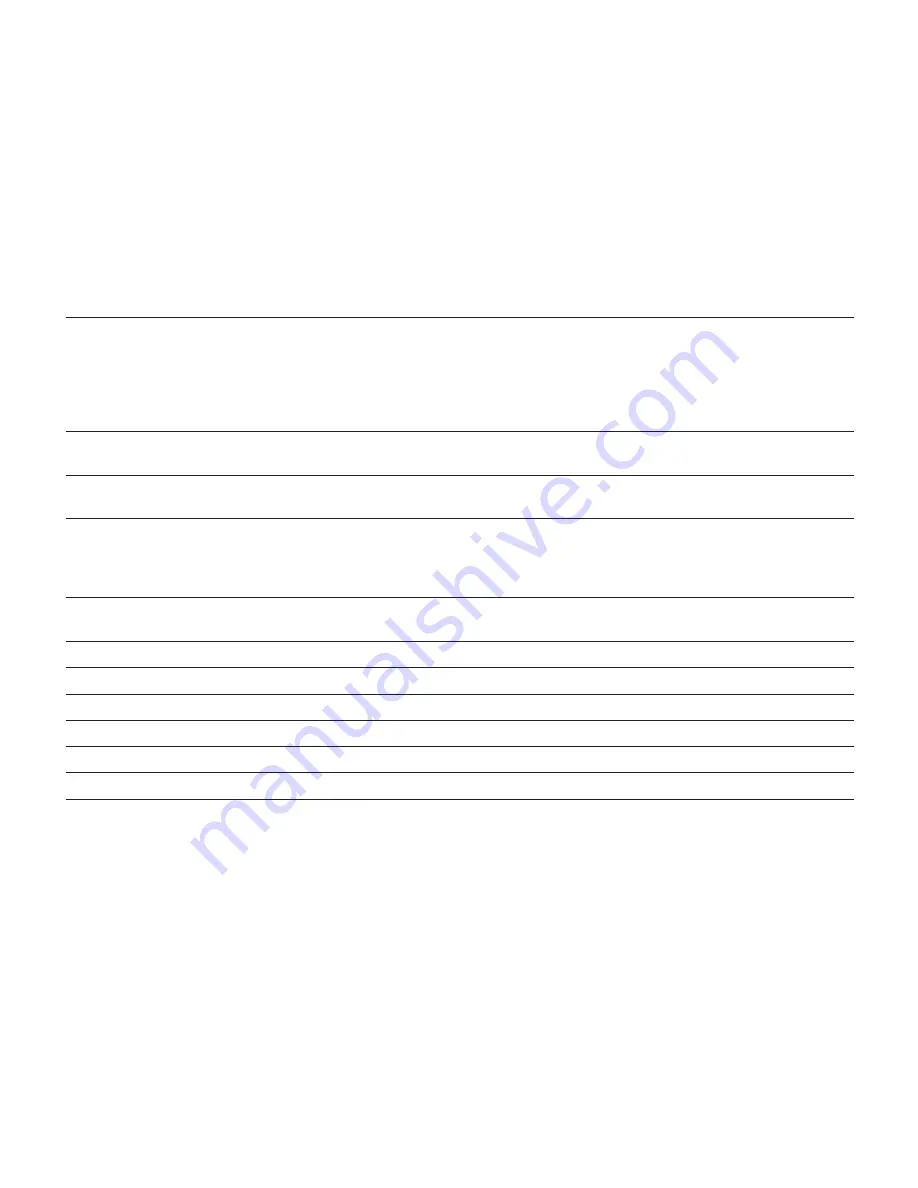
Technical Data
Electronic control unit ERM
6057 758 101 - 2005-02
10
1.3 Circuit board configuration
Designation
Function
LED (1)
“Power”
Supply voltage is applied and ERM program is ready.
LED (2)
“Feedb.”
Closed-loop control operating mode, i.e. DIL switch position 5 and 6 = “1”.
LED (3)
• Ø sensing operation, DIL switch position 5 = “1” and 6 = “0” or
“Ø-Contr.”
• Ø calculation operation, DIL switch position 5 = “0” and 6 = “1”.
• LED “Ø-Contr.” flashes, if the setting procedure has not been carried
out in the operating mode Ø calculation or Ø sensing.
Connection for
Diagnostic connector for ZF MOBiDIG tester
diagnostic unit
K-cable, acc. to ISO 9141
Jumper
For function selection. e.g. feed rate interruption, emergency brake
Fuse
Fine-wire fuse 4 A, medium time-lag fuse
DIL switches
Setting of various operating modes and unit sizes
Program memory
Includes microprocessor operating program
Data memory
Contains operating parameters
Terminal strip
18-pin