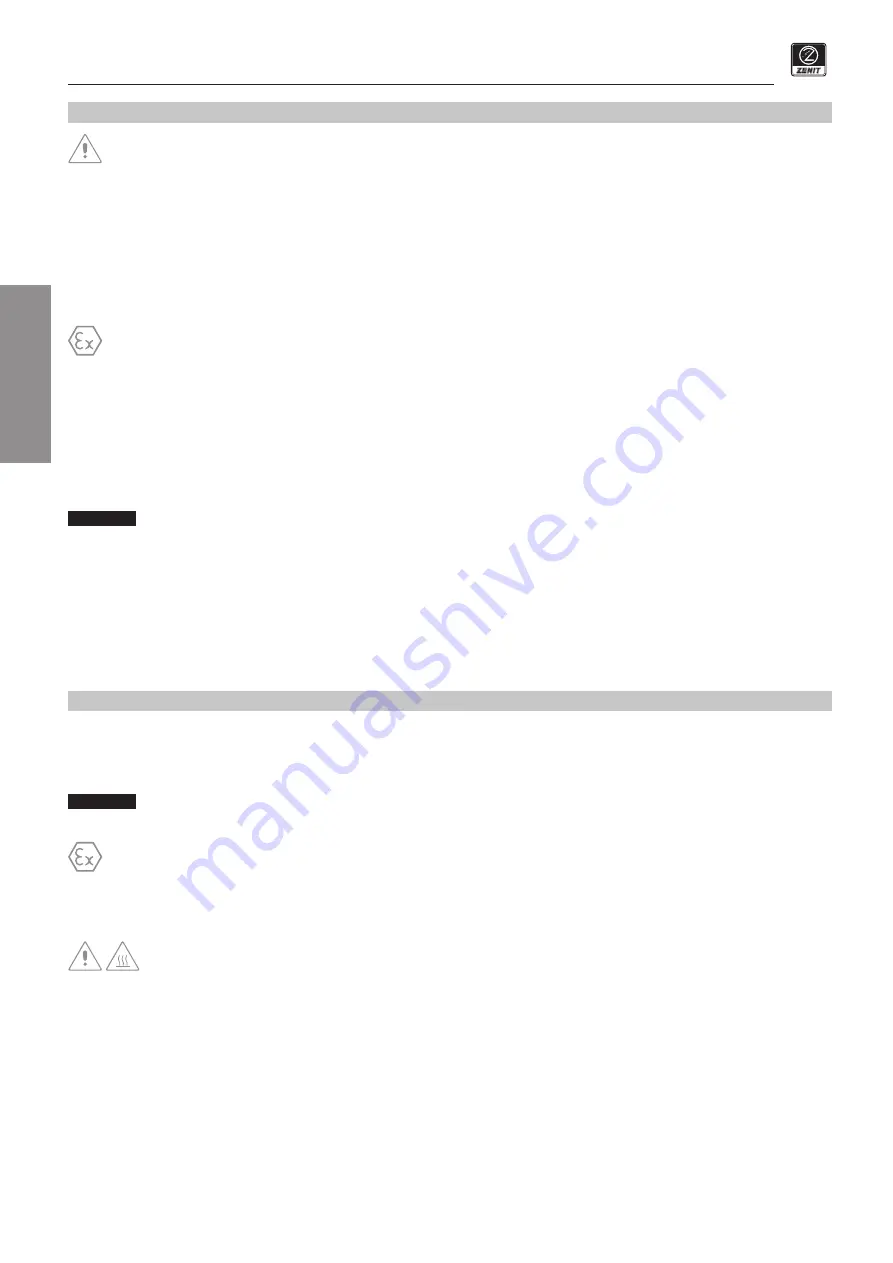
14
water solutions
First installation manual – Translation of original instructions
4. COMMISSIONING
4.1 General safety precautions
•
All operations must be carried out by skilled technical staff.
•
Keep objects and people at a safe distance from the machines installed and do not allow people or animals to come into contact with the liquid
in which they are immersed.
•
Before carrying out any operation, make sure that the pump and electrical panel are disconnected from the electrical mains and cannot be
accidentally powered up.
•
Before connecting the pump to the power supply panel, check that the impeller can turn freely.
•
Check the level and the condition od the oil in oil chamber.
•
Check that the impeller turns in the correct direction using the procedure described in point 3.2 “Checking the impeller rotation direction”.
4.2 Starting the electric pump
The pumps must not be started if the atmosphere in the tank is potentially explosive.
Once installation is complete, the system should be tested to ensure that it is fully operational.
The pump must always be used with the safety devices installed and in good working order; make sure that all protective equipment has been
connected correctly.
The pump must not run dry; check that the liquid level is above the motor.
Check that the required gate valves (where fitted) fuction are open.
Switch on the power supply and let the pump run briefly and:
•
check that the input current is within the limit stated on the nameplate;
•
check whether the monitoring units are operating satisfactorily (no alarms or warnings);
•
check the setting of the level control system (minimum and maximum levels).
warning
!
The maximum permitted number of starts per hour must be complied with to prevent damage to the motor.
In case of abnormal noise or vibration from the pump, other pump failure, alarms or warnings, stop the pump immediately and do not restart it until
the cause of the anomalies are found and fixed.
4.3 Acoustic pressure level
The pump’s acoustic pressure level when in operation is below 70 dB.
However, in some systems and in some duty points on the performance curve this threshold may be exceeded.
Check the permitted acoustic pressure level in the environment where the product is installed to avoid breaching local legal requirements.
5. MAINTENANCE AND SERVICE
5.1 Introduction
Zenit electric submersible pumps undergo through final inspection before they are offered for sale and installed.
The product’s reliability derives from the use of top quality components but also depends on regular inspections which must be carried out by the
user.
warning
!
The instructions for inspection and maintenance of these pumps must never be viewed as “Do-It-Yourself” procedures;
they require specific technical knowledge.
Any interventions of the pump in -Ex versions must be carried out by an authorised Service Centre or by authorised technicians
using only original spare parts. Requests and/or orders of spare parts by unathorised centre will be declined by Zenit.
Failure to comply with this rule may cause loss of warranty rights and put the pump’s safety at risk. A service and planned maintenance contract
with the Zenit Authorised Service Centre guarantees the best technical service. The Zenit warranty is only valid if repairs and reactive maintenance
are performed by an Authorised Service Centre.
5.2 General safety precautions
•
Take the precautions detailed in the “Safety Precautions” manual.
•
Before cleaning and/or maintenance procedures, a skilled technician must disconnect the pump from the power supply and ensure that it
cannot start up accidentally.
•
Always disconnect the phase wires first and then the yellow-green ground wire.
•
Ensure that the pump cannot fall or roll, causing injury or damage.
•
Wash the surface of the pump thoroughly with clean water and/or specific detergent before doing any work on it.
•
After prolonged use, the surface of the pump may become very hot: allow it to cool sufficiently to avoid burns.
•
Always comply with the safety regulations in force in the place of installation, any local regulations and the dictates of common sense.
5.3 Planned maintenance and service
Maintenance intervals depend on the type of installation, the workload to which the pump is subjected and the type of liquid in which it is immersed.
During planned maintenance or in any circumstances when the pump’s performance deteriorates or its vibrations and noise level increase, the
parts subject to wear and tear must be inspected; have this done by an Authorised Service Centre.
EN