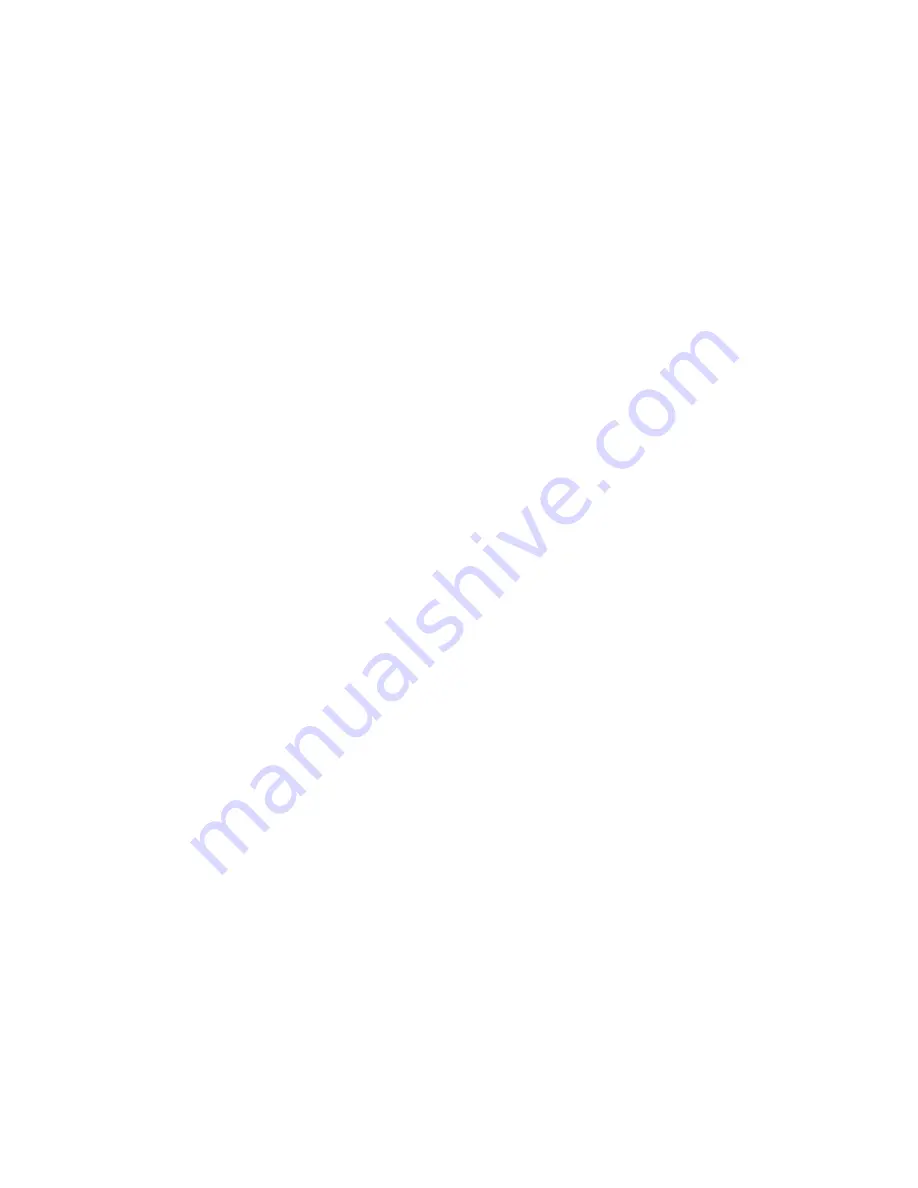
FORM 160.87-OM1
ISSUE DATE: 8/24/2018
JOHNSON CONTROLS
110
SECTION 2 - OPTIVIEW CONTROL CENTER INTRODUCTION
Motor Windings
Temperature
Displays the enabled Motor Winding Temperatures for
phase A, B and C. The setting of the Winding Tempera-
ture Protection Setpoint affects this display as follows:
When winding RTD's are enabled, there are 2 tempera-
tures per phase displayed (otherwise, there is only 1
per phase). When set to Disabled, no temperatures are
displayed and the heading, text and data boxes do not
appear. Individual temperatures can be disabled using
the Temperature Disable Setpoint (on the MOTOR
SETPOINTS Screen). When an individual temperature
is disabled, the temperature data box does not appear.
Any RTD input that registers as an open RTD is con-
sidered invalid and displays as XXX.X.
Average Winding Temperature
This value is calculated as the average of all enabled
and valid Motor Winding Temperatures. Any winding
temperature that registers as open, out of range or dis-
abled is not used in the calculation. When RTD's are
used for winding temperature measurement, there are a
maximum of 6 temperatures used to calculate the aver-
age. When transmitters are used, there are a maximum
of 3 temperatures used to calculate the average. The
text description and data box do not appear when the
Winding Temperature Protection Setpoint is set to dis-
abled.
Motor Cooling Coil Leak Detected (LED)
Illuminates when the enabled Motor Cooling Coil Leak
Detector (refer to
Motor Cooling Coil Leak Protection
) indicates a leak. The LED and text de-
scription do not appear when the Motor Cooling Coil
Leak Protection Setpoint is set to Disabled.
Motor Bearings
Temperature
Displays the enabled Shaft End and Opposite End mo-
tor bearing temperatures. Any RTD input that registers
as an open RTD, is considered invalid and displays as
XXX.X. When the Bearing Temperature Protection
Setpoint is set to Disable, no temperatures are dis-
played and the heading, text and data boxes do not ap-
pear.
Vibration
Displays the Shaft End and Opposite End vibration val-
ues. The vibration values are not in any particular units
of measure. They are relative values. The larger the
number, the greater the magnitude of vibration repre-
sented. When the Motor Vibration Protection Setpoint
is set to Disabled, no vibration values are displayed
and the heading, text and data boxes do not appear.
Vibration Baseline
Displays the Shaft End and Opposite End vibration
values established during the running of the auto base-
line routine using the AUTO BASELINE key or by
manual entry using the MANUAL BASELINE key.
The vibration values are not in any particular units of
measure. They are relative values. The larger the num-
ber, the greater the magnitude of vibration represented.
These values also create the High Vibration Shutdown
and High Vibration Warning thresholds as follows:
(NOTE: if the calculated value exceeds the minimum
and maximum limits of the Shutdown (2.0 to 30.0) or
Warning (1.0 to 15.0) threshold, the threshold is set to
the respective upper or lower limit)
• Shaft End High Vibration Warning - Shaft End Vi-
bration Baseline X2
• Shaft End High Vibration Warning Default - Shaft
End Vibration Baseline X2
• Opposite Shaft End High Vibration Warning - Op-
posite End Vibration Baseline X2
• Opposite Shaft End High Vibration Warning De-
fault - Opposite End Vibration Baseline X2
• Shaft End High Vibration Shutdown - Shaft End
Vibration Baseline X3
• Shaft End High Vibration Shutdown Default -
Shaft End Vibration Baseline X3
• Opposite Shaft End High Vibration Shutdown -
Opposite Shaft End Vibration Baseline X3
• Opposite Shaft End High Vibration Shutdown De-
fault - Opposite Shaft End Vibration Baseline X3
These automatically derived values can be overrid-
den by manually entering a threshold on the MOTOR
SETPOINTS Screen using the VIBRATION SETUP
key.