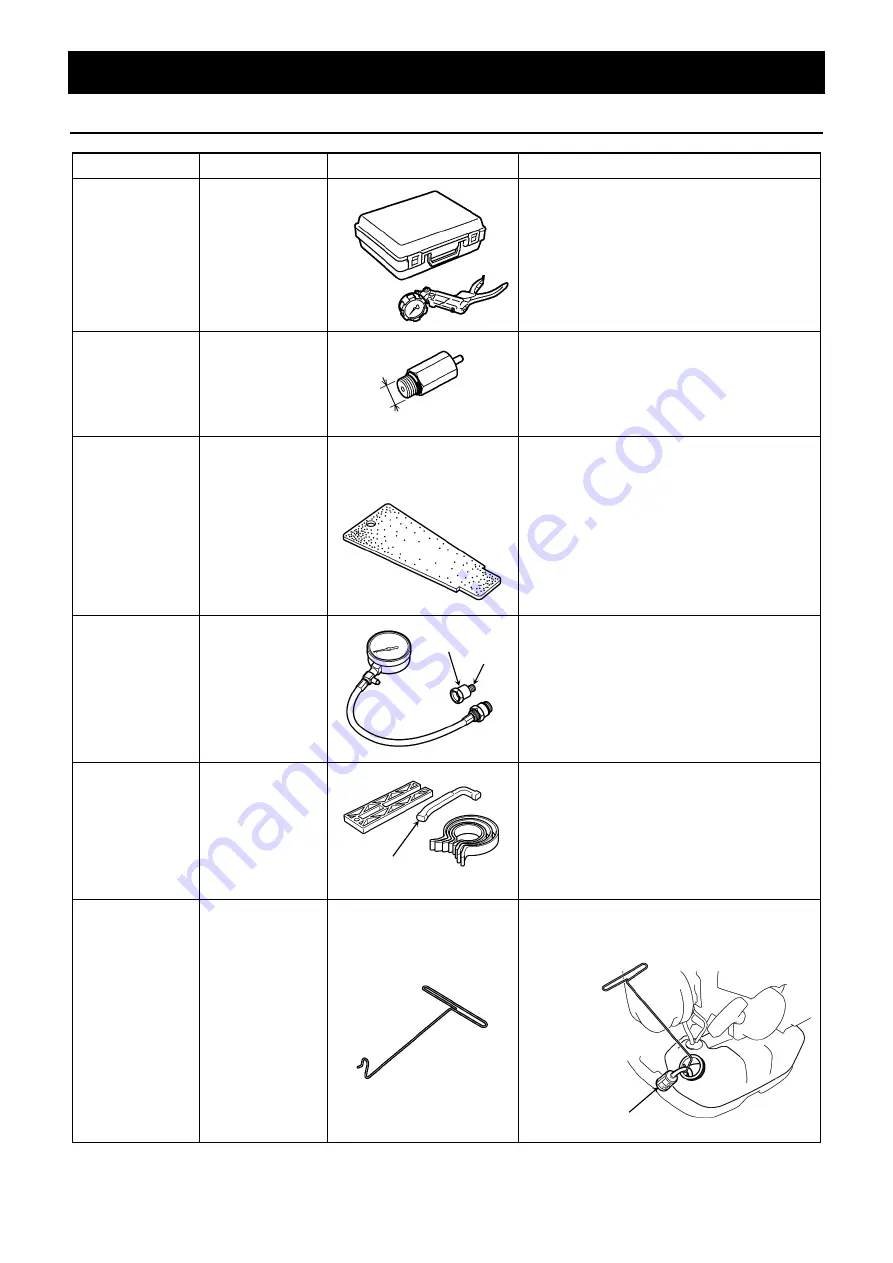
-12-
5.
Special Tools
5-1 Description
Tool Name
Tool Number
Appearance
Usage
Pressure
Vacuum Gauge
H531030623
Engine seal check (see page 19)
Pressure Tester
Attachment
H503844001
Set in the hole of the spark plug, and
connect the pressure gauge
(see page 19).
Outlet Cover
Plate
H502541102
Closure of exhaust port and inlet port
(see page 19)
Compression
Gauge (
φ
14mm)
Adapter Size:
(
φ
10mm)
H531031686
583 84 98-01
Compression pressure check
(see page 18)
Piston Fitting Kit
H502507001
Piston installation (see pages 17 and 20)
Fuel Filter Hook
H502508301
Suspending the fuel filter
Fuel Filter
φ
10
Adapter
φ
10
Stopper
Do not use.
φ
10