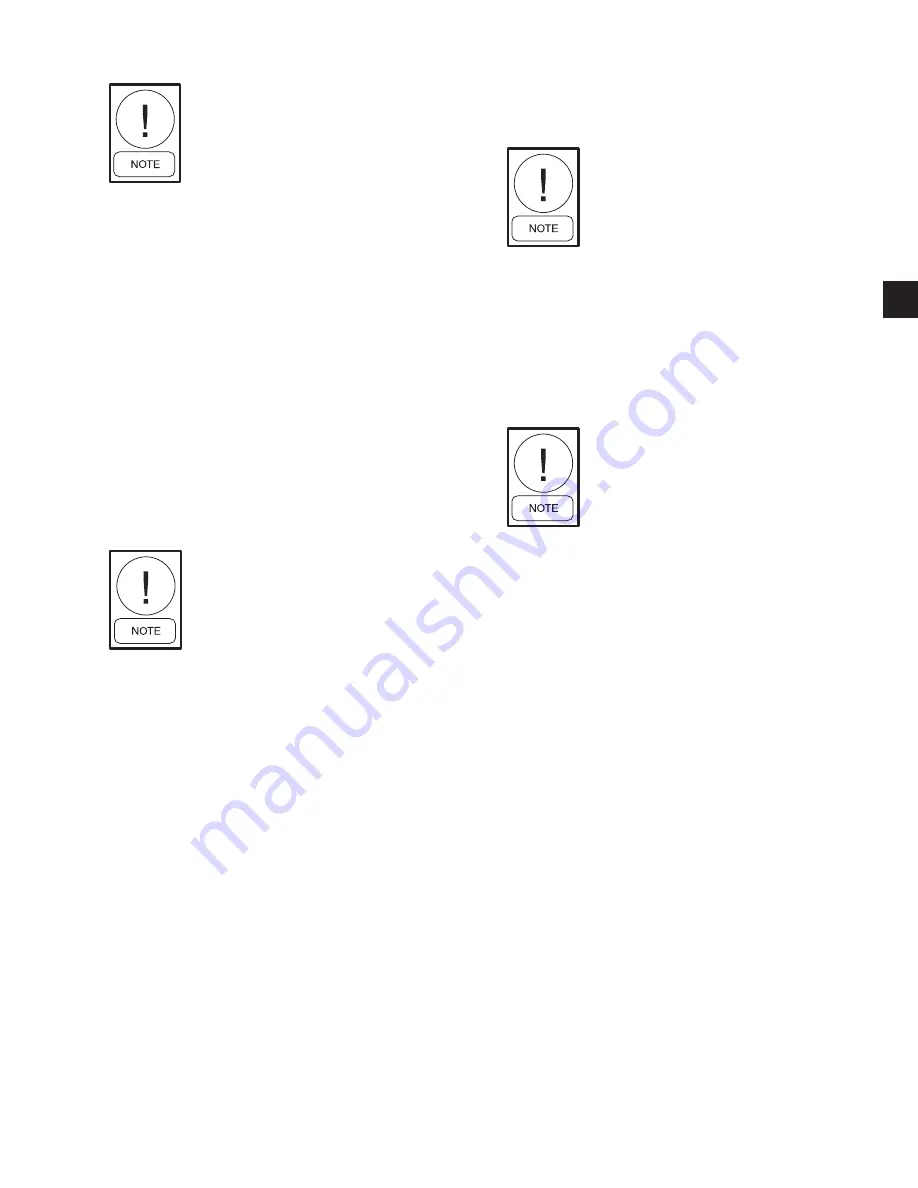
FORM 220.11-NM2 (602)
63
YORK INTERNATIONAL
After completion of each torquing pro-
cedure check to be sure the compres-
sor still fully rotates freely without
drag.
COMPLETION OF COMPRESSOR ASSEMBLY
1. Install the oil pump assembly. (See Replacing Oil
Pump Assembly.)
2. Remove the drive shaft and carefully coat the
threads with YORK Drive Thread Compound P/N
464-14934 before you install the shaft seal. (See
Installing New Shaft Seal.)
3. Complete all internal wiring if proximity probes RTDs
or TCs are used. Be sure to deal with proper sealing
of the connectors per instructions on the drawing or
wrap with teflon tape and seal with heat shrink tub-
ing. Install internal clamps, etc.
4. Install the sump cover and all external oil tubing,
pipe and electrical connections.
Be sure all piping and connections
are thoroughly cleaned prior to assem-
bly.
5. Close all lube oil drains and charge with oil and a
new filter.
6. Energize the oil heaters and circulate oil for 15 min-
utes. Look for leaks. Verify auxiliary oil pump pres-
sure.
PREPARATION FOR TEST RUN
1. Set dial indicators on the compressor shaft to read
horizontal and vertical deflection as the suction and
discharge flange connections are tightened. Maxi-
mum allowable deflection is +/- .002" total com-
bined. Be sure to install correct flange gaskets.
Operation without a guard is not rec-
ommended. Cordon off area if ma-
chine is operated without the guard.
Close supervision is required with un-
protected shafting.
2. Install the drive coupling. See YORK coupling in-
struction for details.
3. Perform leak and vacuum tests in accordance with
YORK instructions. Blow down leak test through
casing drains if possible.
4. Check the motor and gear lubrication.
Presence of some oil vapor or smoke
from the seal area is normal at initial
compressor start. If it persists for more
than a few seconds or gets very severe
shut down the unit.
5. Perform “bump-in” procedures. (See Initial Start-
ing – Mechanical Run-In.)
6. Count the oil drops from the seal and compare for
the compressor size and speed. Seals with a slightly
elevated rate may improve with operational time.
7. Perform hot check for validation alignment.
ORDERING REPLACEMENT PARTS
To order replacement parts refer to the job drawing’s for
all parts including the oil piping. Order parts by their
part numbers. Always show the model and the serial
numbers of the compressor, and the YORK order num-
ber on which the original equipment was furnished.
To obtain parts, contact the nearest YORK Service
office.
4
Summary of Contents for Turbomaster M Series
Page 15: ...FORM 220 11 NM2 602 15 YORK INTERNATIONAL FIG 3 TYPICAL PRIMARY COMPRESSOR GAS FLOW LD07318 3 ...
Page 16: ...YORK INTERNATIONAL 16 FORM 220 11 NM2 602 FIG 4A MAJOR COMPONENTS LD07319 Operation ...
Page 31: ...FORM 220 11 NM2 602 31 YORK INTERNATIONAL Operation 3 This page intentionally left blank ...