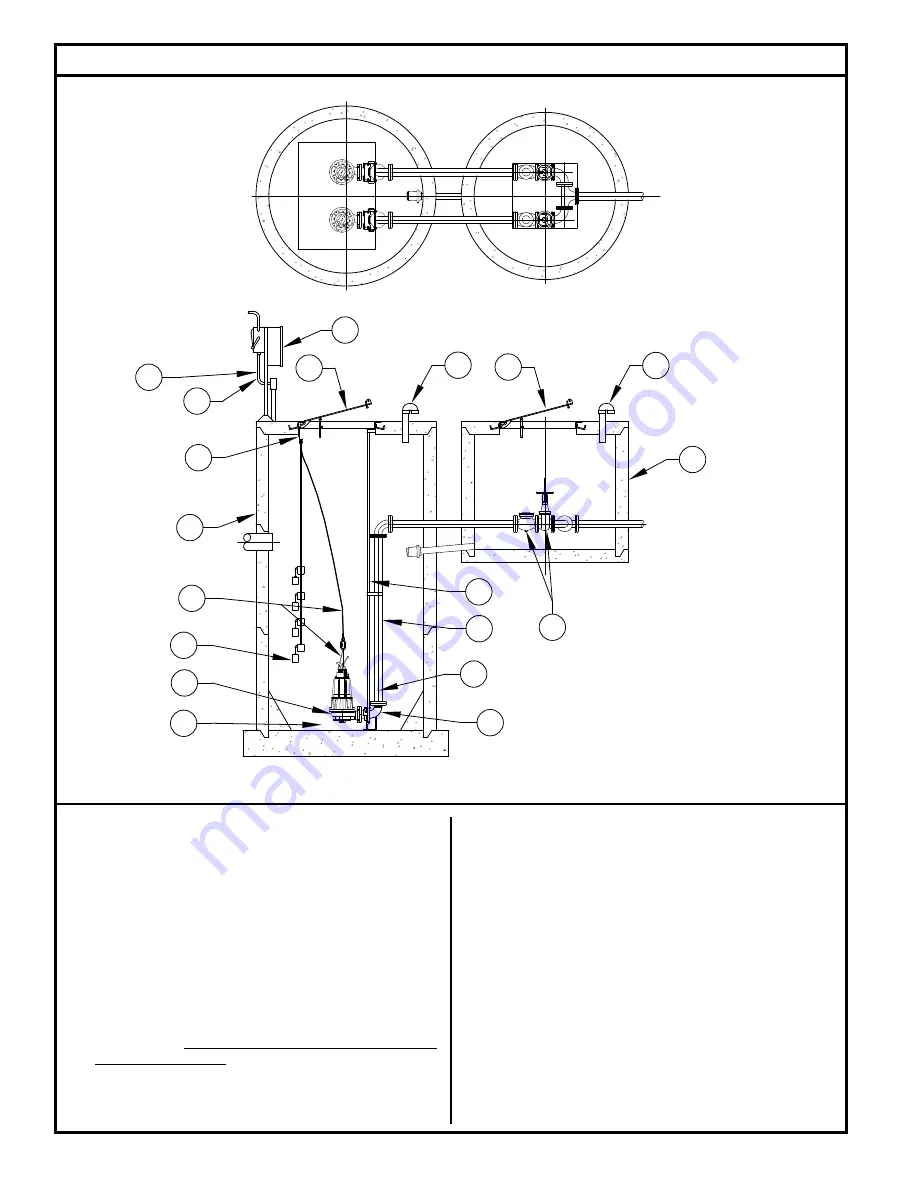
4
© Copyright 2011 Zoeller Co. All rights reserved.
3
1
4
4
7
7
10
8
10
2
11
14
6
13
9
6
12
5
15
Typical Grinder Pumping System Installation
(8) Secure power cord to avoid entanglement with variable level
float switch mechanism.
(9)
Do not
reduce pump discharge pipe below 2” (51mm) IPS size.
(10) Basin
must
be in accordance with all applicable codes
and specifications. Basin must be sized to allow a minimum
3 minute off-time between starts.
(11) Pump must be level and the tethered variable level float switches
must be free and not hang up on pump or pit peculiarities.
(12)
If
a rail system is used, discharge elbow
must
be firmly an-
chored to the bottom of basin. In fiberglass basin, the bottom
will need to be reinforced if the discharge elbow is used.
(13)
If
a rail system is used, the guide rails are 2” (51mm) schedule
40 pipe for all units. Brass, stainless steel or galvanized steel
is recommended.
(14) Install ring and cable for lifting pump from pit.
(15) Basin must be clean and free of debris after installation and
before operation.
ZEPA0521
All installations must comply with all applicable
electrical and plumbing codes, including, but
not limited to, governing electrical code, local,
regional, and/or state plumbing codes, etc.
(1) Electrical wiring and protection
must
be in accordance with the
governing electrical code, and any other applicable state and
local electrical requirements.
(2) Install proper full flow check and shut-off valve.
(3) Install proper controls. (Outdoor panels
require
NEMA 3R or 4X
enclosure)
(4) All installations
require
a basin cover to prevent debris from
falling into the basin and to prevent accidental injury.
(5) Cords must be properly sealed to prevent moisture and gases
from entering the control panel.
(6)
When check valve is installed
, drill a 3/16" (5mm) diameter
hole in the discharge pipe below the check valve even with the
top of the pump. NOTE: The hole must be below the basin cover
and cleaned periodically. Also a vent hole is drilled in the pump
housing. Be sure that this hole is cleared during any servicing.
(7) Vent gases and odors to the atmosphere through vent pipe per
Local and State codes.