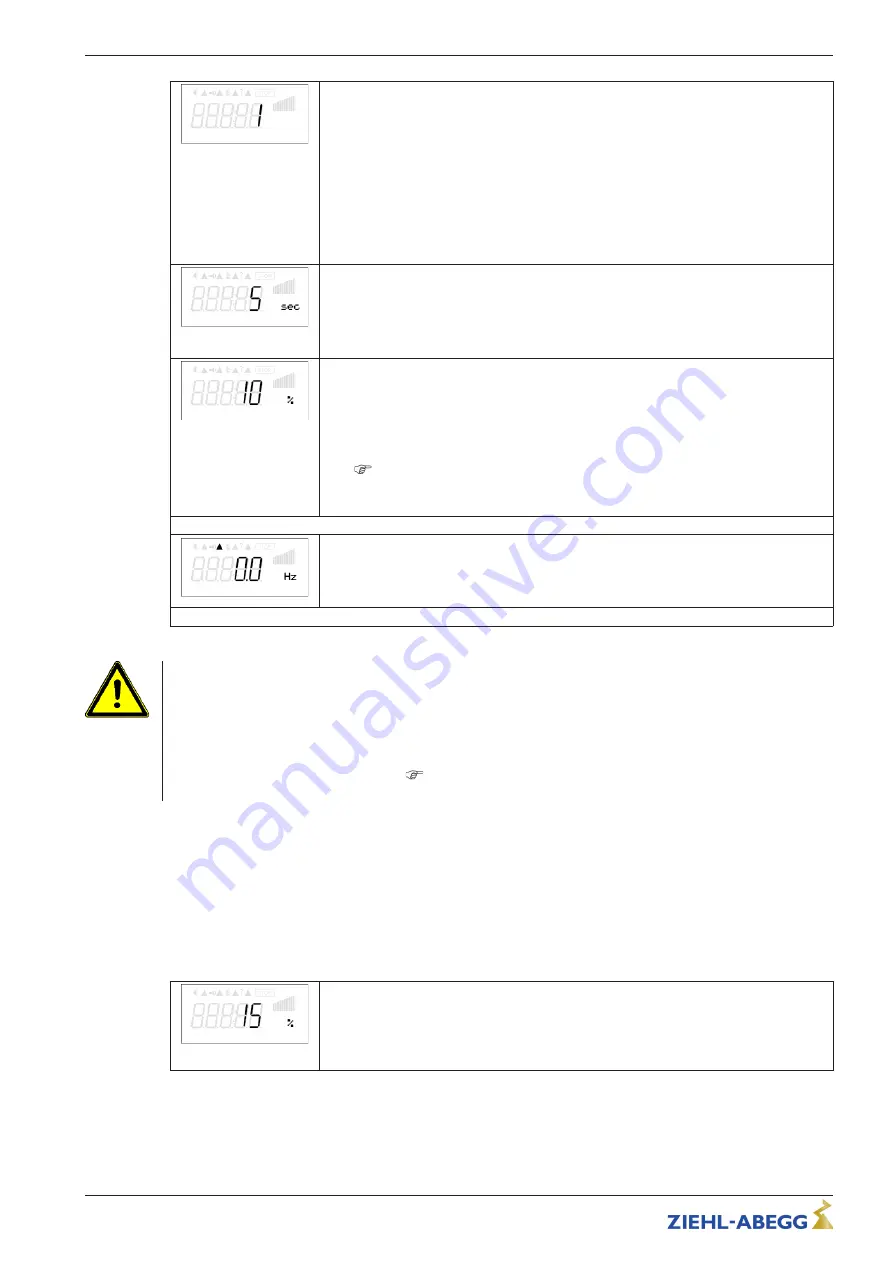
DC brake mode
DC brake mode
Setting function of DC-brake for frequency inverters.
0
= no brake function.
1
(factory setting) = brakes before start (before modulation is returnd)
2
= Special function, brakes before stop (as soon as modulation
“
0
”
).
The motor does not run out up to stop. The motor is braked actively, as soon as no
modulation is present (Setpoint =
“
0
”
or Enable =
“
OFF
”
) .
DC brake time
DC brake time
Maximal length of DC-brake for frequency inverters.
If the braking is activated, the d.c. brake torque is active for this time.
Setting range: 0...250 sec.
Factory setting: 5 sec.
DC brake level
DC brake level
Direct-current voltage level, generated for braking. The higher this value, the greater
the braking effect. The setting is dependent on the size of the ventilator / motor.
Attention! Values that are too high, will result in an excessive braking effect and
possibly lead to actuation of the overload shutoff.
Same setting affects also the function
“
Motorheating
”
(only for type with function
“
12D
”
IO Setup).
Setting range: 0...50 %
factory setting: 10 / 50 % (depending on device type)
Frequency
Active brake mode is signaled by a bright triangle in the display.
Attention!
•
Safe starting of fans is not guaranteed if it is started in reverse. If the application demands safe
starting, the machine manufacturer or owner must prevent reverse driving rotation by suitable
measures.
•
With the frequently one behindthe other following DC bracings it can come to strong heating up of
the motor. To prevent any overheating, motor protection in the form of a temperature limiter
installedin the motor is required (
motor protection).
•
Test required. The
“
min. speed
”
adjustment must be set to
“
0
”
.
7.15.8
Setting Boost value
The boost function is an automatic voltage increase when the control system is under dynamic
requirements. When using the square characteristic curve, the output voltage is increased dispropor-
tionately to the frequency during a 20% increase of the modulation. That results in more torque on the
motor so the current does not increase so strongly during accelerations. Just before reaching the
modulation default value, the motor voltage that corresponds to the square characteristic curve is
restored. The boost mode is only used during suf
fi
ciently large modulation increases (starting from ca.
20 %).
Boost Value
You can determine the amount of voltage increase via the percentage setting. 15 %
boost value increase voltage by 15 % over normal value of the square characteristic
curve.
Setting range: 0...25.0 %
Factory setting: 15.0 %
Operating Instructions
Fcontrol
–
model series FTET4/6/10AHMQ-L
The Installation menu
L-BAL-E139-GB 2022/03 Index 006
Part.-No.
52/92