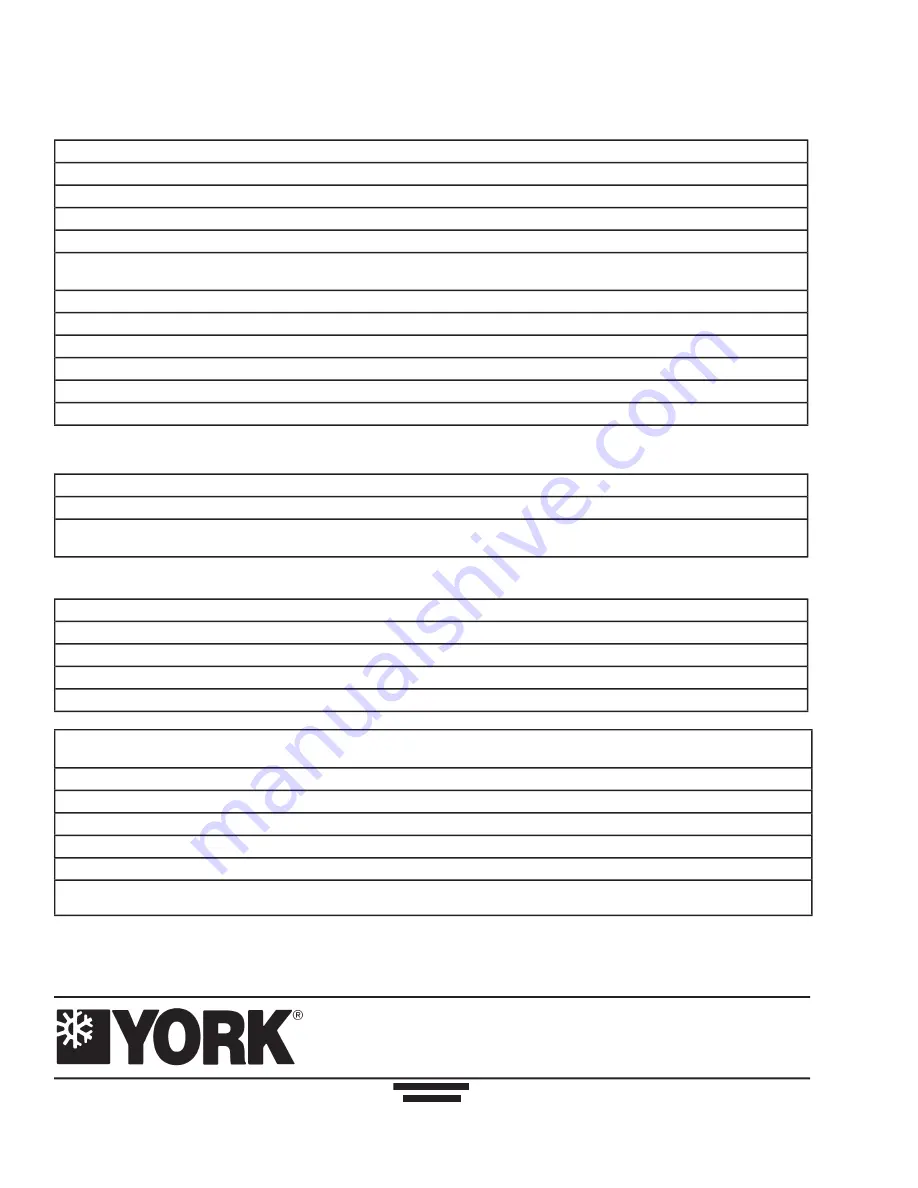
Tele. 800-861-1001
www.York.com
P.O. Box 1592, York, Pennsylvania USA 17405-1592
Subject to change without notice. Printed in USA
Tele. 800-861-1001
Tele. 800-861-1001
Copyright © by Johnson Controls 2006
ALL RIGHTS RESERVED
www.York.com
www.York.com
Form 115.20-NOM6 (1106)
New Release
FAN COILS START-UP CHECKLIST
FAN INSPECTION -
The fan should be inspected and cleaned, in conjunction with main te nance of the motor and bear ings. It is
im por tant to keep the wheel clean in order to avoid im bal ance and vi bra tion.
❑
Check tightness of fan bearing locking collar.
❑
With power off, check blow er wheel set screws for tight ness and ensure that the blower wheel(s) ro tate freely and quietly.
❑
Check tightness of all motor base and mounting bolts.
❑
Check motor connections to en sure that they are se cure and made in accordance with the wiring di a gram
❑
Rotate all moving components manually. Adjust as required.
NOTE: If the motor and fan have not been operated in the last (4) four weeks or more, lubricate all the bearings and rotate the motor and fan
monthly to prevent moisture from accumulating in the bearings. (See Form 50.20-NM3, Long Term Storage)
❑
Installer has cleaned out interior.
❑
Ensure
drain pan free from foreign ma te ri al.
❑
Ensure
air fi lters are clean, installed properly and secured. Use the di rec tion al ar rows or oth er information on the fi lter to
de ter mine the prop er fl ow direction.
INSTALL CHECKLIST
❑
Equipment received as ordered.
❑
Unit checked for damage interior and exterior.
❑
Make sure all ductwork is complete and available for full air fl ow.
❑
Unit installed level to ensure proper drain age and operation.
❑
Unit installed with proper clearances.
❑
Ensure con den sate water will drain to ward the drain con nec tion. An overfl ow drain may be required as a back up to a clogged
primary drain.
❑
Check that coil(s), valves and pip ing have been leak checked and in su lat ed as required.
❑
Main coil drain pan must be properly trapped and charged with water before units are started.
❑
Ensure that all air has been vented from the system.
❑
Return valves to their prop er op er at ing po si tions prior to start-up.
❑
Repair any sol der joint leaks and gently tighten any leak ing valve packing nuts and piping ac ces so ries as required.
❑
Install all panels.
CLEANING CHECKLIST
CONTROLS CHECKLIST
❑
Check that supply voltage matches nameplate data.
❑
Ensure that the unit is prop er ly ground ed.
❑
Controls installation complete
❑
Check all electrical connections for tightness.
❑
Review electrical print for correct wiring.