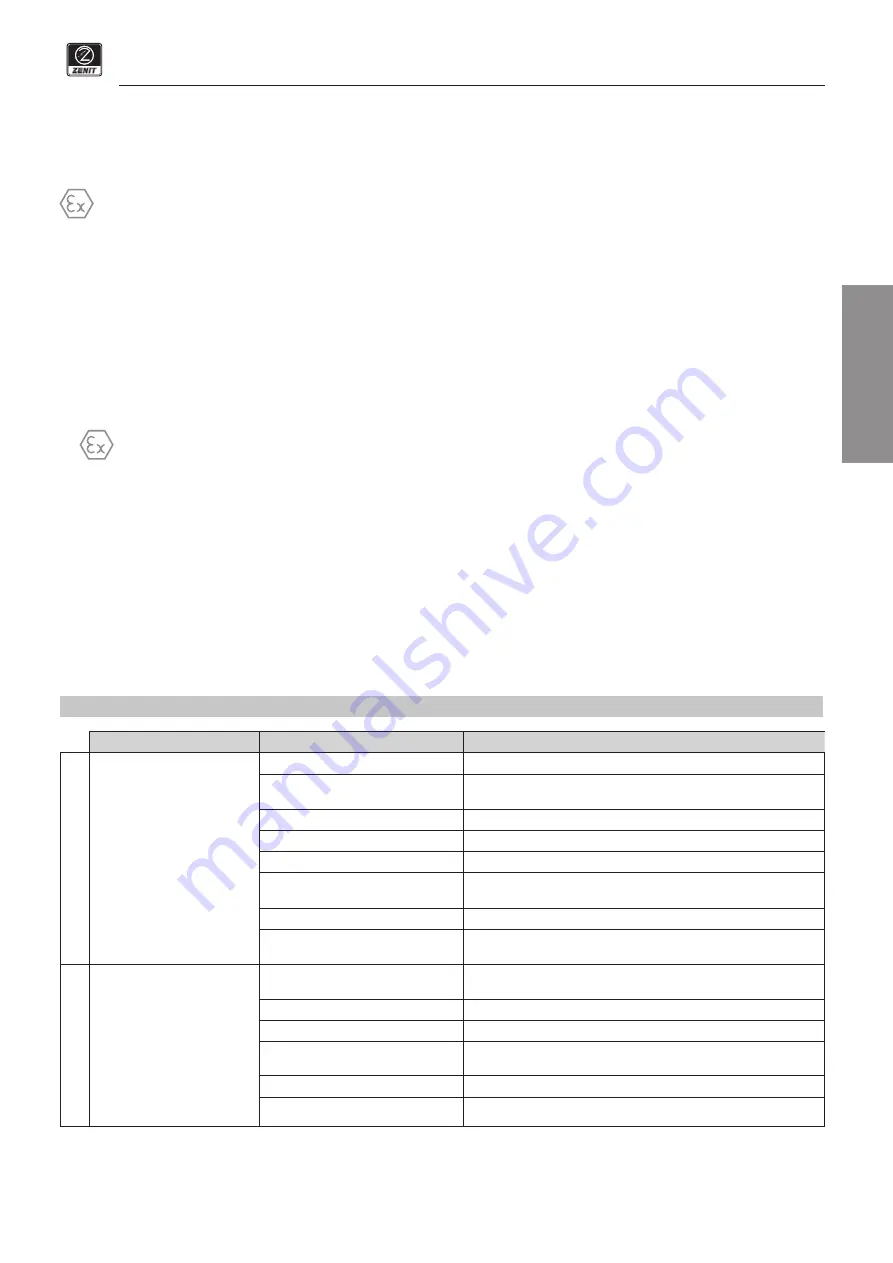
15
water solutions
First installation manual – Translation of original instructions
Do not use the pump if malfunctioning because sudden failure of the rotating parts may cause hazardous situations or damage
to the motor.
If the hydraulic part is fouled, clean it thoroughly.
Pumps in normal operation must be inspected every 4000 hours of operation or at least once a year. If the pumped liquid is very
muddy or sandy, a short inspection period is necessary.
Check the wear conditions of the bearings, the mechanical seals and all other parts subject to wear, since particularly unfavo-
rable or incorrect installation conditions can be a cause of ignition hazard.
A maintenance plan with a maximum interval of 2 years must be scheduled; re-conditioning must include the replacing of bea-
rings, mechanical seals (oil change included) and weared pump parts. Do not reuse rubber parts.
If the pump is used only occasionally, after each use flush out the hydraulic part to prevent the formation of deposits; run the pump for a few cycles
with clean water.
Also take care not to allow sediments to form on the float switches, to ensure that the start and stop thresholds remain correct.
5.4 Inspection
•
Bearings inspection
All bearing are rolling element type grease lubricated for life. Check the shaft noisy or heavy operation (turn the shaft by hand) and in case,
replace the defective ball bearings.
Defective bearings may reduce the -Ex safety.
•
Mechanical seals inspection
When the pump is new or after mechanical seals replacement, check the oil level. The oil must be changed after 4,000 operating hours or
once a year. Oil change and mechanical seals inspection is necessary if the leakage probe detects an ingress of water into the seal chamber.
Oil chamber is designed in order than, filling it with the pump in vertical position, the right quantity of the lubricate is reached when its level
reach the hole for the filling (oil plug).
Use CASTROL PRODUCT L320 oil or similar.
•
Cable inspection
Make sure that the electrical cables aren’t sharply bent and/or pinched or damaged in any way.
6. TROUBLESHOOTING GUIDE
PROBLEM
POSSIBLE CAUSE
SOLUTION
1
The pump doesn’t start
No power supply
Check power supply line.
Damaged or disconnected cable
Check the cable connections and make sure that it’s not dama-
ged.
Fuses blowed
Check fuses type and rating and replace them with correct ones.
Tripped circuit breaker
Refer to Point 3.
Tripped thermal protector
Refer to Point 2.
Damaged or wrongly connected
capacitor (single phase motor)
Replace the capacitor and check that it’s correctly connected.
Tripped level control
Check that the level sensor is correctly connected and functioning
Broken, burned or disconnected
wiring
Check the status of wiring and connections.
2
The thermal protection trips
after a short operating time
The pump is immersed in a liquid
which is too hot
Cool down the liquid.
Clogged hydraulic
Clean the hydraulic parts and remove the blocking material
Blocked rotor
Contact an authorised service center.
Uncorrect voltage
Check that the supplied voltage matches with the one on the
pump’s nameplate
Fault in bearings
Contact an authorised service center.
Starts per hour exceed the permitted
number
Refer to Point 6
EN