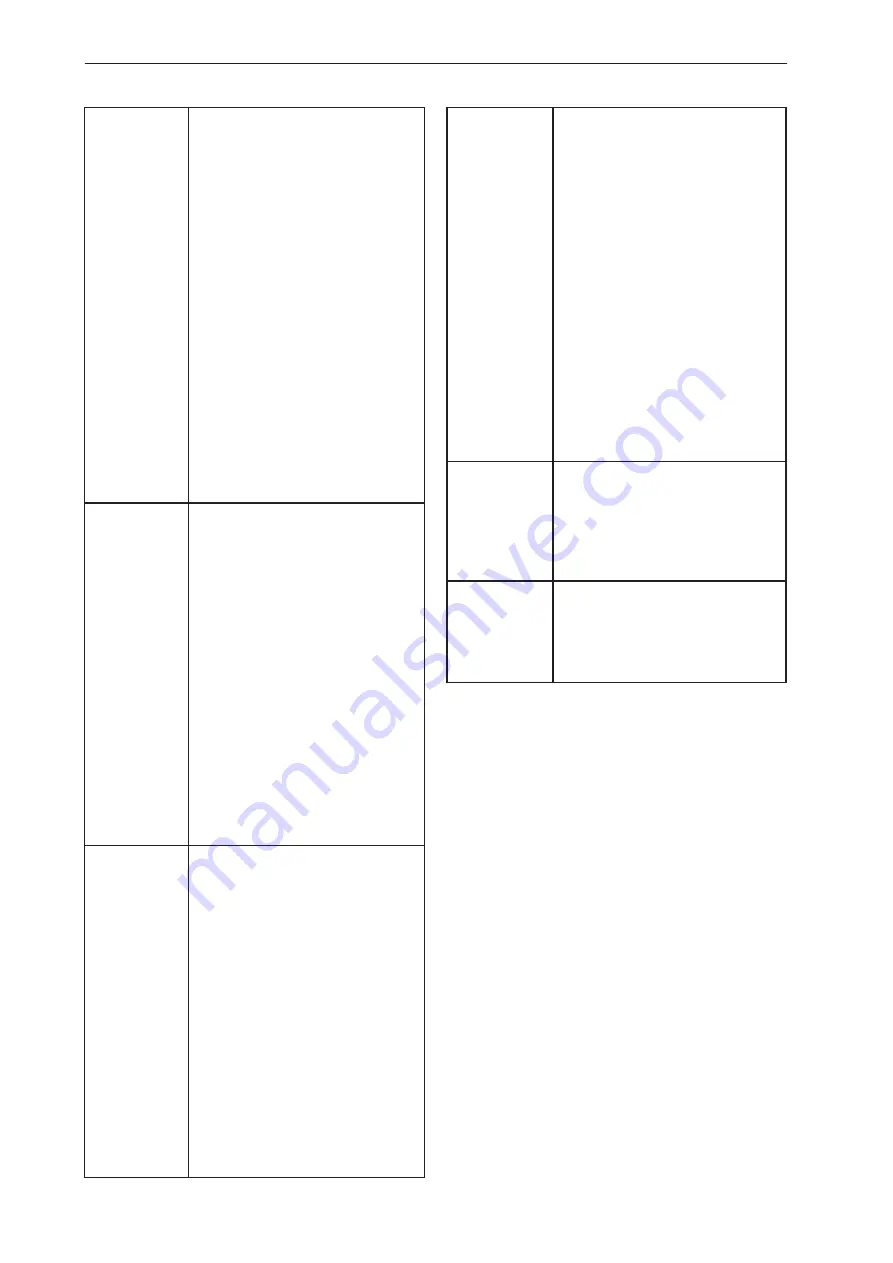
59
- English
Troubleshooting
Acceleration och retardation
Does not
accelerate
Engine stalls
when throttle
released
Over rich
acceleration
Adjust L screw
Adjust H screw
Blocked air filter
Blocked fuel tank vent
Blocked fuel filter
Fuel line blocked
Loose or damaged fuel hose
Impulse channel blocked
Loose cover on carburettor pump
side
Faulty pump diaphragm
Leaking air intake hose (rubber)
Loose carburettor mounting bolts
Needle valve set too low
Metering system incorrectly
assembled
Needle valve assembly sticking
Faulty diffuser jets
Blocked silencer
Adjust L screw
Adjust H screw
Faulty pump diaphragm
Needle valve set too high
Needle valve assembly sticking
Faulty diffuser jets
Adjust L screw
Adjust H screw
Blocked air filter
Faulty pump diaphragm
Faulty diffuser jets
8.2 Troubleshooting methods
In addition to the faults described in the above
table, trouble shooting can be carried out on
specific components or sub-systems of the chain
saw. The various procedures are described in
the relevant chapters, see the contents page, as
follows:
• Checking the operation of the chain brake
• Measuring the resistance of the stop plate
• Pressure testing the carburettor
• Pressure testing the decompression valve
• Pressure testing the cylinder
High rpm
Will not run at
full throttle
Low power
Will not “four-
stroke”
Adjust H screw
Blocked air filter
Blocked fuel tank vent
Blocked fuel filter
Fuel line blocked
Loose or damaged fuel hose
Impulse channel leaking
Impulse channel blocked
Loose cover on carburettor pump
side
Faulty pump diaphragm
Leaking air intake hose (rubber)
Loose carburettor mounting bolts
Needle valve set too low
Metering system damaged
Metering system incorrectly
assembled
Leaking control diaphragm/cover
plate
Needle valve assembly sticking
Blocked silencer
Adjust H screw
Blocked fuel tank vent
Blocked fuel filter
Impulse channel leaking
Impulse channel blocked
Loose cover on carburettor pump
side
Faulty pump diaphragm
Blocked air filter
Needle valve assembly sticking
Leak in metering system (air or
fuel)
Metering system incorrectly
assembled
Loose diaphragm rivet
Hole in diaphragm
Leaking control diaphragm/cover
plate
Blocked fuel tank vent
Blocked fuel filter
Fuel line blocked
Loose or damaged fuel hose
Impulse channel leaking
Impulse channel blocked
Loose cover on carburettor pump
side
Faulty pump diaphragm
Leaking air intake hose (rubber)
Loose carburettor mounting bolts
Needle valve set too low
Leak in metering system (air or fuel)
Metering unit incorrectly assembled
Loose diaphragm rivet
Hole in diaphragm
Leaking control diaphragm/cover
plate
Summary of Contents for GZ4350
Page 1: ...Workshop Manual English GZ4350...
Page 2: ......
Page 5: ...English 4 Index...
Page 12: ...11 English 11 12 9 4 Service tools Service tools 4 3 8 1 2 7 10 5 6 13 14 15 16 17...
Page 15: ...English 14 Service data...
Page 61: ......