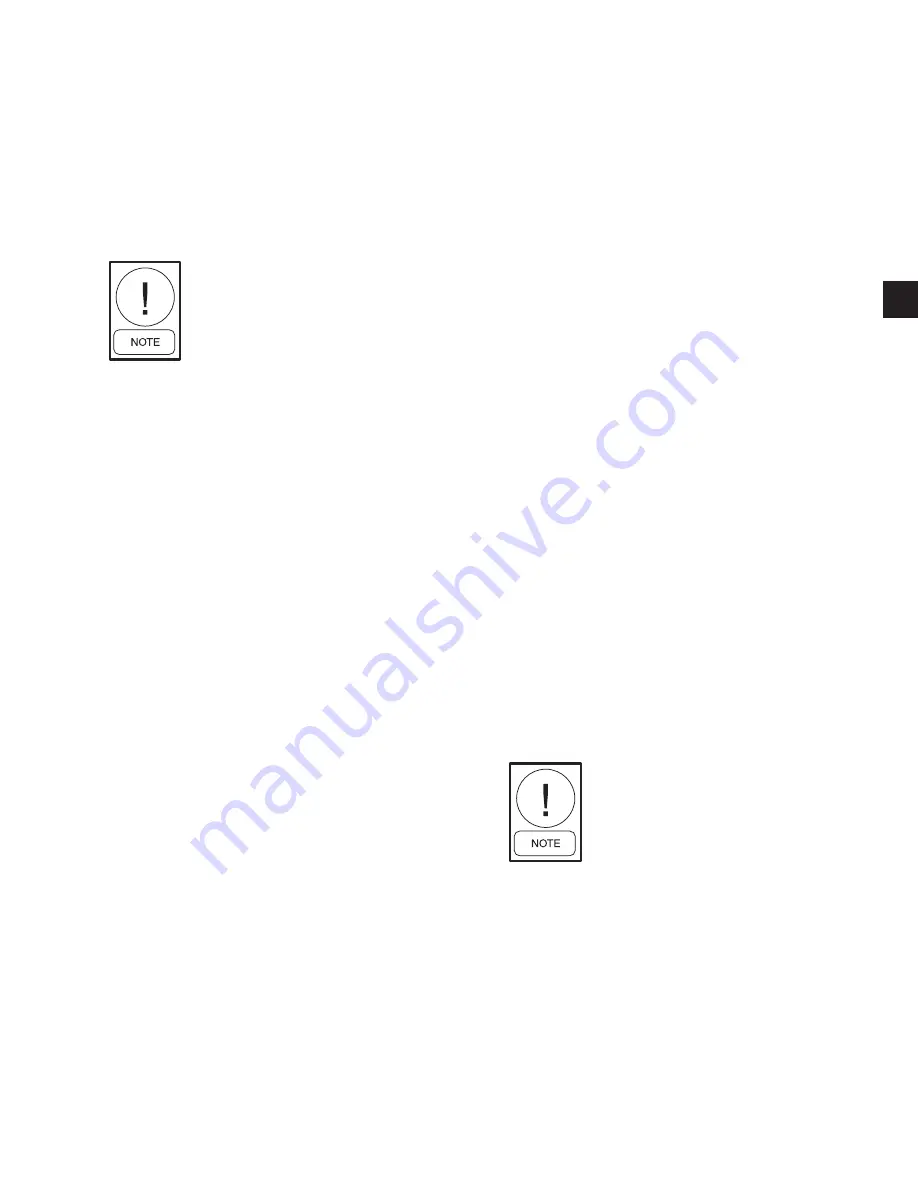
FORM 220.11-NM2 (602)
55
YORK INTERNATIONAL
3. Replace the control shaft by reversing the two steps
above. Use Molycote and oil between the thrust
washer, control shaft, and PRV housing. When in-
stalling fulcrum screw (232), carefully put a drop
of Loctite thread locker (Loctite 277) on the threads.
Do not get Loctite on the bearing rod ball joint.
Replacing Control Shaft Cover
For the old style shaft with vulcanized
rubber bonded bushing, set vanes to
50% open prior to torquing cover
screws.
1. Install new O-rings, (refer to compressor drawing)
on the control shaft and place a new gasket in the
PRV housing recess. Lubricate the control shaft
and O-rings with Molypaste. Seat the shaft cover
and torque the cover cap screws.
2. Verify that all shaft cover markings are in the same
locations and that control shaft and vanes rotate freely.
ADJUSTING THE PRV
After the PRV assembly has been reassembled the op-
eration of the vanes should be checked.
1. With the vanes in the closed position the insert pin
pointer should be pointing to “C” on the shaft cover.
A. If the vanes are not closed with the insert pin
pointer on “C”, adjust the linkage.
B. All vanes should be closed, if not, loosen the
hex head cap screw that holds the vane(s) in
place. Move the vane until it is fully closed,
then tighten and torque screws properly.
2. Use the lever to move the vanes to the open posi-
tion “O” stamped on the PRV shaft cover. All
vanes should be fully open. (Early 26" and 38"
compressor have an “R” stamping on the cover.)
With the lever move the pointer to “R”, at this
point the vanes should be approximately 20° be-
yond fully open position.
3. If all positions are not correct, readjust the vanes in
the closed position and recheck as previously men-
tioned. Make sure the linkage is properly tightened
and is moving freely.
4. PRV actuators (usually air operated Conomotors),
come in two basic configurations; direct and reverse
acting. Direct acting has the actuator shaft retracted
at minimum actuating air. Reverse acting has it fully
extended at minimum air. The external lever clamped
to the control shaft has two fulcrum points, upper
and lower. Depending on how the actuator is mounted
on the PRV housing, either style may be supplied.
Some units are still supplied with the optional hand
wheel and linkage for manual operation.
5. Set the vane indicator pin to the “C” mark with the
vanes fully closed. Some applications may require the
actuator stroke to hold the pin about 3/32" open at
minimum actuating air. This will hold the vanes open
slightly at all times and ease start-up. This will also
increase the in rush demand on the driving hardware.
REMOVING SHAFT AND IMPELLER LABYRINTH
SEALS
Two piece labyrinth shaft seals (See Fig. 31) are lo-
cated in the exit plate on the high pressure side of the
diffuser to minimize gas leakage along the shaft. The
first stage diffuser is equipped with a one piece impel-
ler eye labyrinth seal to prevent the discharge gas of
the first stage from leaking back into the inlet of the
first stage wheel. Each successive stage impeller inlet
eye seal is of two piece construction and is keyed into a
matching groove in the diffuser inlet entrance plate. They
are kept from rotating by means of a locating disk. (Fig.
4B, Item 74.) Install these disks in the notch during re-
assembly, because it is impossible to disassemble the
diffuser if the seals should rotate. Some compressors
may have up to eight stages, but additional stages all
follow the same pattern of construction. If it becomes
necessary to remove the top half of the compressor to
replace the labyrinth seals or work on the rotor, refer to
Figs. 29, 30, and 31 and proceed as follows:
It may be necessary to loosen or back
off on the compressor hold down bolts
before removing the top half. Failure
to do so may result in elevated cross-
foot stresses which may cause prob-
lems during reassembly. The flat foot
plane should be checked and bolts
retorqued after reassembly has been
completed.
Removing Top Half of Compressor Casing
Refer to Preparation for Service. Lockout/tagout main
motor on driver. Remove unit charge and drain the oil.
(See Refrigerant Transfer Unit and Pump Out Receiver,
Form 160.71-NM3.) Make sure main and control power
are OFF. Remove the compressor suction and discharge
piping. Remove the oil piping and tubing. Remove the
coupling guard and open the coupling. (Refer to Re-
4
Summary of Contents for Turbomaster M Series
Page 15: ...FORM 220 11 NM2 602 15 YORK INTERNATIONAL FIG 3 TYPICAL PRIMARY COMPRESSOR GAS FLOW LD07318 3 ...
Page 16: ...YORK INTERNATIONAL 16 FORM 220 11 NM2 602 FIG 4A MAJOR COMPONENTS LD07319 Operation ...
Page 31: ...FORM 220 11 NM2 602 31 YORK INTERNATIONAL Operation 3 This page intentionally left blank ...