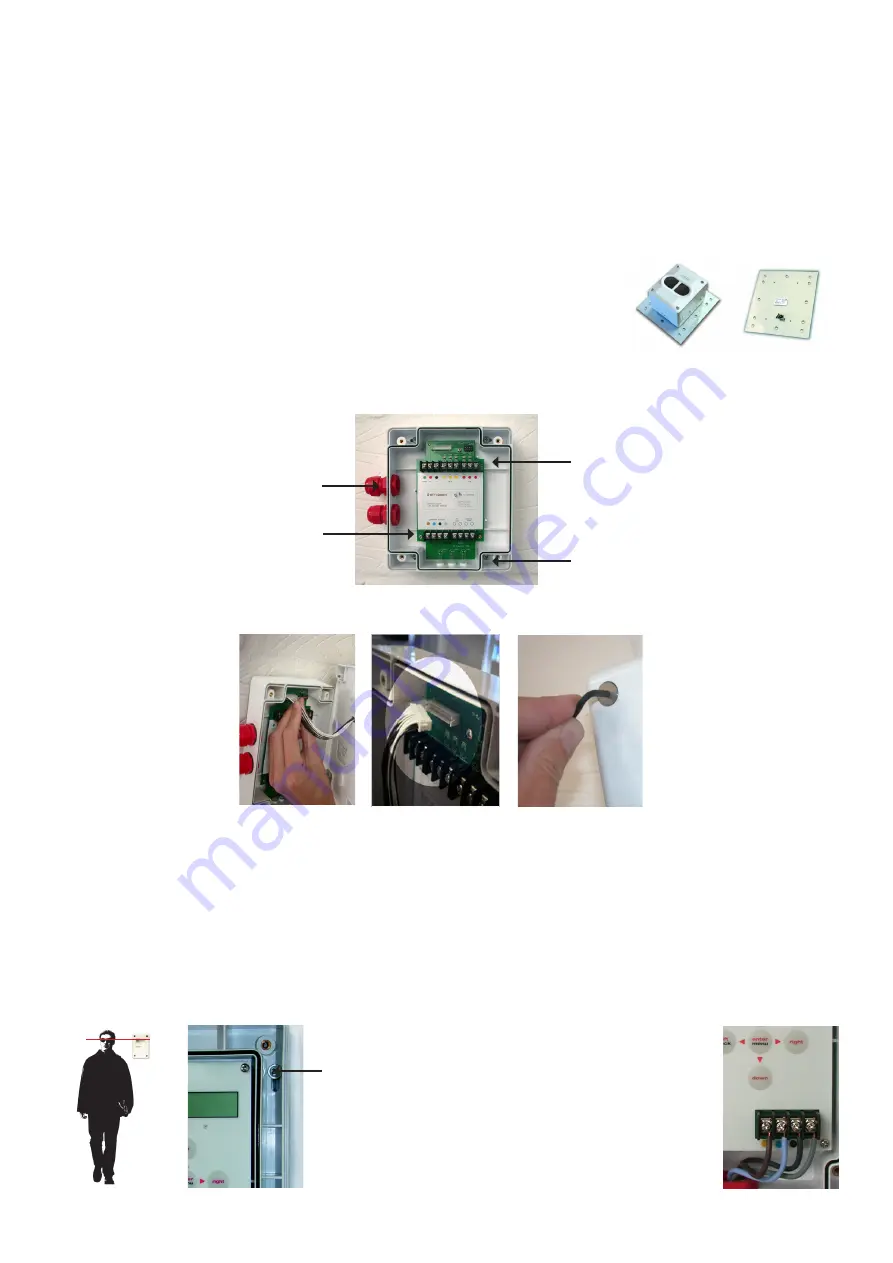
2 Installing, commissioning and testing
step 1 mounting the head
Screw the head backing plate to the wall - always try to use as sturdy a location as possible, such
as brick or major structural steels (avoid mounting to outer metal cladding etc). Avoid mounting the
head where direct sunlight can shine directly into the ‘eyes’ of the beam (care should be taken when
mounting in glass atriums). Ambient sunlight will not affect the beam.
Also available - unistrut adapter plate
Use this accessory for easy mounting to unistrut fabrication. Holes are pre-
drilled to the correct pitch of the head and conveniently positioned for use
with unistrut.
step 2 mounting the controller
Important
mount the controller at eye level and ensure easy access.
Screw in through holes provided outside of the
rubber seal. Wire to head using colour coded
terminals.
If this connection is not made ERROR
will appear on the controller, this connection can
be checked by reading the resistance across the
black and grey terminals, they will read 110 ohm if
OK or 220 ohm if not connected properly.
2 knock-outs are provided on
both sides.
Take care when using
drills not to damage the circuit
board.
Screw the head screws
down with the 3mm
allen key provided.
Your
wiring should be flush
and not flattened by
tightening down screws.
Wire to low level controller using
bottom colour coded terminals.
Wire into system as required (see
generic wiring diagram on the
following page).
Ensure that all
wiring is below the level of the
front edge of the box.
Screw in through holes provided
outside of the rubber seal.
Connect the head
to the base plate by
first plugging in the
connector.
Do not
force
in, whitewires should be
uppermost.
Should you
forget to connect this
the controller screen
will read ERROR.
To avoid damaging the detector head never dangle the front
cover assembly from the ribbon
Important
ensure the
connector is this way up