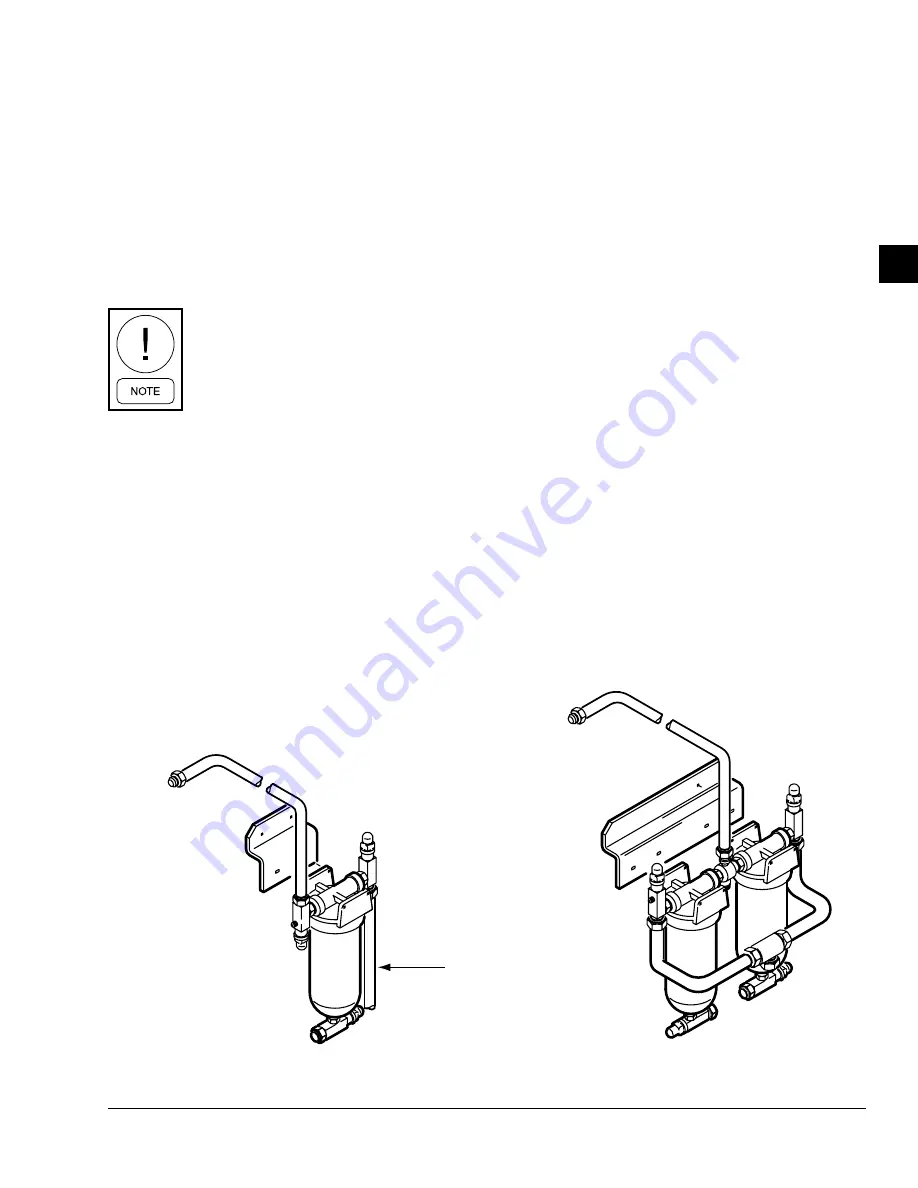
JOHNSON CONTROLS
65
SECTION 4 - OPERATIONAL MAINTENANCE
FORM 160.67-O2
ISSUE DATE: 10/9/2020
4
COMPRESSOR OIL FILTER
A single oil filter is provided as standard equipment
and dual oil filter arrangements are available as option-
al equipment. The oil filter(s) are a replaceable 3 mi-
cron cartridge type oil filter. Use only YORK approved
oil filter elements.
The oil filter element should be changed after the first
200 hours of operation and then as necessary thereaf
-
ter. Always replace the oil filter element and O-ring on
a yearly maintenance schedule.
When the Compressor Oil Pump VSD
frequency increases to 55 Hz to maintain
the target oil pressure, the Compressor Oil
Filter is dirty and needs to be replaced.
Single Oil Filter Replacement
The chiller must be OFF. Place the Keypad control
switch to the OFF position; turn the main disconnect
switch on the power panel to the OFF position to pre-
vent the chiller from being accidentally started.
1. Close the hand isolation valves on the inlet and
outlet oil lines going to and from the oil filter.
2.
Relieve the refrigerant pressure and oil in the oil
filter and the oil lines through the pressure access
port fitting, located on the top of the filter housing.
Connect a refrigeration pressure hose to the pres-
sure access port and drain the oil and refrigerant
into a suitable refrigerant recovery container.
3.
Position a container to collect the oil (less than 2
quarts, 1.9 liters). Loosen and remove the drain
nut at the bottom of the oil filter housing; drain the
oil into the container.
4.
Unscrew the oil filter bowl locking nut.
5. Remove the oil filter element.
6.
Install a new element.
7.
Install a new O-ring on the top of the oil filter
bowl.
8. Tighten the oil filter bowl locking nut.
9.
Open the hand isolation valves.
10. The chiller is ready to be restarted.
FIGURE 16 -
STANDARD SINGLE OIL FILTER AND OPTIONAL DUAL OIL FILTER
LD010025
To Thermostatic
Control Valve
To Compressor
To Compressor