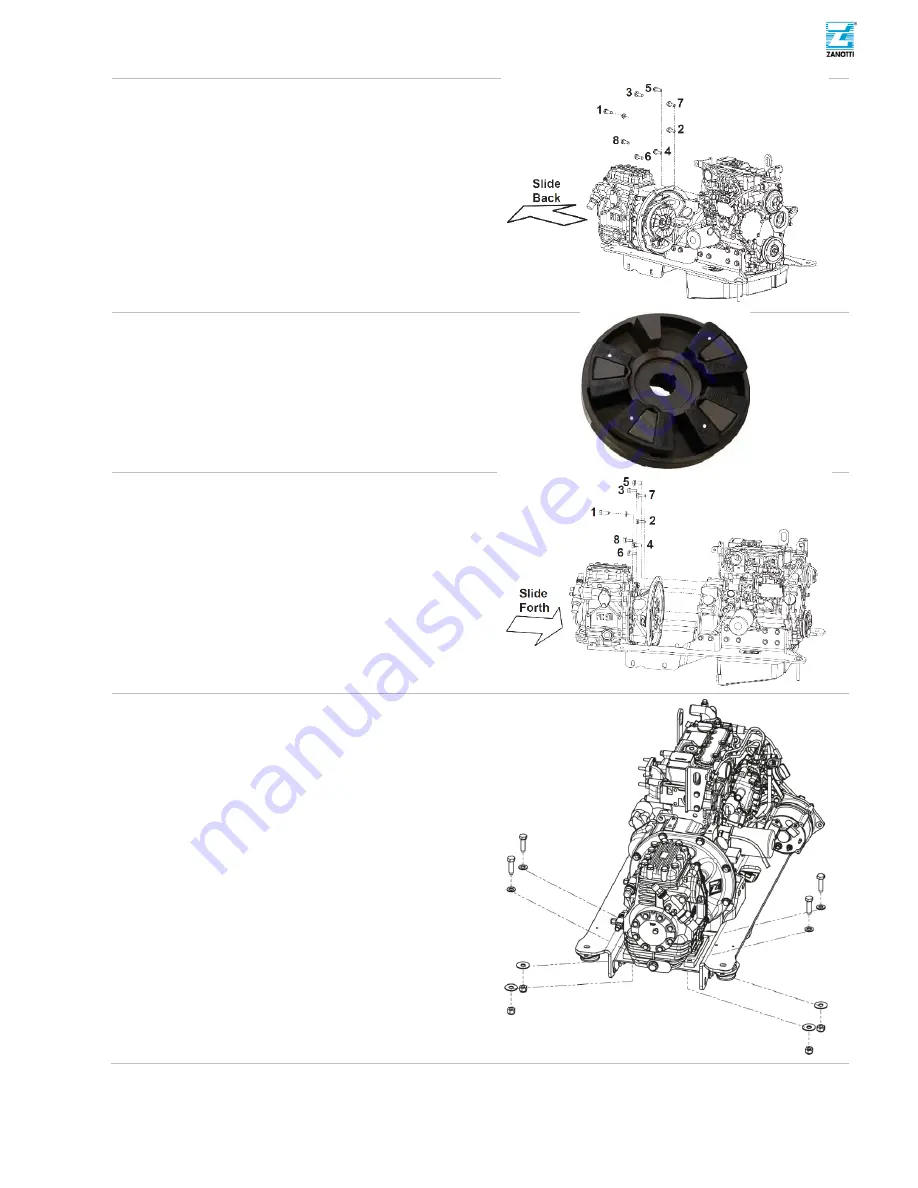
117
4.6 Transmission
Diesel Engine
(h)
Remove bolts from bell- housing (q.ty 8)in a
diametrically opposite sequence.
(i)
Sliding back compressor and bell-housing assembly
from engine flange, just enough to access cou- pling
flexible elements.
(j)
Replace the flexible elements taking care of their
correct positioning.
(k)
Slide compressor forth till bell-housing touch engine
flange.
(l)
Join bell-housing connection to engine flange
screwing in a diametrically opposite sequence
CAUTION
!
Tightening torque: 44N m (389lb − in)
(m)
Fasten compressor to its frame basement.
CAUTION
!
Tightening torque: 74N m (655lb − in).
Summary of Contents for un0 060
Page 1: ...0MAN295 USA WORKSHOPMANUAL un0...
Page 4: ......
Page 15: ......
Page 16: ......
Page 17: ...Section1 Generalinformation...
Page 19: ......
Page 30: ......
Page 31: ...Section2 Descriptionoftheunit...
Page 33: ......
Page 45: ...34 Description of the unit 2 2 Evaporating section...
Page 46: ......
Page 47: ...Section3 CoolingCircuit...
Page 94: ......
Page 95: ...Section4 DieselEngine...
Page 97: ......
Page 130: ......
Page 131: ...Section5 ElectronicsandWirings...
Page 135: ......
Page 146: ...135 5 2 Electronic Boards Electronics and wiring 5 2 Electronic Boards CPU board...
Page 150: ...139 5 2 Electronic Boards Electronics and wiring Relay Board...
Page 155: ...144 Electronics and wiring 5 2 Electronic Boards Low Voltage Wirings...
Page 156: ...145 5 2 Electronic Boards Electronics and wiring High Voltage Wirings...
Page 178: ......
Page 179: ...Section6 Alarms Troubleshooting...
Page 181: ......
Page 183: ...172 Alarms Troubleshooting 6 1 StandardAlarms A04 Low Pressure Switch...
Page 184: ...173 6 1 StandardAlarms Alarms Troubleshooting A07 Water Temperature A08 Door Microswitch...
Page 185: ...174 Alarms Troubleshooting 6 1 StandardAlarms A10 Oil Pressure...
Page 186: ...175 6 1 StandardAlarms Alarms Troubleshooting A11 High Pressure...
Page 188: ...177 6 1 StandardAlarms Alarms Troubleshooting A16 Engine Failure...
Page 189: ...178 Alarms Troubleshooting 6 1 StandardAlarms A17 Alternator Failure...
Page 190: ...179 6 1 StandardAlarms Alarms Troubleshooting A18 Water sensor error...
Page 195: ...184 Alarms Troubleshooting 6 3 Troubleshooting Unit does not start after blackout...
Page 196: ...185 6 3 Troubleshooting Alarms Troubleshooting Unit not performing...
Page 197: ......
Page 198: ......
Page 199: ...Annex1 Parameters...
Page 201: ......
Page 208: ......
Page 209: ......