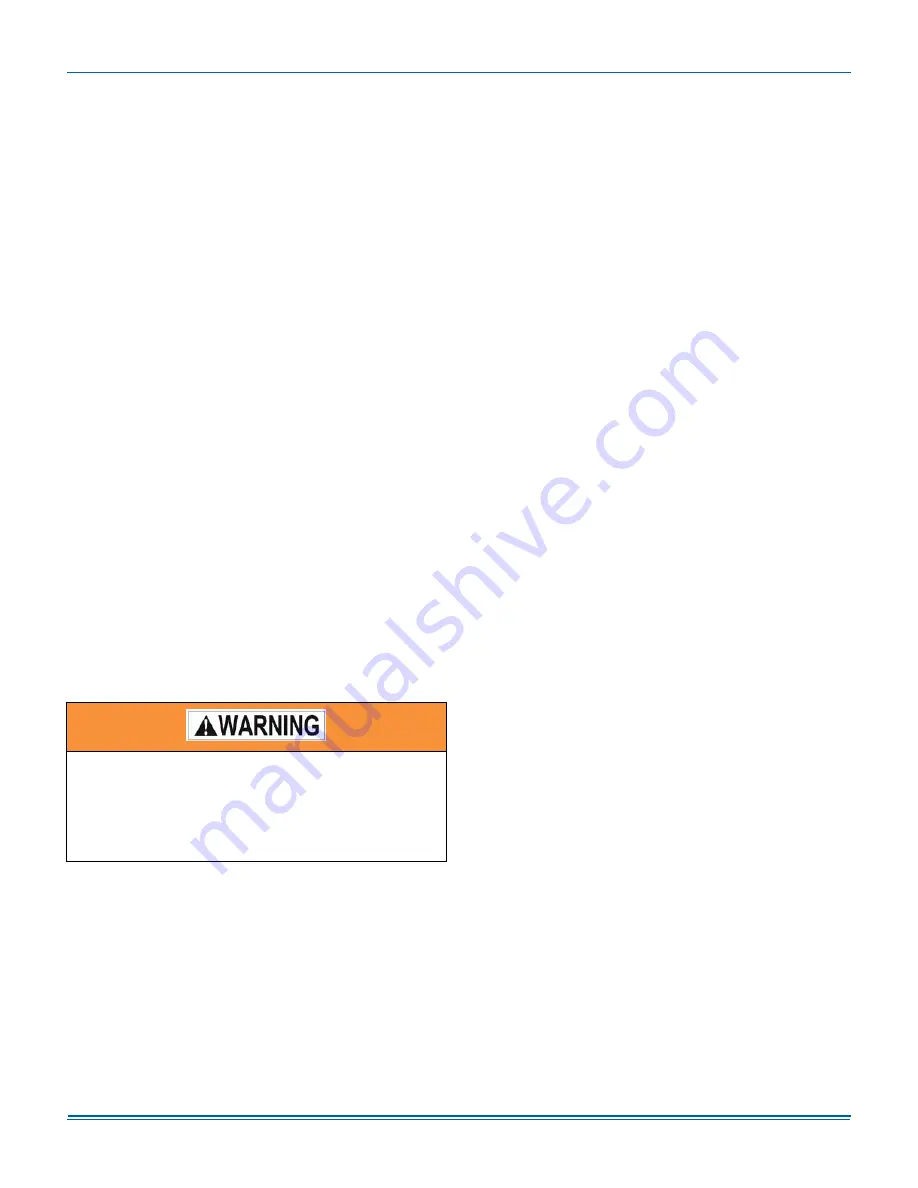
524581-YIM-I-0512
68
Johnson Controls Unitary Products
economizer is not providing free cooling. To test the
economizer control, disconnect the Mate-N-Locks and
jumper between the WHITE and YELLOW wires of the
UCB’s Mate-N-Lock plug.
13. The UCB can be programmed to lock out compressor
operation during free cooling and in low ambient
conditions. These options are not enabled by default. They
can be checked by local distributors.
For units with factory installed economizers, the UCB is
programmed to lock out compressor operation when the
LAS set point is reached.
For units without factory installed or with field installed
economizers, the UCB allows compressor operation all the
time. This programming can be checked or changed by the
local distributor.
14. If none of the above corrected the error, test the integrity of
the UCB. Disconnect the C1 terminal wire and jumper it to
the Y1 terminal. DO NOT jump the Y1 to C1 terminals. If
the compressor engages, the UCB has faulted.
15. If none of the above correct the error, replace the UCB.
Gas Heat Troubleshooting Guide
NOTE:
For units with optional VFD without manual bypass, the
M3 contactor has been replaced with an "ice cube"
relay (designated 'VFDR') located in the control box.
The relay is energized by "FAN" output from the UCB.
Normally-open relay contacts provide a run-permit
signal to the VFD.
On calls for heating, the draft motor operates and the furnace
lights but the supply air blower motor does not energize after a
short delay (the room thermostat fan switch is in “AUTO”
position).
1.
Place the thermostat fan switch in the “ON” position. If the
supply air blower motor energizes, go to Step 9.
2.
If the supply air blower motor does not energize when the
fan switch is set to “ON,” check that line voltage is being
supplied to the contacts of the M3 contactor, and that the
contactor is pulled in. Check for loose wiring between the
contactor and the supply air blower motor.
3.
If M3 is pulled in and voltage is supplied at M3, lightly touch
the supply air blower motor housing. If it is hot, the motor
may be off on inherent protection. Cancel any thermostat
calls and set the fan switch to “AUTO”, wait for the internal
overload to reset. Test again when cool.
4.
If M3 is not pulled in, check for 24 volts at the M3 coil. If 24
volts is present at M3 but M3 is not pulled in, replace the
contactor.
5.
Failing the above, if there is line voltage supplied at M3, M3
is pulled in, and the supply air blower motor still does not
operate, replace the motor.
6.
If 24 volts is not present at M3, check that 24 volts is
present at the supply air blower motor terminal on the UCB.
If 24 volts is present at the UCB terminal, check for loose
wiring between the UCB and M3.
a. If 24 volts is not present at the UCB supply air blower
motor terminal, check for 24 volts from the room
thermostat. If 24 volts is not present from the room
thermostat, check for the following:
• Proper operation of the room thermostat (contact
between R and G with the fan switch in the “ON” position
and in the “AUTO” position during operation calls.)
• Proper wiring between the room thermostat and the
UCB, and
• Loose wiring from the room thermostat to the UCB
7.
If 24 volts is present at the room thermostat but not at the
UCB, check for proper wiring between the thermostat and
the UCB, i.e. that the thermostat G terminal is connected to
the G terminal of the UCB, and for loose wiring.
8.
If the thermostat and UCB are properly wired, replace the
UCB.
9.
If the blower motor runs with the fan switch in the “ON”
position but does not run shortly after the furnace has
ignited when the fan switch is in the “AUTO” position,
check the room thermostat for contact between R and G
during “W1” calls.
On calls for heating, the supply air blower operates but the draft
motor does not (the room thermostat fan switch is in the
“AUTO” position).
1.
The draft motor has inherent protection. If the motor shell is
hot to the touch, wait for the internal overload to reset.
2.
If the motor shell is cold with the room thermostat calling
for heat, check for line voltage at the motor leads. If line
voltage is present, replace the draft motor.
3.
If line voltage is not present, check for line voltage on the
ignition control at the “inducer” terminal draft motor relay
(DMR or DMC) contacts in the main control box and check
to see if the (DMR or DMC) is pulled in.
The draft motor runs but the furnace does not light and the
spark ignitor does not spark.
1.
Check for 24 volts at the spark ignitor from the ignition
control board (ICB). Check the 24-volt wiring from the ICB
to the spark ignitor. Check for 24 volts at the ICB spark
ignitor terminal.
2.
Check the ground wiring for the ICB and the gas valve is
intact and making good electrical connection. Check the
ceramic insulator on the spark ignitor for breaks or cracks.
Replace the spark ignitor if damaged.
The furnace may shut down on a high temperature
condition during the procedure. If this occurs, the UCB
energize the supply air blower motor until the high
temperature limit has reset. Caution should be used at
all times as the supply air blower may energize
regardless of the room thermostat fan switch position.