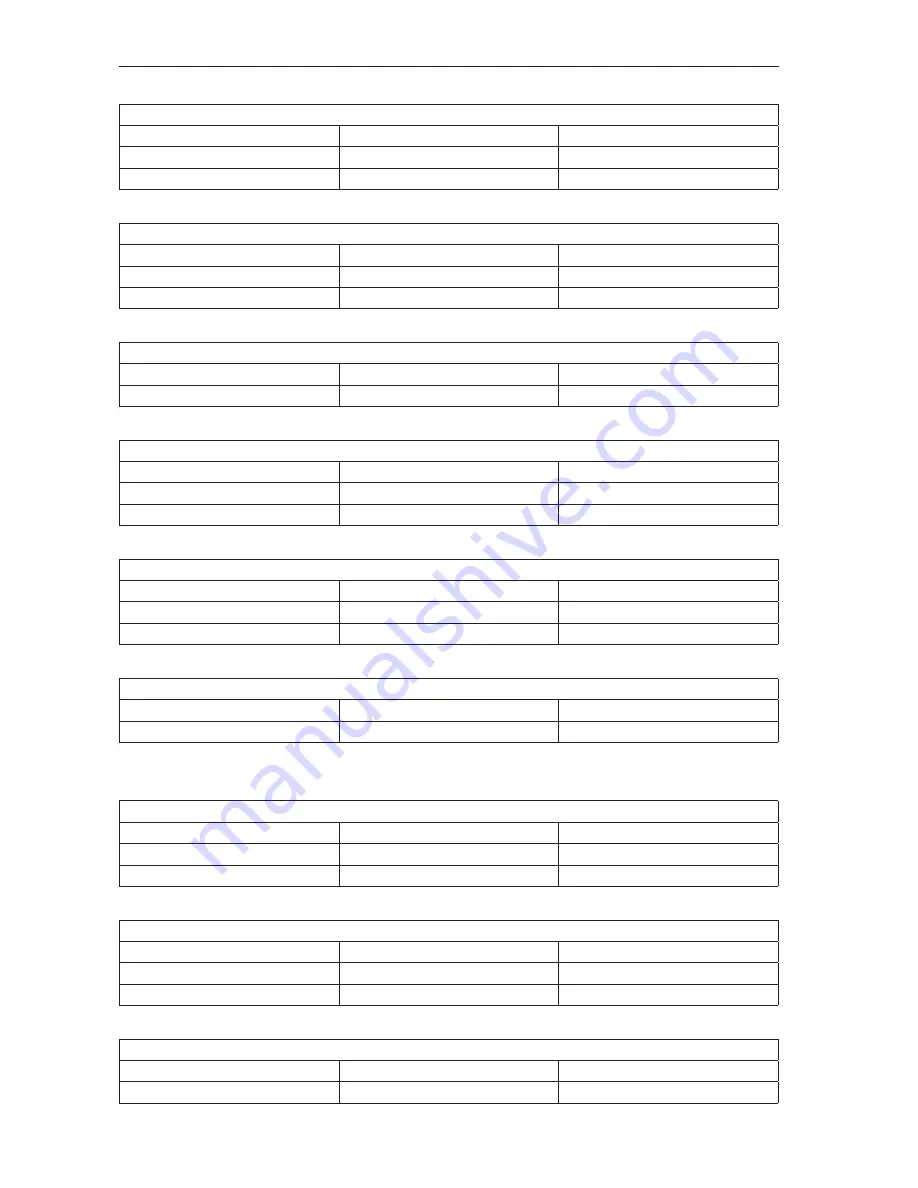
IM00120
126
IM00120
MSC-3 Start Up
Function Code 01: Read Coils
Request:
Function code
1 byte
1
Starting address
2 bytes
0 to 4
Quantity of coils
2 bytes
1 to 5
Response:
Function code
1 byte
1
Byte count
1 byte
1
Coil status
1 byte
MSC-3 coils states
Error:
Function code
1 byte
129 (128+function code, 0x81)
Exception code
1 byte
1, 2 or 3
Function Code 02: Read Discrete Inputs
Request:
Function code
1 byte
2
Starting address
2 bytes
0 to 20
Quantity of coils
2 bytes
1 to 21
Response:
Function code
1 byte
2
Byte count
1 byte
1 to 3
Coil status
1 to 3 bytes
MSC-3 discrete input states
Error:
Function code
1 byte
130 (128+function code, 0x82)
Exception code
1 byte
1, 2 or 3
Function Code 03: Read Holding Registers
Request:
Function code
1 byte
3
Starting address
2 bytes
0 to 9
Quantity of registers
2 bytes
1 to 10
Response:
Function code
1 byte
3
Byte count
1 byte
2 x (Quantity of registers)
Register value(s)
2 x (Quantity of registers) bytes
MSC-3 holding register(s)
Error:
Function code
1 byte
131 (128+function code, 0x83)
Exception code
1 byte
1, 2 or 3
Summary of Contents for MSC-3
Page 1: ...MSC 3 Instruction Manual INVENTIVE TECHNOLOGY DSP II...
Page 3: ......
Page 6: ...IM00120 iv IM00120...
Page 14: ......
Page 59: ...IM00120 45 IM00120 MSC 3 Instruction Manual Extended Features Option Wiring...
Page 60: ......
Page 157: ......