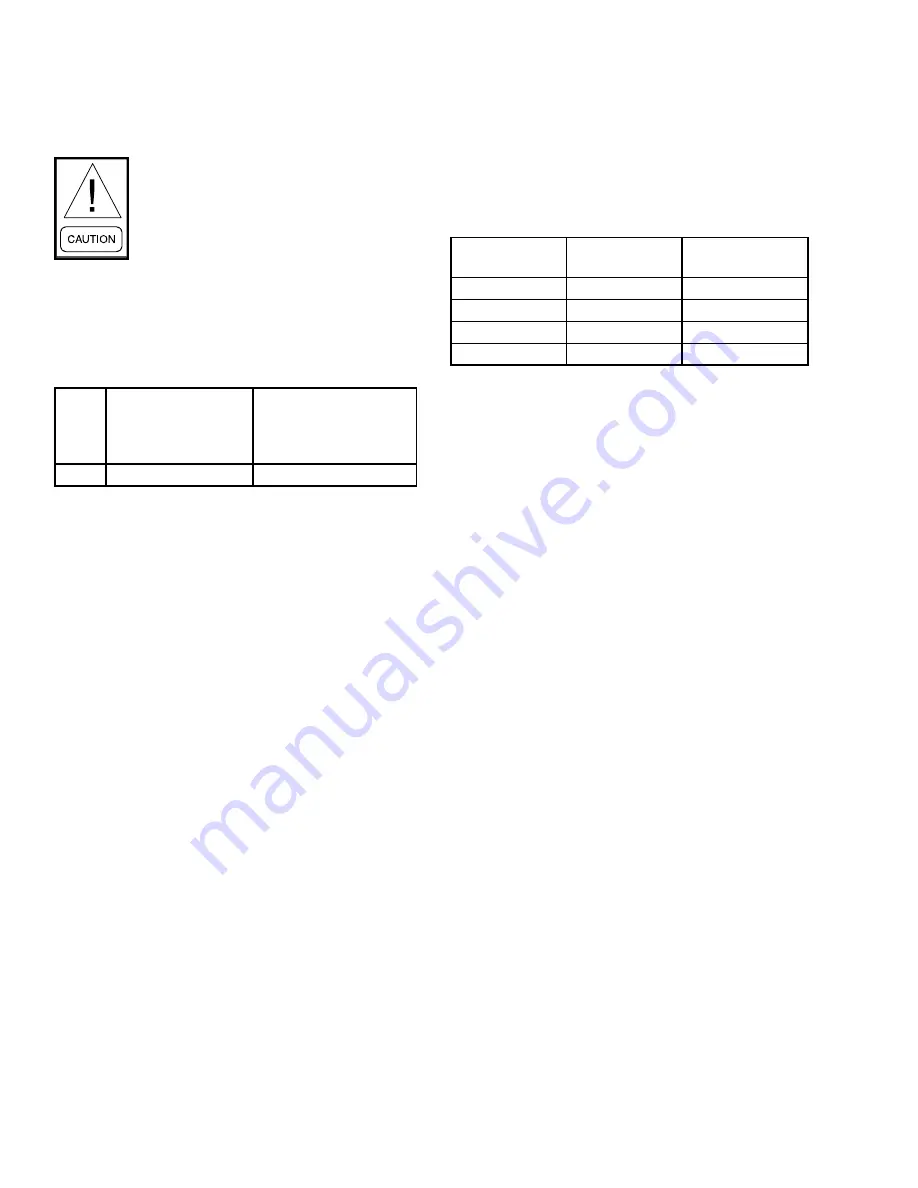
JOHNSON CONTROLS
58
FORM 160.81-NOM1
ISSUE DATE: 10/3/2020
SECTION 5 – MAINTENANCE
COMPRESSOR OIL
Yearly oil analysis is recommended to verify the con-
tinued use of the compressor oil.
It is very important to take the oil sample
after the oil filter. The oil sample should
not be left open to the atmosphere for
more than 15 minutes since it will absorb
moisture from the atmosphere and may
yield erroneous results.
Compressor oil should be changed when the oil analy-
sis indicates the oil has moisture and acid numbers are
in excess of the limits set in
TABLE 15 -
COMPRESSOR OIL LIMITS
YORK
OIL
TYPE
MOISTURE
CONTENT
(BY KARL FISHER)
PPM
TAN
(TOTAL ACID NUMBER)
MGKOH/ML
H
LESS THAN 300 PPM
LESS THAN 0.5
The YORK YR Chiller Compressors use rolling ele-
ment bearings (ball and roller bearings); no sleeve
bearings are used. Oil analysis that include metals may
cause confusion when the results are compared to other
equipment that utilize different bearing types. Iron and
copper are examples of metals, which will appear in oil
analysis that include metals. Other metals that may ap-
pear are Titanium, Zinc, Lead, Tin and Silicon. These
metals should be ignored and are acceptable in quanti-
ties of less than 100 ppm. If an oil analysis should indi-
cate high levels of Iron (more than 300 ppm) combined
with Chromium and Nickel (more than 50 ppm), con-
sult your local Johnson Controls Service Office – this
could indicate bearing damage and wear.
Changing Compressor Oil
Compressor oil is changed by draining oil from the oil
separator into a refrigerant recovery container. The oil
separator is under positive pressure at ambient tem-
peratures. Connect one end of a refrigeration charging
hose to the service valve located at the bottom of the
oil separator; connect the other end to an approved re-
frigerant recovery cylinder. Open the valve and drain
the oil from the oil separator.
CHARGING UNIT WITH OIL
The Oil Charge
YORK oil types approved for YR Chillers and the
quantity of oil required is listed in
TABLE 16 -
YORK OIL TYPE FOR R-134A
COMP. SIZE
OIL TYPE
SYSTEM
QUANTITY (GAL)
T0
H
9
T1
H
9
T2
H
15
T3
H
15
Oil Level
The YR chiller does not have an oil pump. System
oil flow is dependant on the pressure differential be-
tween the condenser and evaporator. Therefore, the oil
flow rate, and oil level in the separator will vary as
the system pressures and slide valve position change.
It is normal for the oil level to be at the bottom of the
lower sight glass or near the top of the upper sight glass
located on the separator, depending on conditions. Oil
should NOT be added unless the oil level cannot be
seen in the lower sight glass. Oil also should NOT be
removed unless the oil level is above the upper sight
glass. The following paragraphs outline procedures to
be followed:
Start-up
1. Oil level cannot be seen in either sight glass on
oil separator:
For chillers shipped with a factory charge of oil
and refrigerant and no oil level is obvious at start-
up, a qualified technician should add only enough
oil to create a visible level in the bottom of the
lower sight glass. Start the chiller and run a load
condition greater than 65% full load amps [FLA]
but less than 80% FLA for a minimum of 1 hour
and observe the oil level. The oil level should
become visible in either the bottom or top sight
glass depending on conditions. A qualified techni-
cian should then remove the approximate amount
added to start the chiller.
2. Oil level above the upper sight glass:
Conditions can exist where the evaporator pres-
sure is higher than the condenser pressure. This
occurs when the evaporator (or chilled) water loop
is warmer than the condenser (or cooling tower)