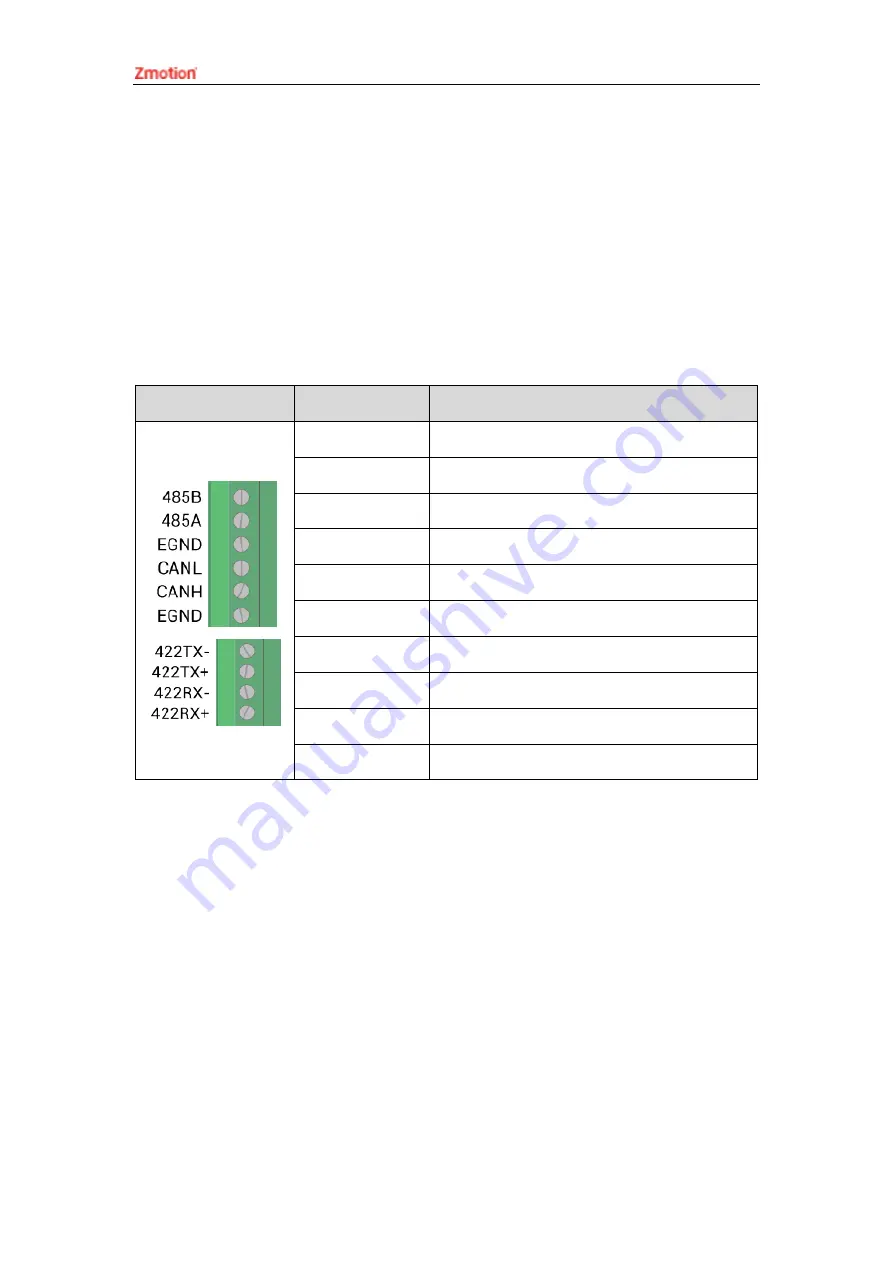
ZMC306X Motion Controller User Manual V1.5
3.2.
RS485, RS422, CAN Communication Interfaces
The communication interface adopts a 10Pin screw-type pluggable wiring terminal and
the gap spacing between 2 terminals should be 3.81mm. This terminal is shared by
controller RS485, CAN and RS422 communication. It supports MODBUS_RTU protocol
and custom communication.
→
Terminal Definition:
Terminal
Name
Function
485B
485-
485A
485+
EGND
External power supply ground
CANL
CAN differential data -
CANH
CAN differential data +
EGND
Communication public end
422TX-
RS422 send -
422TX+
RS422 send +
422RX-
RS422 receive -
422RX+
RS422 r
3.2.1.
RS485, RS422, CAN Specification & Wiring
The RS485 serial port supports the MODBUS_RTU protocol and custom
communication, mainly including 485A, 485B and public end.
The RS422 serial port supports the MODBUS_RTU protocol and custom
communication, mainly including 422TX-, 422TX+, 422RX-, 422RX+ and public end.
The CAN interface of the controller adopts the standard CAN communication
protocol, which mainly includes three ports, CANL, CANH and the public end. And it can
connect ZIO/ZMIO expansion modules and other standard CAN devices.
Summary of Contents for ZMC306X
Page 1: ......