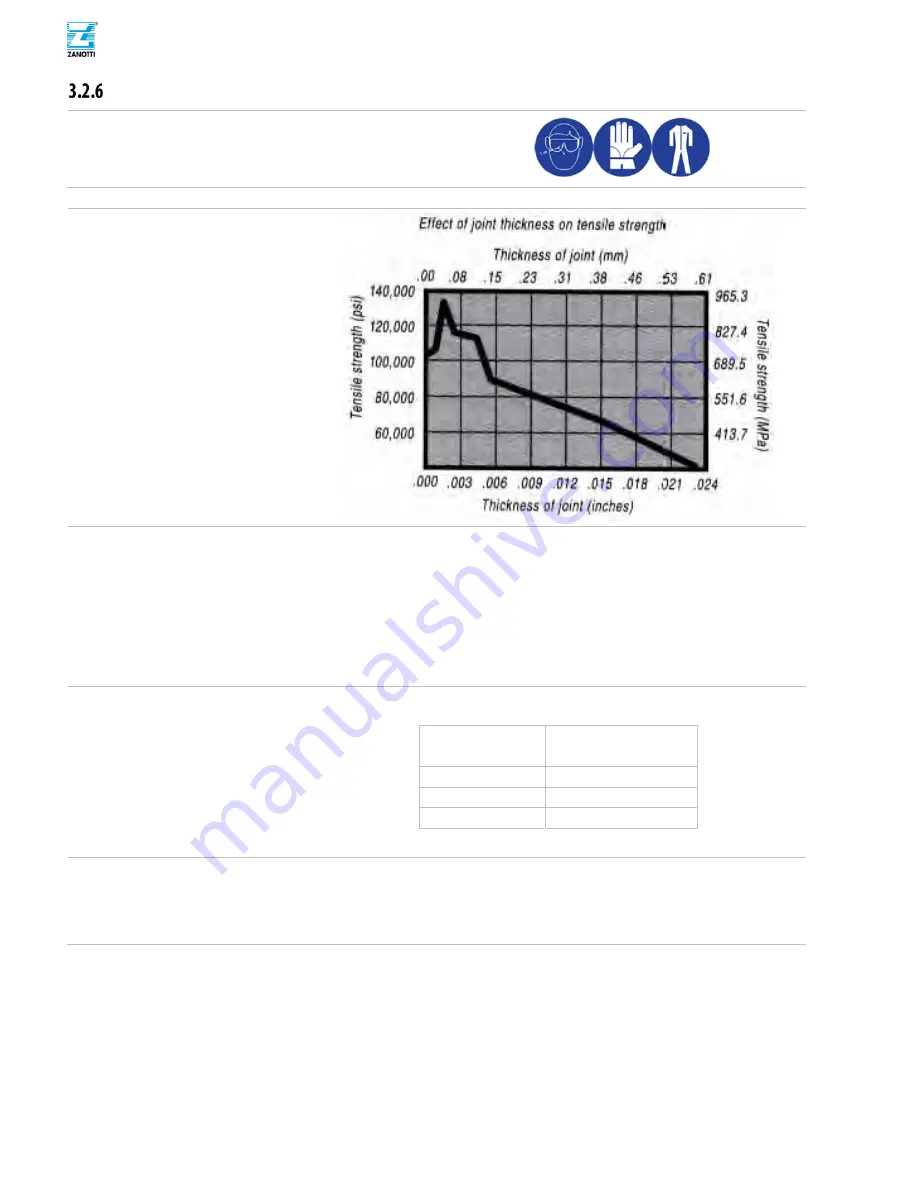
46
Cooling Circuit
3.2 Operations
Basic steps in brazing
Individual Protection Devices
Goggles, Gloves, Vest
(a)
Ensure fit and clearance: Braz-
ing uses the principle of capillary
action to distribute the molten
filler metal between the surfaces
of the base metals. Therefore,
during the brazing operation,
you should take care to maintain
a clearance between the base
metals to allow capillary action
to work most effectively. This
means, in almost all cases, a
close clearance as 0.25mm -
0.13mm (0.001" - 0.005") is
sufficient. When joining
dissimilar metals, allow for
differences in thermal
expansion.
(b)
Clean metal: Joint parts should be well cleaned before welding operations. Brazing filler metal won’t bond to a rusty
surface, furthermore oil and grease will carbonize when heated, forming a film over which filler metal will not stick
compromising junction strength and seal.
(c)
Flux prior to brazing: Flux is required to prevent oxides from forming while the metal is heated. The flux also serves
the purpose of cleaning any contamination left on the brazing surfaces. Flux can be applied in any number of forms
including flux paste, liquid, powder or pre-made brazing pastes that combine flux with filler metal powder. Flux can
also be applied using brazing rods with a coating of flux, or a flux core. Flux must be chemically compatible with both
base metal and filler metal being used.
(d)
Hold parts in position for
brazing, ensuring correct
alignment during heating and
cooling cycles, so that capillary
action can do its job. Best
practice is to flow nitrogen
inside tubes according aside
Table (approx. 0, 35barg),
avoiding internal oxidation dirt.
Tube Diameter
[mm]
Nitrogen Flowrate
[
l/min
]
6
−
18
3
−
4
20
−
40
4
−
5
> 40
5
−
6
(e)
Brazing: Heat a broad area around the joint by hand held torch. Both metal parts in the assembly should be heated as
uniformly as possible so they reach brazing temperature at the same time. Heated assembly will melt off a portion of
the filler metal, which will instantly be drawn by capillary action throughout the entire joint area.
(f)
Clean junction with a metal brush
Summary of Contents for un0 060
Page 1: ...0MAN295 USA WORKSHOPMANUAL un0...
Page 4: ......
Page 15: ......
Page 16: ......
Page 17: ...Section1 Generalinformation...
Page 19: ......
Page 30: ......
Page 31: ...Section2 Descriptionoftheunit...
Page 33: ......
Page 45: ...34 Description of the unit 2 2 Evaporating section...
Page 46: ......
Page 47: ...Section3 CoolingCircuit...
Page 94: ......
Page 95: ...Section4 DieselEngine...
Page 97: ......
Page 130: ......
Page 131: ...Section5 ElectronicsandWirings...
Page 135: ......
Page 146: ...135 5 2 Electronic Boards Electronics and wiring 5 2 Electronic Boards CPU board...
Page 150: ...139 5 2 Electronic Boards Electronics and wiring Relay Board...
Page 155: ...144 Electronics and wiring 5 2 Electronic Boards Low Voltage Wirings...
Page 156: ...145 5 2 Electronic Boards Electronics and wiring High Voltage Wirings...
Page 178: ......
Page 179: ...Section6 Alarms Troubleshooting...
Page 181: ......
Page 183: ...172 Alarms Troubleshooting 6 1 StandardAlarms A04 Low Pressure Switch...
Page 184: ...173 6 1 StandardAlarms Alarms Troubleshooting A07 Water Temperature A08 Door Microswitch...
Page 185: ...174 Alarms Troubleshooting 6 1 StandardAlarms A10 Oil Pressure...
Page 186: ...175 6 1 StandardAlarms Alarms Troubleshooting A11 High Pressure...
Page 188: ...177 6 1 StandardAlarms Alarms Troubleshooting A16 Engine Failure...
Page 189: ...178 Alarms Troubleshooting 6 1 StandardAlarms A17 Alternator Failure...
Page 190: ...179 6 1 StandardAlarms Alarms Troubleshooting A18 Water sensor error...
Page 195: ...184 Alarms Troubleshooting 6 3 Troubleshooting Unit does not start after blackout...
Page 196: ...185 6 3 Troubleshooting Alarms Troubleshooting Unit not performing...
Page 197: ......
Page 198: ......
Page 199: ...Annex1 Parameters...
Page 201: ......
Page 208: ......
Page 209: ......