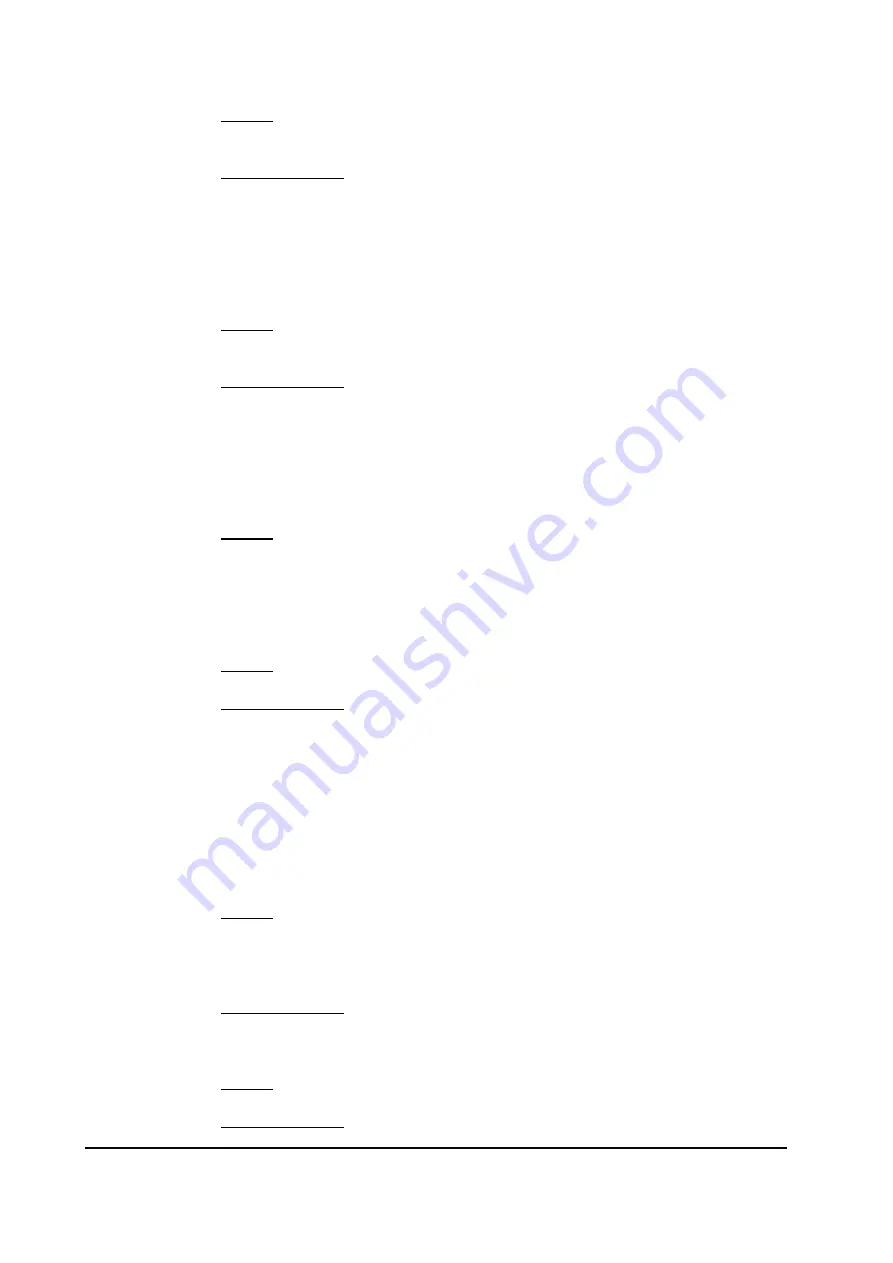
8) “PUMP
I=0
EVER”
Cause:
This test is carried out when the pump motor is running, and it verifies that
the current feedback sensor is not constantly stuck to 0.
Troubleshooting:
A) Check the motor connection, that there is continuity. If the motor
connection is opened, the current cannot flow, so the test fails and the
error code is displayed.
B) If everything is ok for what it concerns the motor, the problem could be in
the current sensor or in the related circuit.
9) “MOTOR
TEMPERATURE”
Cause:
This warning occurs when the temperature sensor is opened (if digital) or has
overtaken the threshold of 150° (if analog).
Troubleshooting:
Check the thermal sensor inside the motor (use the MOTOR
TEMPERATURE reading in the TESTER menu); check the sensor ohmic
value and the sensor wiring. If the sensor is OK, improve the air cooling of
the motor. If the warning is present when the motor is cool, then the problem
is inside the controller.
10) “WAITING FOR TRACTION”
Cause:
The controller receive from the CAN the message that Master controller is in
fault condition; as a consequence the pump controller itself cannot enter an
operative status, but has to WAIT for the Master controller coming out from
the fault condition.
11) “INCORRECT START”
Cause:
This is a warning for an incorrect starting sequence.
Troubleshooting:
The possible reasons for this alarm are (use the readings in the TESTER to
facilitate the troubleshooting):
A) A hydraulic function demand active at key on
B) Deadman sensor active at key on
Check the wirings. Check the microswitches. It could be also an error
sequence made by the operator. A failure in the logic is possible too; so
when all of the above conditions were checked and nothing was found,
replace the controller.
12) “VACC NOT OK”
Cause:
The test is made at key-on and after 20sec that the hydraulic potentiometer
(Lift/Lowering) is back to neutral position. This alarm occurs if the Lift /
Lowering potentiometer reading in the TESTER menu’ is 1,0 V higher than
the minimum value when the Lift/Lower accelerator is released.
Troubleshooting:
Check the mechanical calibration and the functionality of the potentiometer.
13) “RAM WARNING”
Cause:
Checksum of the ram failed.
Troubleshooting:
This fault is not related to external components.
Page - 82/86
AEQZP0BA – COMBI AC1 - User Manual
Summary of Contents for COMBI AC1
Page 29: ...7 DRAWINGS 7 1 Mechanical drawing AEQZP0BA COMBI AC1 User Manual Page 29 86...
Page 30: ...7 2 Connection drawing 7 2 1 AmpSaab version Page 30 86 AEQZP0BA COMBI AC1 User Manual...
Page 31: ...7 2 2 AmpSeal version AEQZP0BA COMBI AC1 User Manual Page 31 86...
Page 37: ...9 3 2 Master AmpSeal version AEQZP0BA COMBI AC1 User Manual Page 37 86...
Page 38: ...9 3 3 Slave AmpSaab version Page 38 86 AEQZP0BA COMBI AC1 User Manual...
Page 39: ...9 3 4 Slave AmpSeal version AEQZP0BA COMBI AC1 User Manual Page 39 86...