREEN
RED
WHITE
SENSOR
LEADS
TEMPERATURE
RED & ORANGE
SENSOR
LEADS
POWER AND SENSOR CORD, LEAD IDENTIFICATION
ZEPA0039E