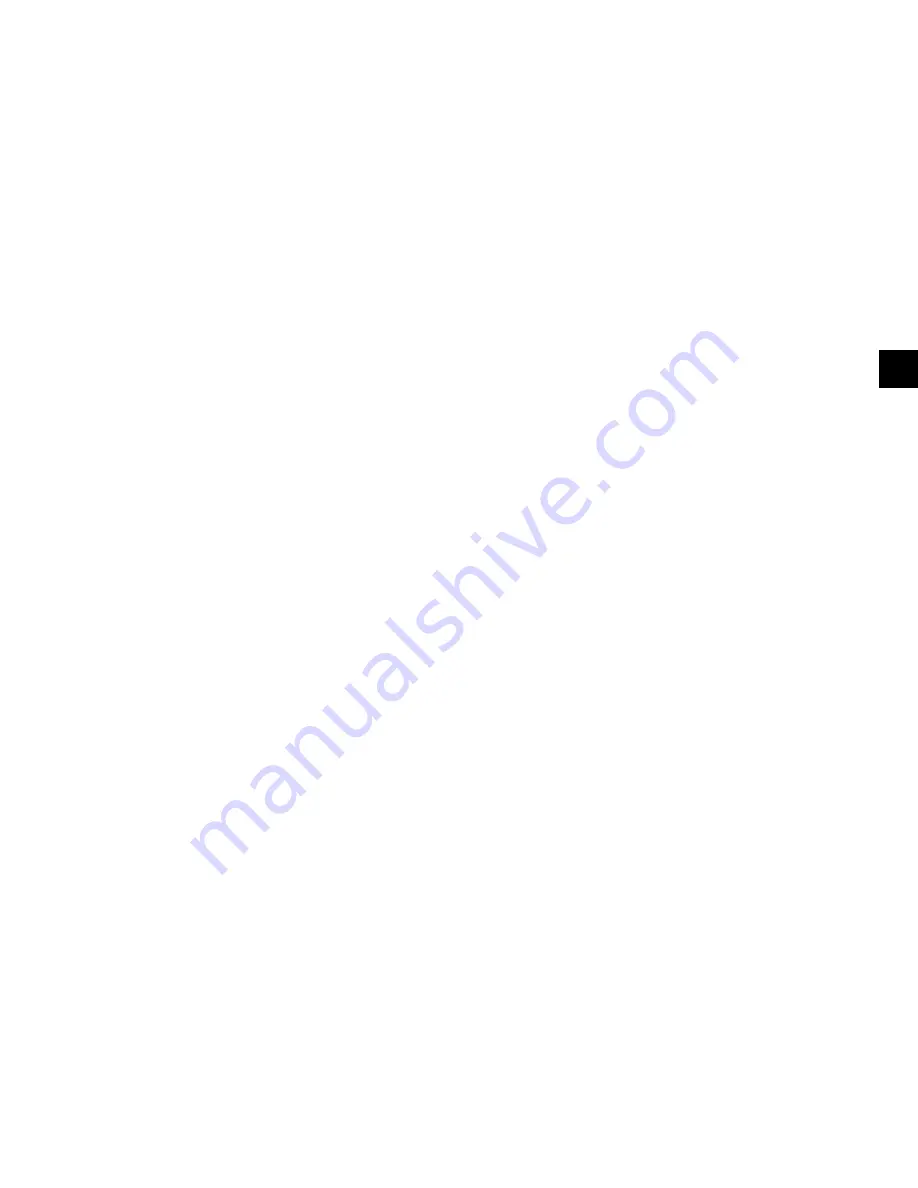
JOHNSON CONTROLS
79
SECTION 6 - MAINTENANCE
FORM 160.67-O2
ISSUE DATE: 10/9/2020
6
These joints have been kept in contact by the bolts
while under prolonged exposure to heat and moisture.
Even though joint compounds have been used at the
factory, which assist sealing and help prevent sticking,
it is to be expected that more or less sticking may oc-
cur from corrosion at one or more of these points.
It
is therefore necessary to proceed with care in order
to avoid damage to the rotor and other stationary
parts.
First, remove sheet metal covering, if provided, insu-
lation and piping as required, then all horizontal joint
bolts. There are four tapped holes in the horizontal
flange. These are provided for the use of jack-bolts in
order to “break” the main casing joint.
Insert bolts and apply reasonable torque to part the
joint. In some cases, it may be necessary to use pene-
trating oil and tap on the casing barrel while jack-bolts
are fully tightened. After the joint separates, continue
to raise the casing cover with the jack-bolts. The rotor
must remain free and bearing caps must not lift as the
cover is raised.
Rotating the shaft while raising the cover will assure
that the rotor is not in contact with any parts being
raised
. If the rotor rises with the cover, it indicates that
either the lower half of a diaphragm or a carbon ring
retaining plate is rising with the cover. This situation
is brought about by diaphragm halves sticking together
in or by retainer plates sticking in the casing cover and
being free in the base. In either case, the cover should
be lifted with the jack-bolts only until all the clearance
(1/6 to 1/8 inch) is taken up and the rotor starts to rise.
Do not lift beyond this point, but retract two diagonally
opposite jack-bolts and rock the cover back and forth.
Try to determine where the sticking is occurring so that
if the rocking does not release the stuck joint, the use
of penetrating oil and tapping on the outside of the cas-
ing will.
Do not use wedges or pry bars between
the joint as this will damage the surface and cause
leakage.
If there is persistent sticking of these parts, consider-
able care must be exercised to free them. Tapping and
rocking as described above should be continued; pos-
sibly tapping directly on the circumference of the dia-
phragm or retainer plate by inserting a flat bar between
the casing flanges (against the diaphragm or plate) and
tapping on the exposed end.
After the parts are free, a chain hoist can be used to
remove cover and rotor. The lower diaphragm portion
cannot rise and the upper portion is fastened to it.
No difficulty should be encountered in lifting the cas-
ing cover. The packing cases employ stainless steel
carbon ring retainer plates. Should the plates stick in
the packing case, screw an eyebolt in the horizontal
flange and impose a lift strain by means of a hand op-
erated chain hoist while tapping on the upper portion
of the packing case near the centerline.
If it is found that any retainer plates are stuck in the
lower portion, these should be freed up with penetrat-
ing oil. After the retainer plates are all free, the ro-
tor, with retainer plates, may be lifted out with a chain
hoist.
The diaphragms are removed by rolling out, assisted
by pulling on a clamp fastened on one corner with a
chain hoist. It may be necessary to free-up the dia-
phragms with penetrating oil before they can be rolled
out.
Before re-assembly, the pressure joints must be com-
pletely cleaned to the bare metal. The joints must then
be re-coated with sealing compound using a type that
will not harden in service. Murray joint compound
is available for this purpose and will not “freeze” the
joints.
The joint compound is also suitable as an anti-seize
compound or pipe thread sealant. The compound must
be kept absolutely clean and free of metal particles that
might interfere with proper sealing.
Apply a light even coat, leaving about ¼ inch of the
joint surface on the inside and outside uncoated to
avoid surplus squeeze-out. Coat only the casing joints
and the packing case joints of bolted type packing
case. Do not apply closer than ¼ inch to carbon rings.
Do not coat diaphragm joints or grooves. Bearing caps
should not be sealed with high temperature joint com-
pound. Instead, use a material intended for oil tight
joints such as “Tite-Seal” or a similar non-hardening
Teflon-based paste compound.
Refer to the Turbine Tightening Torque Specifications
at the end of this section when reassembling the tur-
bine.