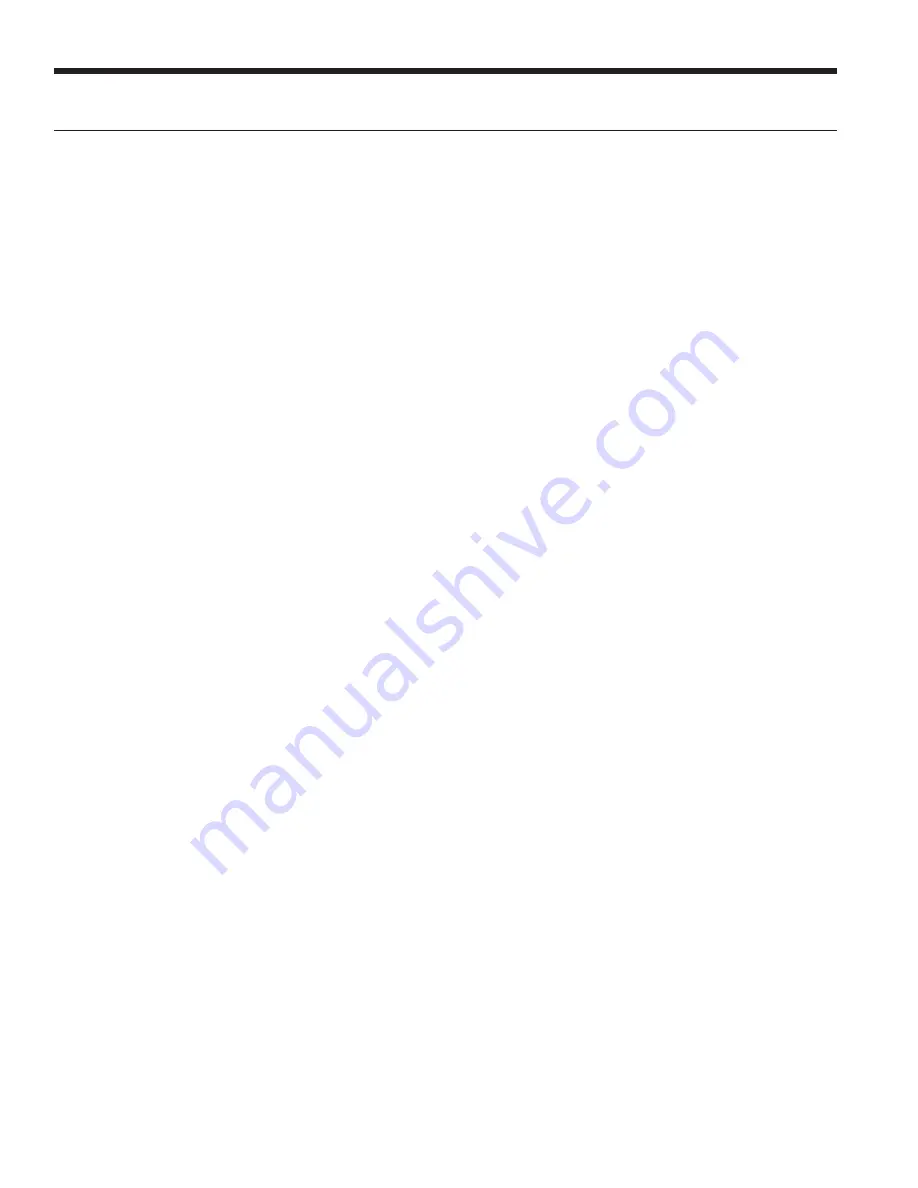
40
Unit Startup
Before Powering Unit, Check the Following:
NOTE:
Remove and discard the compressor hold down
shipping bolt located at the front of the compressor
mounting bracket.
• Black/white and gray/white wires in unit control box
have been removed if auxiliary heat has been installed.
• Dip switches are set correctly.
• Transformer switched to 208V if applicable.
• High voltage is correct and matches nameplate.
• Fuses, breakers and wire size correct.
• Low voltage wiring complete.
• Piping completed and water system cleaned and flushed.
• Air is purged from closed loop system.
• Isolation valves are open.
• Condensate line trapped, open and correctly pitched.
• Blower rotates freely.
• Blower speed is correct.
• Field-installed air filter/cleaner is clean and in position.
• Service/access panels are in place.
• Return air temperature is between 50-80°F heating and
60-95°F cooling.
• Check air coil cleanliness to ensure optimum
performance. Clean as needed according to
maintenance guidelines. To obtain maximum
performance the air coil should be cleaned before
startup. A 10% solution of dishwasher detergent and
water is recommended for both sides of coil, a thorough
water rinse should follow.
Powering The Controls
Initial Configuration of the Unit
Before operating the unit, apply power and complete
the following Aurora Startup procedure for the controls
configuration. An AID Tool is recommended for setup,
configuration and troubleshooting, especially with an
Aurora ‘Advanced’ Control. AID Tool version 2.04 or greater
is preferred.
1. Configure Aurora Screen
a. In advanced controls - Confirm AXB is added
and
communicating.
b. If used confirm communicating
thermostats are added and communicating. Set
thermostat mode to off.
c. In advanced controls - Confirm IntelliZone2, if
installed, is added and communicating. Set Zoning
system to off mode.
2. Aurora Setup Screen
a. ECM Setup for Heating Airflow – select “G”, low,
high and aux blower speeds as appropriate for the
unit and electric heat.
b. Cooling Airflow % - sets the cooling airflow % from
heating airflow. Factory setting is -15%.
c. Sensor Kit Setup
i. Brine Selection – for HE/HR
capacity
calculation
ii. Flow Meter – activates the flow meter
iii. Select blower energy – ECM
iv.
Activate
energy
option
v. Fan and Aux heat current
sensor
activation
vi. Line Voltage calibration – Voltmeter
required to calibrate line voltage during
heating or cooling. Refer to Line Voltage
Calibration in this manual for more details.
d. Smart Grid Setup – Select Action option for utility
received
on-peak
signal
e. Home Automation 1 & 2 Setup – Select type of
sensor for two home automation inputs.
Configuring the Sensor Kits
Configuring the Sensor kits
The Aurora Advanced Control allows Refrigeration, Energy,
and Performance Monitoring sensor kits. These kits can be
factory or field installed. The following description is for
field activation of a factory installation of the sensor kits.
Energy Monitoring (Standard Sensor Kit on
‘Advanced’ models)
The Energy Monitoring Kit includes two current transducers
(fan and electric heat) added to the existing two
compressor sensors so that the complete power usage of
the heat pump can be measured. The AID Tool provides
configuration detail for the type of blower motor, a line
voltage calibration procedure to improve the accuracy, and
a power adjustment setting that allows the compressor
power to be adjusted to match the unit’s line voltage using
the provided tables. This information can be displayed
on the AID Tool, selected communicating thermostats, or
Symphony (if available). The TPCM32U03*/04* will display
instantaneous energy use while the color touchscreen
TPCC32U01* will in addition display a 13 month history
in graph form. Ensure the Energy Kit has been enabled
by accessing the ‘Sensor Kit Setup” in the AID Tool and
complete the following:
a. Select ‘Blower Energy’ – ECM/5-Speed ECM
b. Activate ‘Energy Option’ to activate the sensors on
for compressor (2), fan and aux heat current sensor.
c. Select ‘Pump’ option of FC1, FC2, or open loop.
This selects the pump watts used in the
calculation. Pump watts are not measured
but
estimated.
d. Line Voltage Calibration – Voltmeter required to
calibrate line voltage during heating or cooling.
Refer to Line Voltage Calibration in this manual for
more
details.
i. Turn on Unit in Heating or Cooling .
ii. Use multimeter at L1 and L2 to measure
line
voltage
AFFINITY SERIES
OUTDOOR PACKAGED HEAT PUMP INSTALLATION MANUAL