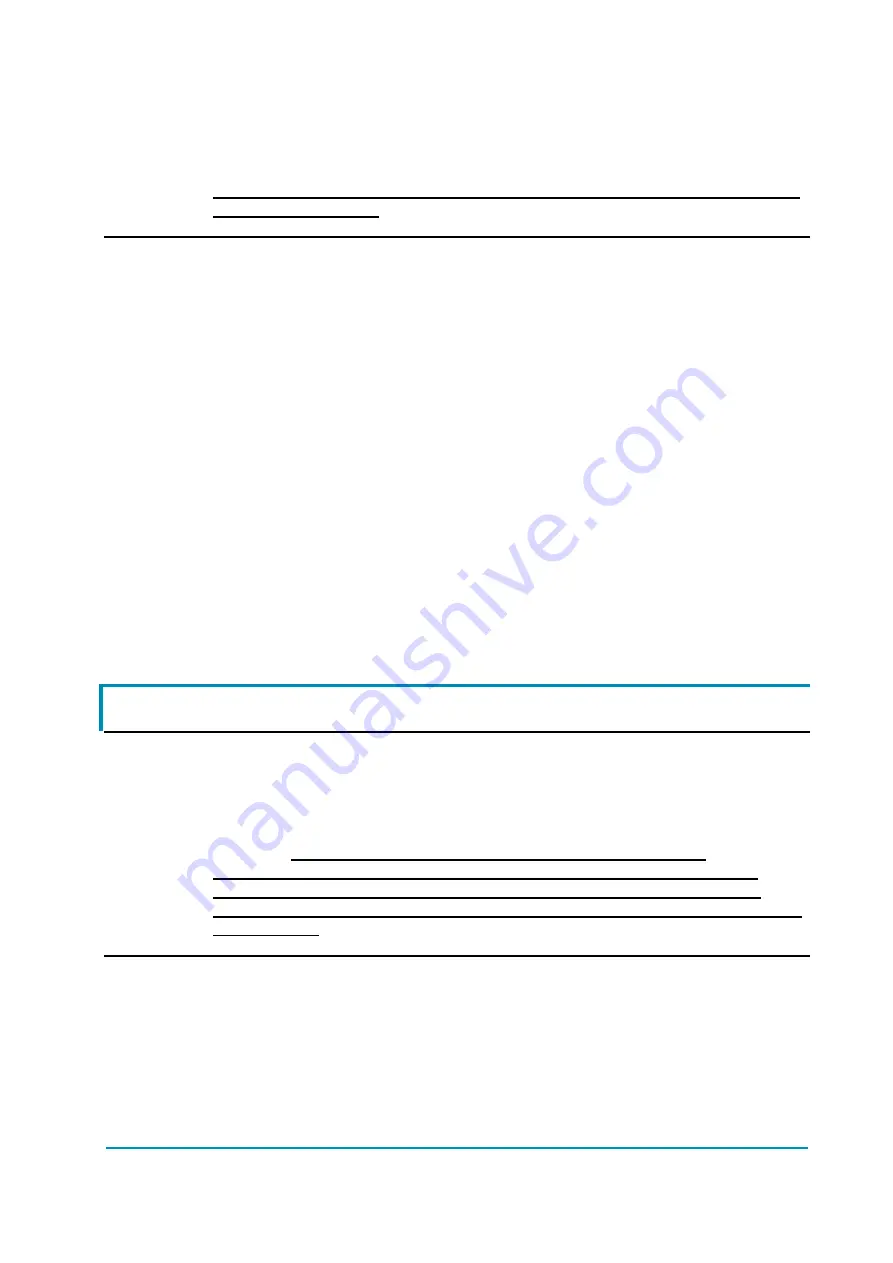
AFDZP0BA – VCM Zapi 2uC - User Manual
Page - 19/54
screening of electrical connections have to be carefully designed.
ZAPI is always available to cooperate with the customer in order to evaluate
installation and connection solutions. Furthermore, ZAPI is available to
develop new SW or HW solutions to improve the safety of the machine,
according to customer requirements.
Machine manufacturer holds the responsibility for the truck safety features
and related approval.
6.3.3 Double microcontroller architecture
The VCM module has two separated microcontrollers in a master/slave
architecture. The communication between them is realized by the local CANbus
line.
Many input and output pins are connected to both master and slave
microcontroller (see chapter 7) . These pins can be used as part of safety
functions whose requested Performance Level is high. The double-
microcontroller architecture operates as follows:
For inputs: both master and slave read the status of the input pin, through
two independent circuits. Then the two microcontrollers use the local CANbus
line to check if the two read status are equal. Any mismatch during the read
process is detected and it can be used to enter an alarm condition or to start
other actions.
For outputs: the master transmits the control command to the output driver
(which can be a current command or a PWM command) while the slave gives
an enable signal which can block the master command. No output can be
turned on unless both microcontrollers has agreed on the activation.
6.4 EMC
U
EMC and ESD performances of an electronic system are strongly
influenced by the installation. Special attention must be given to the
lengths and the paths of the electric connections and the shields. This
situation is beyond ZAPI's control. Zapi can offer assistance and
suggestions, based on its years experience, on EMC related items.
However, ZAPI declines any responsibility for non-compliance,
malfunctions and failures, if correct testing is not made. The machine
manufacturer holds the responsibility to carry out machine validation,
based on existing norms (EN12895 for industrial truck; EN50081-2 for other
applications).
EMC stands for Electromagnetic Compatibility, and it represents the studies and
the tests on the electromagnetic energy generated or received by an electrical
device. So the analysis works in multiple directions:
2) Emission
problems, the disturbances generated by the device and the
possible countermeasure to prevent the propagation of that disturbances. It is
used to talk about “conduction” issues when guiding structures such as wires
and cables are involved, “radiated emissions” when the propagation of
electromagnetic energy happens through the open space. In the CAN I/O