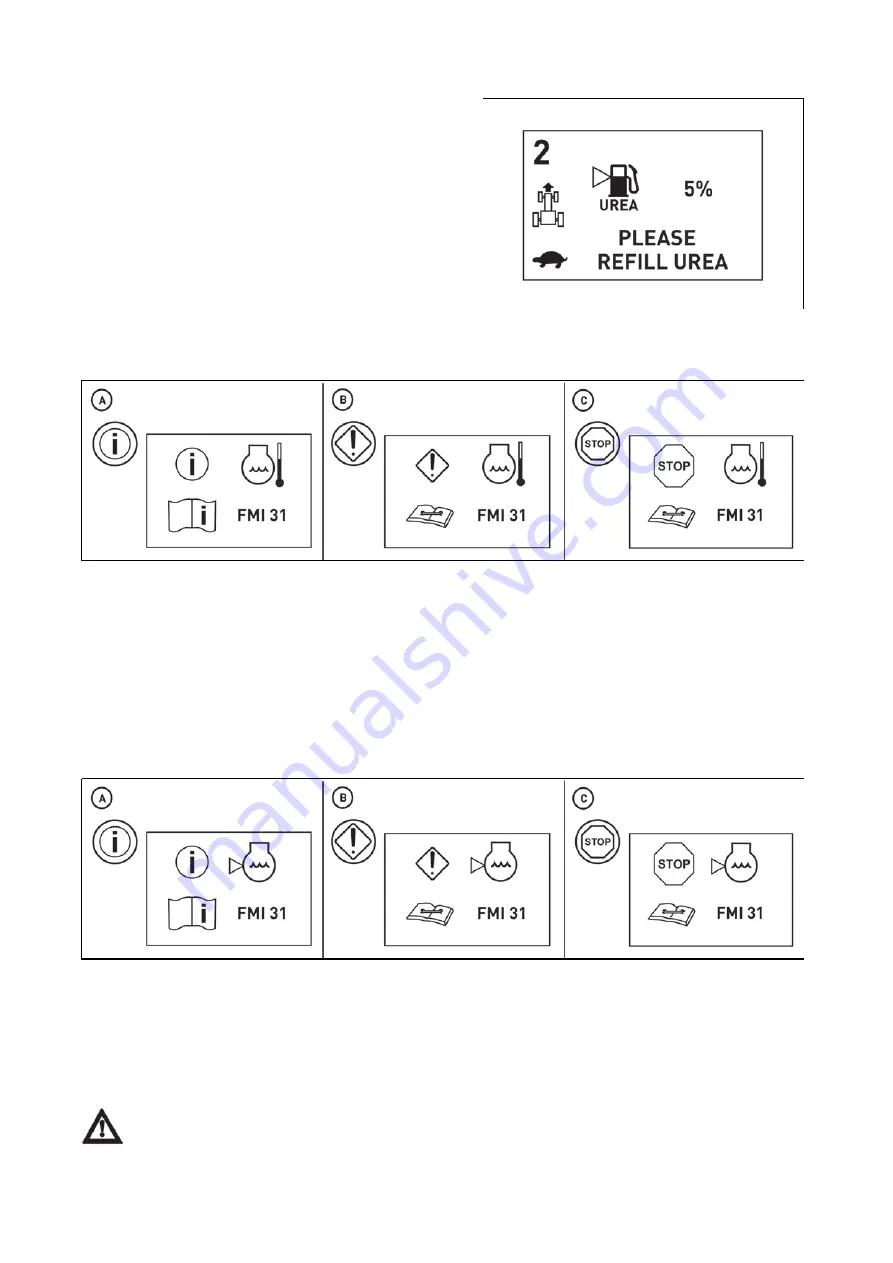
Add urea
High temperature of the cooling liquid
C15N112
High temperature of the cooling liguid is indicated in several stages of warning
A - informative - reduce the engine power
B - warning - stop the tractor, set the engine to idling until the temperature of the cooling liquid is reduced
C - caution - stop the engine, wait until the temperature of the cooling liquid is reduced and check the level of
the cooling liquid; if the cooling liquid starts to be overheated again when the engine is started, stop the
engine and contact the service centre
Low level of the cooling liquid
C15N113
Low level of the cooling liguid is indicated in several stages of warning
A - informative
B - warning - the cooling liquid must be replenished
C - caution - stop the engine, wait until the temperature of the cooling liquid is reduced and replenish the
cooling liquid
Do not release the overpressure plug unless the cooling liquid is cold! Danger of scald burns!
When the level of the urea tank content drops, the prompt
for the addition of urea and the amount of urea in the tank
in percentage of the tank volume are shortly displayed on
the display.
C15N151
DASHBOARD
61
Summary of Contents for CRYSTAL Series
Page 1: ...150 160 Tractor is Zetor Since 1946 OPERATOR S MANUAL CRYSTAL 1 2015...
Page 3: ...2...
Page 11: ...10...
Page 89: ...NOTES 88...
Page 95: ...NOTES 94...
Page 123: ...NOTES 122...
Page 127: ...NOTES 126...
Page 131: ...NOTES 130...
Page 163: ...NOTES 162...
Page 167: ...NOTAS 166...
Page 180: ...NOTES 179...