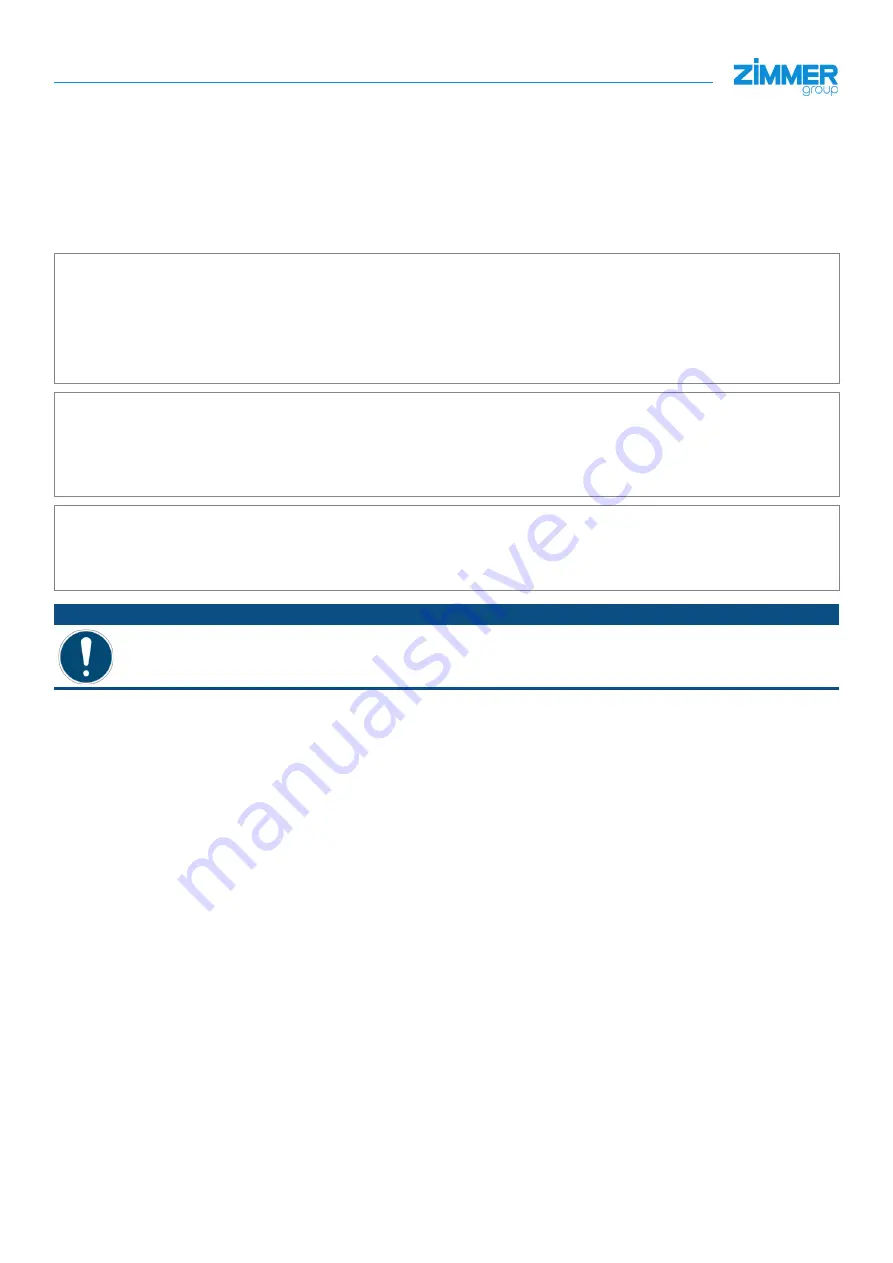
INSTALLATION AND OPERATING INSTRUCTIONS:
startZ Universal Robots
49
Zimmer GmbH
•
Im Salmenkopf 5
•
77866 Rheinau, Germany
•
+49 7844 9138 0
•
+49 7844 9138 80
•
www.zimmer-group.com
EN / 2020-11-30
DDOC01095 / 0
10
Operation
The Zimmer Comfort URCap can be found on the left side of the "Polyscope program" tab under the "URCaps/Zimmer"
section.
The chapter „9.3.7 Controller-I/O: Speichern der Greiferkonfiguration“ describes how the Zimmer node can be used in the
robot program.
10.1 Zimmer gripper control principle
Preparation (only for advanced grippers):
1.
Reference run, if necessary (Z_Homing)
2.
Check if the reference run is OK (Z_IsHomingOk or Z_IsHomingSuccess)
3.
Switch on motor (Z_MotorOn)
4.
Check whether the motor is switched on (Z_IsMotorOn)
5.
If no error (Z_IsError), prepared
Operation A (advanced)
1.
If more than one workpiece is used, adjust the workpiece ( Z_Ch number) that was preconfigured with
Zimmer IO-Link HMI
2.
Checking if the workpiece is changed (Z_IsWpC number)
Operation B (basic):
1.
Grip (Z_Grip) or release (Z_Release) the workpiece.
2.
Check the position of the gripper fingers (Z_IsOnTeachPos , Z_IsOpened, Z_IsClosed or Z_IsOnUndefPos)
NOTICE
If workpieces to be switched have different gripping directions, using the reset command (Z_Reset) is
recommended. This command resets the gripping direction flag.