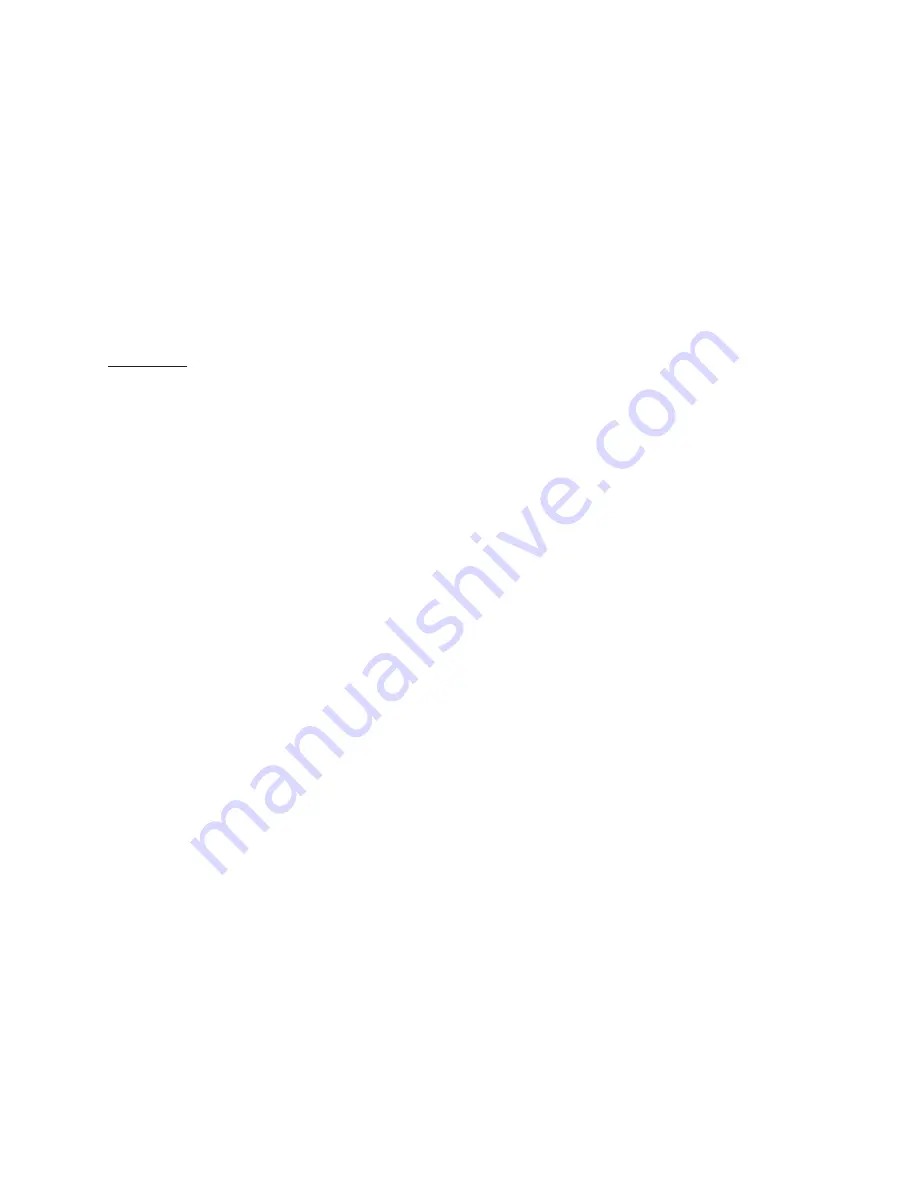
FORM 195.26-NM3
YORK INTERNATIONAL
17
COMPRESSOR INSULATION
In high humidity environments, compressor sweating
may be noted. In most applications, this is of no con-
cern. However, if it is undesirable, it is the responsibil-
ity of the installer to make provisions to field insulate
the compressor or install a factory insulation kit when
they become available. Contact YORK Factory Mar-
keting for availability.
ELECTRICAL WIRING
Chillers are shipped with all factory mounted controls
wired for operation.
Field Wiring – Power wiring must be provided through
a fused disconnect switch to the unit terminals (or op-
tional molded case disconnect switch) in accordance
with N.E.C. or local code requirements. Minimum cir-
cuit ampacity and maximum dual element fuse size
are given on page 10. A 115-1-60/50, 20 amp source
must be supplied for the control panel through a fused
disconnect when a control panel transformer (optional)
is not provided. Refer to Wiring Diagram, Form 195.26-
W2.
Affiliated apparatus, such as a chilled water flow switch,
auxiliary contacts from the chilled water pump starter,
alarms, etc., should be interlocked into the control panel
circuit. These field modifications may be made as shown
on the WIRING DIAGRAM.
FIELD CONTROL WIRING
Affiliated components, such as liquid line solenoid
valves, zone thermostat, start/stop, auxillary cycling
contacts, alarms, and emergency stop, should be in-
terlocked into the control panel circuit. These devices
should be connected as noted below. Also see WIR-
ING DIAGRAMS.
Liquid Line Solenoid Valve Connection
Z Compressors
Connect SYS 1 to terminals 23 and 2 in Compressor
#1 Motor Terminal Box and SYS 2 to terminals 23 and
2 in Compressor #2 Motor Terminal Box. The control
panel will supply a 115 VAC signal to operate each
solenoid. An RC SUPPRESSOR is connected across
terminals 23 and 2 in each Motor Terminal Box. THE
RC SUPPRESSOR MUST NEVER BE REMOVED. See
Fig. 7 for terminal locations.
Liquid Line Solenoid Valve Connection
J Compressors
Connect SYS 1 to terminals SP1 and 2 in Compressor
#1 Motor Terminal Box and SYS 2 to terminals SP1 and
2 in Compressor #2 Motor Terminal Box. The control
panel will supply a 115 VAC signal to operate each sole-
noid. An RC SUPPRESSOR is connected across termi-
nals 23 and 2 in each Motor Terminal Box. THE RC SUP-
PRESSOR MUST NEVER BE REMOVED. See Fig. 7
for terminal locations.
Zone Thermostat Start/Stop
Connect SYS 1 to terminals 13 and 14 of TB3 (Fig. 12).
Connect SYS 2 to terminals 13 and 15 of TB3 (Fig. 12).
User supplied contacts must be dry contacts which
close to run. See Note 4 of the Wiring Diagram for
wiring requirements.
Auxillary Cycling Contacts
Connect SYS 1 in series with SYS 1 Zone Thermostat
on terminals 13 and 14 of TB3 (Fig. 12). Connect SYS
2 in series with SYS 2 Zone Thermostat on terminals
13 and 14 of TB3 (Fig. 12). User supplied contacts
must be dry contacts which close to run. See Notes 3
and 4 of the WIRING DIAGRAM for wiring requirements.
CAUTION:
The fan(s) in the Air Handler MUST be in-
terlocked into the Auxiliary Cycling Contacts.
Failure to do so may cause damage to the
chiller. Do not operate a system unless the
fans are running.
Emergency Stop
Connect between terminals 5 and 1 of TB1 (Fig. 10)
terminal block. Must be N.C. dry contact supplied by
user. Jumper if not used. See Note 5 of WIRING DIA-
GRAM.
Alarm Contacts
A single set of contacts are available on terminals 23
and 24 of TB1 (Fig. 10). These contacts will transition
anytime a fault lockout occurs on either system. Con-
tacts are N.C. under no-fault conditions. Any inductive
loads connected to these contacts must be suppressed.
MULTIPLE UNITS
For increased compressor protection and to reduce
power inrush at start-up on multiple chiller installa-
tions, provisions must be made to prevent simultaneous
start-up of two or more units. Also, some method must
be employed to automatically cycle one or more of the
units on or off to permit more efficient operation at part
load conditions.