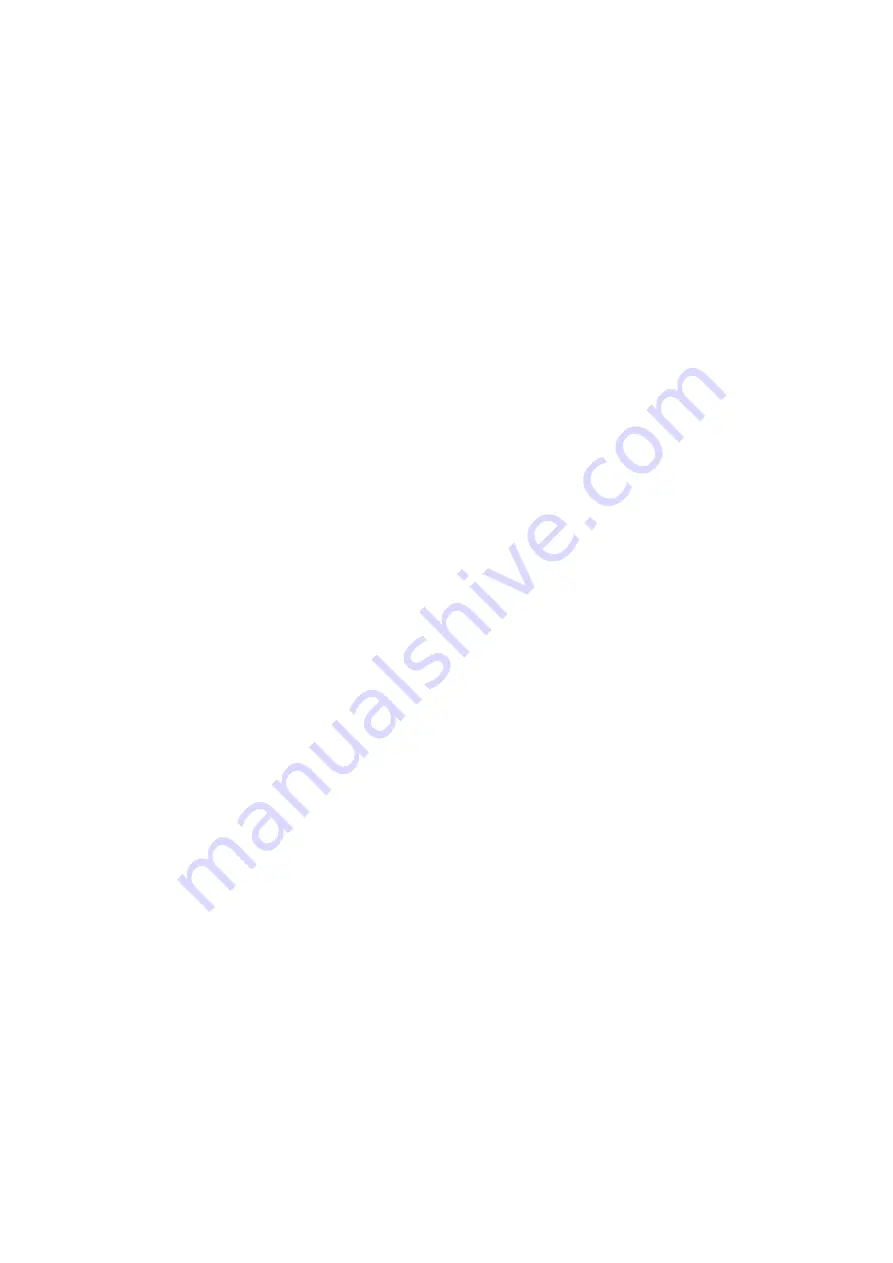
This should be done before gluing to the leading edge to be beveled (see picture) to the glue
gap low to hold.
Then the planking completely glued.
Page 16
10. Glue the rear paneling. In front the bond should be the two balsa strips can be attached.
Thereby becomes the right one rib spacing guaranteed. But do not glue the end strips yet!
Attention, the rear planking has at the top with 21 mm and at the bottom with 22 mm a different
width!
Then the two planking parts between the front and rear paneling fitted and glued.
Page 17
11. Planking for aileron servo adjust and glue. This will on ribs # 12 and # 13 appropriate.
12. Glue the end strip. For the right one alignment of the balsa end strips are included in the balsa
template kit at. For greater stability you can carefully use the templates beforehand low
viscosity superglue soaked will. It is also important to ensure that the right-angled cutting edge
of the both end strips pointing downwards (see image).
13. Top side, except for planking at aileron servo, planked
14. The next step is the wing half from building board taken.
Page 18
15. Setting up the slipway ribs for the machining the bottom. The ribs are now in great shape
millings in the Helling base plate placed and in fixed at right angles to the building board.
There will be a rib in the area rib # 1, one in the area of rib # 9 and one in the area of rib # 17
set up. Subsequently becomes the wing half with the upper one planking down on the slipway
placed. The wing half is like on the images evident, with screws, halved toothpicks and the
4mm beech rods fixed.
Slope Strips
(1 x drawing)
Page 19
16. Rudder fin glue in. The frontal plywood final rib with a distance of approx. 1mm glue to rib
# 9.
17. GRP hooks for surface mounting glue into rib # 1. The GFK got to in front the bonding be
sanded and degreased. The milling edges must be well deburred
18. Now the feet are off the ribs separated and possibly overhangs sanded flush with the contour.